Empty spate ust be filled
Page 52
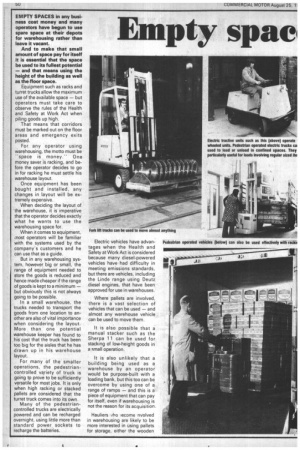
Page 53
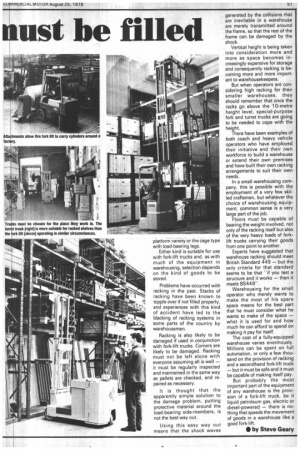
If you've noticed an error in this article please click here to report it so we can fix it.
EMPTY SPACES in any business cost money and many operators have begun to use spare space at their depots for warehousing rather than leave it vacant.
And to make that small amount of space pay for itself it is essential that the space be used to its fullest potential — and that means using the height of the building as well as thelloor space.
Equipment such as racks and turret trucks allow the maximum use of the available space — but operators must take care to observe the rules of the Health and Safety at Work Act when piling goods up high.
That means that corridors must be marked out on the floor areas and emergency exits posted.
For any operator using warehousing, the motto must be "space is money." One money saver is racking, and before the operator decides to go in for racking he must settle his warehouse layout.
Once equipment has been bought and installed, any changes in layout will be extremely expensive.
When deciding the layout of the warehouse, it is imperative that the operator decides exactly what he wants to use the warehousing space for.
When it comes to equipment, most operators will be familiar with the systems used by the company's customers and he can use that as a guide.
But in any warehousing systern, however big or small, the range of equipment needed to store the goods is reduced and hence made cheaper if the range of goods is kept to a minimum — but obviously this is not always going to be possible.
In a small warehouse, the trucks needed to transport the goods from one location to another are also of vital importance when considering the layout.
More than one potential warehouse keeper has found to . his cost that the truck has been too big for the aisles that he has drawn up in his warehouse layout.
For many of the smaller operations, the pedestrian controlled variety of truck is going tp prove to be sufficiently versatile for most jobs. It is only when high racking or stacked pallets are considered that the turret truck comes into its own.
Many of the pedestriancontrolled trucks are electrically powered and can be recharged overnight, using little more than standard power sockets to recharge the batteries. Electric vehicles have advantages when the Health and Safety at Work Act is considered because many diesel-powered vehicles have had difficulty in meeting emissions standards, but there are vehicles, including the Linde range using Deutz diesel engines, that have been approved for use in warehouses.
Where pallets are involved, there is a vast selection of vehicles that can be used — and almost any warehouse vehicle can be used to move them.
It is also possible that a manual stacker such as the Sherpa 1 1 can be used for stacking of low-height goods in a small operation.
It is also unlikely that a building being used as a warehouse by an operator would be purpose-built with a loading bank, but this too can be overcome by using one of a range of ramps — and this is a piece of equipment that can pay for itself, even if warehousing is not the reason for its acquisition.
Hauliers vho ecome nvolved in warehousing are likely to be more interested in using pallets for storage, either the wooden
platform vir-ietyor the cage type with load-bearing legs.
Either kind is suitable for use with fork-lift trucks and, as with much of the equipment in warehousing, selection depends on the kind of goods to be stored.
Problems have occurred with racking in the past. Stacks of racking have been known to topple over if not filled properly, and experiences with this kind of accident have led to the blacking of racking systems in some parts of the country by warehousemen.
Racking is also likely to be damaged if used in conjunction with fork-lift trucks. Corners are likely to be damaged Racking must not be left alone with everyone assuming all is well — it must be regularly inspected and maintained in the same way as pallets are checked, and repaired as necessary.
It is thought that the apparently simple solution to the damage problem, putting protective material around the load-bearing side-members, is not the best way out.
Using this easy way out means that the shock waves generated by the collisions that are inevitable in a warehouse are merely transmitted around the frame, so that the rest of the . frame can be damaged by the shock.
Vertical height is being taken into consideration more and more as space becomes increasingly expensive for storage and consequently racking is becoming more and more important to warehousekeepers.
But when operators are considering high racking for their smaller warehouses, they should remember that once the racks go above the 10-metre height level, special-purpose fork and turret trucks are going to be needed to cope with the height.
There have been examples of both coach and heavy vehicle operators who have employed their initiative and their own workforce to build a warehouse or extend their own premises and have built their own racking arrangements to suit their own needs.
In a small warehousing company, this is possible with the employment of a very few skilled craftsmen, but whatever the choice of warehousing equipment, common sense is a very large part of the job.
Floors must be capable of bearing the weight involved, not only of the racking itself but also of the very heavy loads of forklift trucks carrying their goods from one point to another.
Experts have suggested that warehouse racking should meet British Standard 449 — but the only criteria for that standard seems to be that -if you test a structure and it works — then it meets BS449".
Warehousing for the small operator who merely wants to make the most of his spare space means for the best part that he must consider what he wants to make of the space — what it is used for and how much he can afford to spend on making it pay for itself.
The cost of a fully-equipped warehouse varies enormously. Millions can be spent on full automation, or only a few thousand on the provision of racking and a secondhand fork-lift truck — but it must be safe and it must be capable of making itself pay. But probably the most important part of the equipment
of any warehouse is the provision of a fork-lift truck, be it
liquid petroleum gas, electric or diesel-powered — there is no thing that speeds the movement of goods in a warehouse like a good fork-lift.
• by Steve Geary