Tool up for profit
Page 117
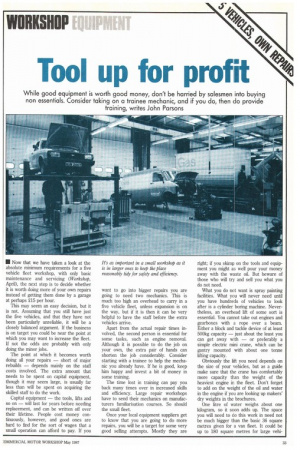
Page 118
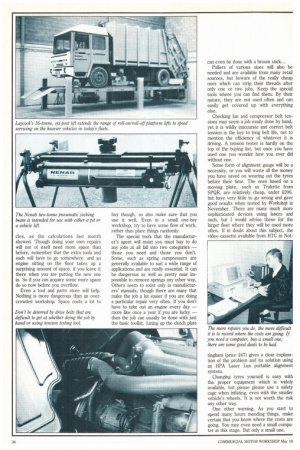
If you've noticed an error in this article please click here to report it so we can fix it.
While good equipment is worth good money, don't be harried by salesmen into buying non essentials. Consider taking on a trainee mechanic, and if you do, then do provide training, writes John Parsons
• Now that we have taken a look at the absolute minimum requirements for a five vehicle fleet workshop, with only basic maintenance and servicing (Workshop. April), the next step is to decide whether it is worth doing more of your own repairs instead of getting them done by a garage at perhaps £15 per hour.
This may seem an easy decision, but it is not. Assuming that you still have just the five vehicles, and that they have not been particularly unreliable, it will be a closely balanced argument. If the business is on target you could be near the point at which you may want to increase the fleet. If not the odds are probably with only doing the minor jobs.
The point at which it becomes worth doing all your repairs — short of major rebuilds — depends mainly on the staff costs involved. The extra amount that needs to be spent on capital equipment, though it may seem large, is usually far less than will be spent on acquiring the skilled staff to do the work.
Capital equipment — the tools, lifts and so on — will last for years before needing replacement, and can be written off over their lifetime. People cost money continuously, however, and good ones are hard to find for the sort of wages that a small operation can afford to pay. If you want to go into bigger repairs you are going to need two mechanics. This is much too high an overhead to carry in a five vehicle fleet, unless expansion is on the way, but if it is then it can be very helpful to have the staff before the extra vehicles arrive.
Apart from the actual repair times involved, the second person is essential for some tasks, such as engine removal. Although it is possible to do the job on your own, the extra pair of hands can shorten the job considerably. Consider starting with a trainee to help the mechanic you already have. If he is good, keep him happy and invest a bit of money in Some training.
The time lost in training can pay you back many times over in increased skills and efficiency. Large repair workshops have to send their mechanics on manufacturers familiarisation courses. So should the small fleet.
Once your local equipment suppliers get to know that you are going to do more repairs, you will be a target for some very good selling attempts. Mostly they are right; if you skimp on the tools and equipment you might as well pour your money away with the waste oil. But beware of those who will try and sell you what you do not need.
What you do not want is spray painting facilities. What you will never need until you have hundreds of vehicles to look after is a cylinder boring machine. Nevertheless, an overhead lift of some sort is essential. You cannot take out engines and gearboxes with a rope over a beam. Either a block and tackle device of at least 500kg capacity — just about the least you can get away with — or preferably a simple electric mini crane, which can be gantry mounted with about one tonne lifting capacity.
Obviously the lift you need depends on the size of your vehicles, but as a guide make sure that the crane has comfortably more capacity than the weight of the heaviest engine in the fleet. Don't forget to add on the weight of the oil and water in the engine if you are looking up makers' dry weights in the brochures.
One litre of water weighs about one kilogram, so it soon adds up. The space you will need to do this work in need not be much bigger than the basic 36 square metres given for a van fleet. It could be up to 180 square metres for large vehi cies, as the calculations last month showed. Though doing your own repairs will not of itself need more space than before, remember that the extra tools and such will have to go somewhere, and an engine sitting on the floor takes up a surprising amount of space, if you leave it there when you are putting the new one in. So if you can acquire some more space do so now before you overflow.
Even a tool and parts store will help. Nothing is more dangerous than an overcrowded workshop. Space costs a lot to buy though, so also make sure that you use it well. Even in a small one-bay workshop, try to have some flow of work, rather than place things randomly.
The special tools that the manufacturer's agent will insist you must buy to do any jobs at all fall into two categories — those you need and those you don't. Some, such as spring compressors are generally available to suit a wide range of applications and are really essential. It can be dangerous as well as pretty near impossible to remove springs any other way. Others seem to exist only in manufacturers' manuals, though there are many that make the job a lot easier if you are doing a particular repair very often. If you don't have to take out an engine every day — more like once a year if you are lucky — then the job can usually be done with just the basic toolkit. Lining up the clutch plate can even be done with a broom stick...
Pullers of various sizes will also be needed and are available from many retail sources, but beware of the really cheap ones which can strip their threads after only one or two jobs. Keep the special tools where you can find them. By their nature, they are not used often and can easily get covered up with everything else.
Checking fan and compressor belt tensions may seem a job easily done by hand, yet it is wildly inaccurate and correct belt tension is the key to long belt life, not to mention the efficiency of whatever it is driving. A tension tester is hardly on the top of the buying list, but once you have used one you wonder how you ever did without one.
Some form of alignment gauge will be a necessity, or you will waste all the money you have saved on wearing out the tyres before their time. The ones based on a moving plate, such as Trakrite from SPQR, are relatively cheap, under £200, but have very little to go wrong and gave good results when tested by Workshop in November. There are many much more sophisticated devices using lasers and such, but I would advise these for the larger fleet where they will be used more often. If in doubt about this subject, the video cassette available from HTC in Not tingham (price £47) gives a clear explanation of the problem and its solution using an HPA Laser Lux portable alignment system.
Changing tyres yourself is easy with the proper equipment which is widely available, but please please use a safety cage when inflating, even with the smaller vehicle's wheels. It is not worth the risk any other way.
One other warning. As you start to spend many hours mending things, make certain that you know where the costs are going. You may even need a small computer at this stage. But only a small one.