Hoist Loaded Contain Cut Distribution Costs
Page 58
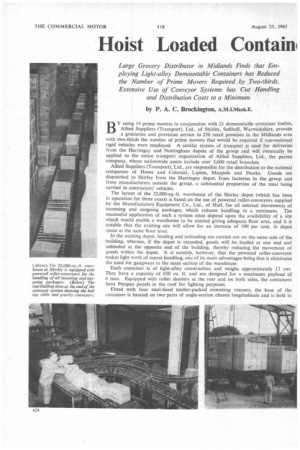
Page 59
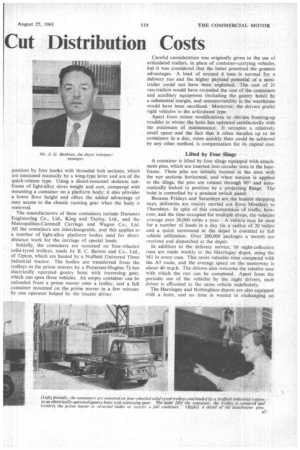
Page 60
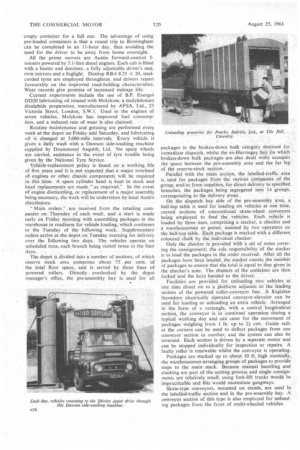
If you've noticed an error in this article please click here to report it so we can fix it.
Large Grocery Distributor in Midlands Finds that Employing Light-alloy Demountable Containers has Reduced the Number of Prime Movers Required by Two-thirds. Extensive Use of Conveyor Systems has Cut Handling and Distribution Costs to a Minimum by P. A. C. Brockington,
BY using 14 prime movers in conjunction with 21 demountable container bodies, Allied Suppliers (Transport), Ltd., of Shirley, Solihull, Warwickshire, provide. a grocieries and provision service to 250 retail premises in the Midlands area with two-thirds the number of prime movers that would be required if conventional rigid vehicles were employed. A similar system of transport is used for deliveries from the Harringay and Nottingham depots of the group and will eventually be applied to the entire transport organization of Allied Suppliers, Ltd., the parent company, whose nationwide assets include over 3,000 retail branches.
Allied Suppliers (Transport), Ltd., are responsible for the distribution to the national companies of Home and Colonial, Lipton, Maypole and Pearks. Goods are dispatched to Shirley from the Harringay depot, from factories in the group and from manufacturers outside the group, a substantial proportion of the total being carried in contractors' vehicles.
The layout of the 22,000-sq.-ft. warehouse of the Shirley depot (which has been in operation for three years) is based on the use of powered roller-conveyors supplied by the Manufacturers Equipment Co., Ltd., of Hull, for all internal movements of incoming and outgoing packages, which reduces handling to a minimum. The successful application of such a system must depend upon the availability of a site which would enable a warehouse to be erected giving adequate floor area, and it is notable that the existing site will allow for an increase of 100 per cent, in depot space at the same floor level.
In the existing depot, loading and unloading are carried out on the same side of the building, whereas, if the depot is extended, goods will be loaded at one end and unloaded at the opposite end of the building, thereby reducing the movement of goods within the depot. It is notable, however, that the powered roller-conveyor makes light work of repeat handling, one of its main advantages being that it eliminates the need for gangways in the main section of the warehouse.
Each container is of light-alloy construction and weighs approximately 13 cwt. They have a capacity of 650 cu. ft. and are designed for a maximum payload of 6 tons. Equipped with roller shutters at the rear and on both sides, the containers have Perspex panels in the roof for lighting purposes.
Fitted with four steel-lined timber-packed mounting runners, the base of the container is located on two pairs of angle-section chassis longitudinals and is held in position by four hooks with threaded bolt sections, yihich are tensioned manually by a wing-type lever and are of the quick-release type. Using a direct-mounted skeleton subframe of light-alloy saves weight and cost, compared with mounting a container on a platform body; it also peovides a lower floor height and offers the added advantage of easy access to the chassis running gear when the body is removed.
The manufacturers of these containers include Duramin Engineering Co., Ltd., King and Tayloy, Ltd., and the Metropolitan-Cammell Carriage and Wagon Co., Ltd. All the containers are interchangeable, and this applies to a number of light-alloy platform bodies used for shortdistance work for the carriage of special loads.
Initially, the containers are mounted on four-wheeled solid-tyred trolleys, made by B. C. Barton and Co., Ltd., of Tipton, which are hauled by a Nuffield Universal Three industrial tractor. The bodies are transferred from the trolleys to the prime movers by a Patterson-Hughes 74-ton electrically operated gantry hoist with traversing gear, which can span three vehicles. An empty contalner can be unloaded from a prime mover onto a trolley, and a full container mounted on the prime mover in a few minutes by one operator helped by the tractor driver.
Careful consideration was originally given to the use of articulated trailers, in place of container-carrying vehicles, but it was considered that the latter promised-the greatest advantages. A load of around 6 tons is normal for a delivery run and the higher payload potential of a semitrailer could not have been exploited. The cost of 21 van-trailers would have exceeded the cost of the containers and auxiliary equipment (including the gantry hoist) by a substantial margin, and manceuvrability in the warehouse would have been sacrificed. Moreover; the drivers prefer rigid vehicles to the articulated type.
Apart from minor modifications to obviate frosting-up troubles in winter the hoist has operated satisfactorily with the minimum of maintenance. It occupies a relatively small space and the fact that it often handles up to 60 containers in a day, more quickly than could be achieved by any other method, is compensation for its capital cost.
Lifted by Four Slings A container is lifted by four slings equipped with attachment pins, which are inserted into circular slots in the baseframe. These pins are initially located in the slots with the eye sections horizontal, and when tension is applied to the slings, the pins are rotated 'through 90°and automatically locked in position by a projecting flange. The hoist is controlled by a pendant switch panel.
Because Fridays and Saturdays are the busiest shopping days, deliveries are mainly carried out from Mondays to Thursdays. In spite of this concentration of traffic, however, and the time occupied for multiple drops, the vehicles average over 20,000 miles a year. A vehicle may be used for a number of loads in a day (in a radius of 20 miles) and a quick turnround at the depot is essential to full vehicle utilization. Over 200,000 packages a month are received and dispatched at the depot.
In addition to the delivery service, 10 night-collection runs are made weekly to the Harringay depot, using the M1 in every case. This saves valuable time compared with the A5 route, and the average speed on the motorway is about 40 m.p.h. The drivers also welcome the relative ease with which the run can be completed. Apart from the periodic use of the vehicles by the night drivers, each driver is allocated to the same vehicle indefinitely.
The Harringay and Nottingham depots are also equipped with a hoist, and no time is wasted in exchanging an empty container for a full one. The advantage of using pre-loaded containers is that a round trip to Birmingham can be completed in an 11-hour day, thus avoiding the need for the driver to be away from home overnight.
All the prime movers are Austin forward-control 5tonners powered by 5.1-litre diesel engines. Each cab is fitted with a heater and demister, a fully adjustable driver's seat. twin mirrors and a foglight. Dunlop RB.6 8.25 X 20, steelcorded tyres are employed throughout, and drivers report favourably on the improved road-holding characteristics. Wear records give promise of increased mileage life.
Current experiments include the use of B.P. Energol DD20 lubricating oil treated with Molykote, a molybdenum disulphide preparation, -manufactured by AFSA, Ltd., 25 Victoria Street, London, S.W.1. Used in the engines of seven vehicles, Molykote has improved fuel consump
tion, and a reduced rate of wear is also claimed. -
Routine maintenance and greasing are performed every week, at-the depot:on Friday 'and Saturday, and lubricating oil is changed at 3.000-mile intervals. Every, vehicle is given a daily wash with a Dawson side--washing machine supplied by Drummond Asquith, Ltd. No spare wheels arc carried, assistance in the event of tyre trouble being given by the National Tyre Service.
• Vehicle-replacement policy is based on a working life of 'five years and it is not expected that a major overhaul of engines or other chassis components: Will be required in this Itime..'A spare cylinder head is kept in stock and head replacements are made "as required." In the event of engine dismantling, or replacement of a major assembly being necessary, the work will be undertaken by local Austin distributors.
" Main orders are received from the retailing companies on Thursday' of each, week, and a 'start is made early on Friday morning with assembling packages in the warehouse in readiness for vehieleloading, which continues to the Tuesday of the following ..week.Supplementary orders arrive at the depot on Tuesday morning for delivery over the following two .days. The vehicles operate on scheduled runt, each branch being visited twice in the four
days. . • The depot is divided into a number of sections, of which reserve stock area comprises .about: 75 , per cent, of the total floor' space, and is served by three lines of powered rollers. Directly overlooked by the depot manager's office, the pre-assembly bay is used for all packages in the broken-down bulk category destined for immediate dispatch, whilst the ex-Harringay baY (in which broken-down bulk packages are also dealt with) occupies . the space between the pre-assembly area and the far leg of the reserve-stock section.• , • .
Parallel with the main section, the labelled-traffic. area .
is used for packages from the various companies of the group, and/or from suppliers, for direct delivery to specified branches, the packages being Segregated into 14 grobPs, corresponding to the delivery area.i... • •
• On the dispatch bay side of the pre-assembly area, a ball-top fable is used for loading six vehicles at one curved sections of conventional -slcate-wh.eel conveyors being employed to feed • the' .vehicles. Each .vehicle is loaded by three:men, comprising-a 'stacker, a checker and a warehouseman or porter, assisted .by two operators on the ball-top table. Fad' package is marked with a different coloured-chalk by the individual checker. .
Only the checker is provided with a .set of notes covering the consignment; the Sole reSpOnsibility of. the stacker is to load the packages in the order received.'After all the packages have been loaded, the stacker counts the number of packages to ensure that the total itS•equal to that given in the checker's note. The .shutters of the container are then
locked and the keys banded to the driver. •
Facilities . are provided, for Unloading two vehicles at one time direct on to a -Platform adjacent to the leading section of the powered roller-conveyor, line. A Rapistan Stevedore electrically operated conveyor-elevator cart be used for loading or unloading an extra vehicle. Arranged in the form of a. rectangle, with a central 'longitudinal section, the conveyor is in continual operation during a typical working day and can cater for the movement of packages weighing from 1 lb. up to 24cwt. Guide rails at the corners can be used to deflect packages from one conveyor section to another, and the system can also be reversed. Each section is driven by a separate motor and can be stopped individually for inspection or repairs. A faulty roller is renewable whilst the conveyor is operating.
Packages are stacked up to about 10 ft. high manually, the warehousemen arranging groups of packages to provide steps to the main stack. Because manual handling and stacking arc part of the sorting process and single consignments are relatively small, using fork-lift trucks would be impracticable and this would necessitate gangways. Skate-type conveyors, mounted on stands, are used in the labelled-traffic section and in the pre-assembly bay. A conveyor section of this type is also employed for unloading packages from the front of multi-wheeled vehicles.