THE 'JAKE BRAKE' ADDS SAFETY-AND PAYS FOR ITSELF IN REDUCED RE-LINE BILLS
Page 40
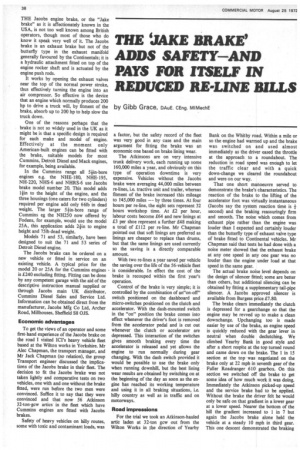
Page 41
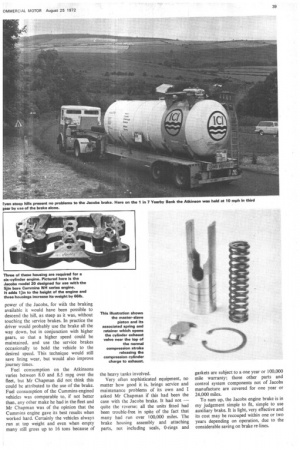
If you've noticed an error in this article please click here to report it so we can fix it.
by Gibb Grace, DAuE. CEng. M1MechE
THE Jacobs engine brake, or the "Jake brake" as it is affectionately known in the USA, is not too well known among British operators, though most of those who do know it speak very well of it. The Jacobs brake is an exhaust brake but not of the butterfly type in the exhaust manifold generally favoured by the Continentals; it is a hydraulic attachment fitted on top of the engine rocker shaft and is actuated by the engine push rods.
It works by opening the exhaust valves near the top of the normal power stroke, thus effectively turning the engine into an air compressor. So effective is the device that an engine which normally produces 200 hp to drive a truck will, by fitment of the brake, absorb up to 200 hp to help slow the truck down.
One of the reasons perhaps that the brake is not so widely used in the UK as it might be is that a specific design is required for each make and model of engine. Effectively at the moment only American-built engines can be fitted with the brake, suitable models for most Cummins, Detroit Diesel and Mack engines, for example, being available.
In the Cummins range all 5-11-in-bore engines e.g. the NHE-180, NHE-195, NH-220, NHS-6 and NHRS-6 use Jacobs brake model number 20. This model adds ilin to the height of the engine, and the three housings (one caters for two cylinders) required per engine add only 661b in dead weight. The larger 5+in-bore range of Cummins eg the NH250 now offered by Fodens, for example, would use the model
25A, this application adds to engine height and 751b dead weight.
Models 71 and 53, similarly, have been designed to suit the 71 and 53 series of Detroit Diesel engine.
The Jacobs brake can be ordered on a new vehicle or fitted in service on an existing vehicle. A typical price for the model 20 or 25A for the Cummins engines is E240 excluding fitting. Fitting can be done by any competent garage with the aid of the descriptive instruction manual supplied or through Jacobs main UK distributor, Cummins Diesel Sales and Service Ltd. Information can be obtained direct from the manufacturer, Jacobs Mfg Co Ltd, Archer Road, Millhouses, Sheffield S8 OJS.
Economic advantages To get the views of an operator and some first-hand experience of the Jacobs brake on the road I visited ICI's heavy vehicle fleet based at the Wilton works in Yorkshire. Mr Alec Chapman, the transport manager, and Mr Jack Chapman (no relation), the group Transport engineer discussed the implications of the Jacobs brake in their fleet. The decision to fit the Jacobs brake was not taken lightly and comparative tests on two vehicles, one with and one without the brake fitted, were run before the two men were convinced. Suffice it to say that they were convinced and that now 56 Atkinson 32-ton-gcw artics in the fleet which have Cummins engines are fitted with Jacobs brakes.
Safety of heavy vehicles on hilly routes, some with toxic and contaminant loads, was a factor, but the safety record of the fleet was very good in any case and the main argument for fitting the brake was an economic one based on brake lining wear.
The Atkinsons are on very intensive trunk delivery work, each running up some 160,000 miles a year, and obviously on this type of operation downtime is very expensive. Vehicles without the Jacobs brake were averaging 44,000 miles between re-lines, i.e. tractive unit and trailer, whereas fitment of the brake increased this mileage to 145,000 miles -by three times. At four hours per re-line, the eight sets represent 32 hours workshop time. At £2 per hour, labour costs become £64 and new linings at £3 per shoe represent a further £48 making a total of £112 per re-line. Mr Chapman pointed out that soft linings are preferred as linings are cheaper to replace than drums, but that the same linings are used currently so the saving is a directly comparable amount.
With two re-lines a year saved per vehicle the saving over the life of the 56-vehicle fleet is considerable. In effect the cost of the brake is recouped within the first year's operation.
Control of the brake is very simple; it is controlled by the combination of an"on-off' switch positioned on the dashboard and micro-switches positioned on the clutch and accelerator. With the dash-mounted switch in the "on" position the brake comes into effect whenever the driver's foot is removed from the accelerator pedal and is cut out whenever the clutch or accelerator are depressed. This interaction of the switches gives smooth braking every time the accelerator is released and yet allows the engine to run normally during gear changing. With the dash switch provided it would be possible to use the brake only when running downhill, but the best lining wear results are obtained by switching on at the beginning of the day as soon as the engine has reached its working temperature and using it in all braking situations, i.e. hilly country as well as in traffic and on motorways.
Road impressions For the trial we took an Atkinson-hauled attic laden at 32-ton gcw out from the Wilton Works in the direction of Yearby Bank on the Whitby road. Within a mile or so the engine had warmed up and the brake was switched on and used almost immediately as the driver eased the throttle at the approach to a roundabout. The reduction in road speed was eno.ugh to let the traffic clear and with a quick down-change we cleared the roundabout and were on our way.
That one short manoeuvre served to demonstrate the brake's characteristics. The reaction of the brake to the lifting of the accelerator foot was virtually instantaneous (Jacobs say the system reaction time is + second) and the braking reassuringly firm and smooth. The noise which comes from exhaust pipe rather than the engine was louder than I expected and certainly louder than the butterfly type of exhaust valve type of brake fitted to Continental vehicles. Mr Chapman said that tests he had done with a noise meter showed that the exhaust brake at any one speed in any one gear was no louder than the engine under load at that speed in the same gear.
The actual brake noise level depends on the design of silencer fitted; some are better than others, but additional silencing can be obtained by fitting a supplementary tail-pipe silencer. A Jacobs approved silencer is available from Burgess price £7.80.
The brake clears immediately the clutch is depressed for a gearchange so that the engine may be revved up to make a clean downchange. Upchanging too is made easier by use of the brake, as engine speed is quickly reduced with the gear lever in neutral when double declutching. We climbed Yearby Bank in good style and after a short respite at the top turned round and came down on the brake. The 1 in 15 section at the top was negotiated on the brake only at 22 mph in seventh gear of the Fuller Roadranger 610 gearbox. On this section we switched off the brake to get some idea of how much work it was doing. Immediately the Atkinson picked-up speed and the service brake had to be applied. Without the brake the driver felt he would only be safe on that gradient in a lower gear at a lower speed. Nearer the bottom of the hill the gradient increased to 1 in 7 but again the Jacobs brake alone held the vehicle at a steady 10 mph in third gear. This one descent demonstrated the braking power of the Jacobs, for with the braking available it would have been possible to descend the hill, as steep as it was, without touching the service brakes. In practice the driver would probably use the brake all the way down, but in conjunction with higher gears, so that a higher speed could be maintained, and use the service brakes occasionally to hold the vehicle to the desired speed. This technique would still save lining wear, but would also improve journey times.
Fuel consumption on the Atkinsons varies between 8.0 and 8.5 mpg over the fleet, but Mr Chapman did not think this could be attributed to the use of the brake. Fuel consumption of the Cummins-engined vehicles was comparable to, if not better than, any other make he had in the fleet and Mr Chapman was of the opinion that the Cummins engine gave its best results when worked hard. Certainly the vehicles always run at top weight and even when empty many still gross up to 16 tons because of the heavy tanks involved.
Very often sophisticated equipment, no matter how good it is, brings service and maintenance problems of its own and I asked Mr Chapman if this had been the case with the Jacobs brake. It had not — quite the reverse; all the units fitted had been trouble-free in spite of the fact that many had run over 100,000 miles. The brake housing assembly and attaching parts, not including seals, 0-rings and gaskets are subject to a one year or 100,000 mile warranty; those other parts and control system components not of Jacobs manufacture are covered for one year or 24,000 miles.
To sum up, the Jacobs engine brake is in my judgement simple to fit, simple to use auxiliary brake. It is light, very effective and its cost may be recouped within one or two years depending on operation, due to the considerable saving on brake re-lines.