TESTING THE TESTERS
Page 38
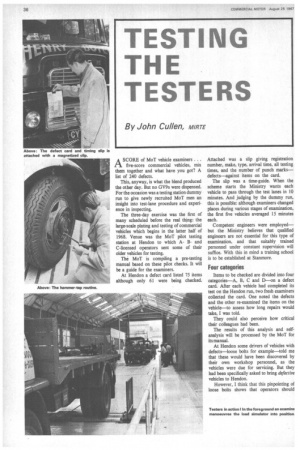
Page 39
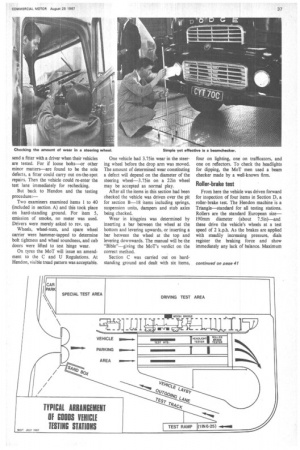
Page 43
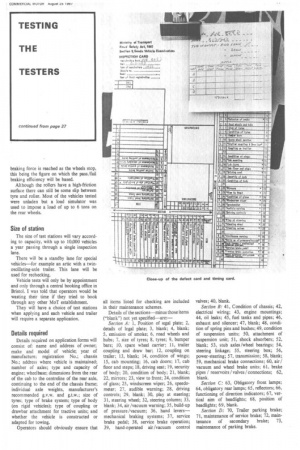
If you've noticed an error in this article please click here to report it so we can fix it.
By John Cullen, MIRTE ASCORE of MoT vehicle examiners . . . five-score commercial vehicles, mix them together and what have you got? A list of 240 defects.
This, anyway, is what the blend produced the other day. But no GV9s were dispensed. For the occasion was a testing station dummy run to give newly recruited MoT men an insight into test-lane procedure and experience in inspecting.
The three-day exercise was the first of many scheduled before the real thing: the large-scale plating and testing of commercial vehicles which begins in the latter half of 1968. Venue was the MoT pilot testing station at Hendon to which ABand C-licensed operators sent some of their older vehicles for testing.
The MoT is compiling a pre-testing manual based on these pilot checks. It will be a guide for the examiners.
At Hendon a defect card listed 75 items although only 61 were being checked. Attached was a slip giving registration number, make, type, arrival time, all testing times, and the number of punch marksdefects—against items on the card.
The slip was a time-guide. When the scheme starts the Ministry wants each vehicle to pass through the test lanes in 10 minutes. And judging by the dummy run, this is possible: although examiners changed places during various stages of examination, the first five vehicles averaged 15 minutes each.
Competent engineers were employed— but the Ministry believes that qualified engineers are not essential for this type of examination, and that suitably trained personnel under constant supervision will suffice. With this in mind a training school is to be established at Stanmore.
Four categories Items to be checked are divided into four categories—A, B, C and D—on a defect card. After each vehicle had completed its test on the Hendon run, two fresh examiners collected the card. One noted the defects and the other re-examined the items on the vehicle—to assess how long repairs would take, I was told.
They could also perceive how critical their colleagues had been.
The results of this analysis and selfanalysis will be processed by the MoT for its manual.
At Hendon some drivers of vehicles with defects—loose bolts for example—told me that these would have been discovered by their own workshop personnel, as the vehicles were due for servicing. But they had been specifically asked to bring defective vehicles to Hendon.
However, I think that this pinpointing of loose bolts shows that operators should send a fitter with a driver when their vehicles are tested. For if loose bolts—or other minor matters—are found to be the sole defects, a fitter could carry out on-the-spot repairs. Then the vehicle could re-enter the test lane immediately for rechecking.
But back to Hendon and the testing procedure:—
Two examiners examined items 1 to 40 (included in section. A) and this took place on hard-standing ground. For item 5, emission of smoke, no meter was used. Drivers were merely asked to rev. up.
Wheels, wheel-nuts, and spare wheel carrier were hammer-tapped to determine bolt tightness and wheel soundness, and cab doors were lifted to test hinge wear.
On tyres the MoT will issue an amendment to the C and U Regulations. At Hendon, visible tread pattern was acceptable. One vehicle had 3.75in wear in the steering wheel before the drop arm was moved. The amount of determined wear constituting a defect will depend on the diameter of the steering wheel-3.75in on a 22in wheel may be accepted as normal play.
After all the items in this section had been checked the vehicle was driven over the pit for section B-18 items including springs, suspension units, dampers and stub axles being checked.
Wear in kingpins was determined by inserting a bar between the wheel at the bottom and levering upwards, or inserting a bar between the wheel at the top and levering downwards. The manual will be the "Bible"—giving the MoT's verdict on the correct method.
Section C was carried out on hardstanding ground and dealt with six items, four on lighting, one on trafficators, and one on reflectors. To check the headlights for dipping, the MoT men used a beam checker made by a well-known firm.
Roller-brake test
From here the vehicle was driven forward for inspection of four items in Section D, a roller-brake test. The Hendon machine is a Triangle—standard for all testing stations. Rollers are the standard European size190mm diameter (about 7.5in)—and these drive the vehicle's wheels at a test speed of 2 k.p.h. As the brakes are applied with steadily increasing pressure, dials register the braking force and show immediately any lack of balance. Maximum braking force is reached as the wheels stop, this being the figure on which the pass /fail braking efficiency will be based.
Although the rollers have a high-friction surface there can still be some slip between tyre and roller. Most of the vehicles tested were unladen but a load simulator was used to impose a load of up to 6 tons on the rear wheels.
Size of statinn
The size of test stations will vary according to capacity, with up to 10,000 vehicles a year passing through a single inspection lane.
There will be a standby lane for special vehicles-for example an artic with a twinoscillating-axle trailer. This lane will be used for rechecking.
Vehicle tests will only be by appointment and only through a central booking office in Bristol. I was told that operators would be wasting their time if they tried to book through any other MoT establishment.
They will have a choice of test stations when applying and each vehicle and trailer will require a separate application.
Details required
Details required on application forms will consist of: name and address of owner; make and model of vehicle; year of manufacture; registration No.; chassis No.; address where vehicle is maintained; number of axles; type and capacity of engine; wheelbase; dimensions from the rear of the cab to the centreline of the rear axle, continuing to the end of the chassis frame; individual axle weights, manufacturer's recommended g.v.w. and g.t.w.; size of tyres; type of brake system; type of body (on rigid vehicles); type of coupling or drawbar attachment for tractive units; and whether the vehicle is constructed or adapted for towing.
Operators should obviously ensure that all items listed for checking are included in their maintenance schemes.
Details of the sections-minus those items ("blank") not yet specified-are:
Section A: 1, Position of legal plate; 2, details of legal plate; 3, blank; 4, blank; 5, emission of smoke; 6, road wheels and hubs; 7, size of tyres; 8, tyres; 9, bumper bars; 10. spare wheel carrier; 11, trailer coupling and draw bar; 12, coupling on trailer; 13, blank; 14, condition of wings; 15, cab mounting; 16, cab doors; 17, cab floor and steps; 18, driving seat; 19, security of body; 20, condition of body; 21, blank; 22, mirrors; 23, view to front; 24, condition of glass; 25, windscreen wiper; 26, speedometer; 27, audible warning; 28, driving controls; 29, blank; 30, play at steering; 31, steering wheel; 32, steering column; 33, blank; 34, air /vacuum warning; 15, build-up of pressure/vacuum; 36, hand leversmechanical braking systems; 37, service brake pedal; 38, service brake operation; 39, hand-operated air/vacuum control
valves; 40, blank.
Section B: 41, Condition of chassis; 42, electrical wiring; 43, engine mountings; 44, oil leaks; 45, fuel tanks and pipes; 46, exhaust and silencer; 47, blank; 48, condition of spring pins and bushes; 49, condition of suspension units; 50, attachment of suspension unit; 51, shock absorbers; 52, blank; 53, stub axles/wheel bearings; 54, steering linkage; 55, steering box; 56, power-steering; 57, transmission; 58, blank; 59, mechanical brake connections; 60, air/ vacuum and wheel brake units; 61, brake pipes / reservoirs / valves /connections; 62, blank.
Section C: 63, Obligatory front lamps; 64, obligatory rear lamps; 65, reflectors; 66, functioning of direction indicators; 67, vertical aim of headlights; 68, position of headlights; 69, blank.
Section D: 70, Trailer parking brake; 71, maintenance of service brake; 72, maintenance of secondary brake; 73, maintenance of parking brake.