Operational economies during inflation
Page 45
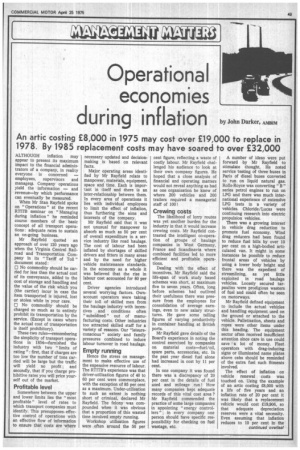
Page 46
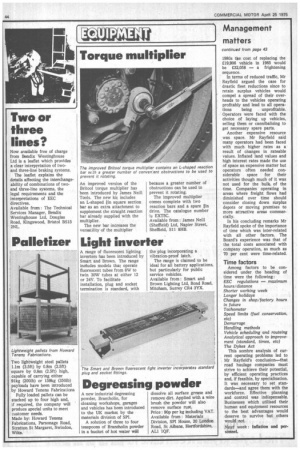
If you've noticed an error in this article please click here to report it so we can fix it.
An artic costing £8,000 in 1975 may cost over £19,000 to replace in 1978. By 1985 replacement costs may have soared to over £32,000
ALTHOUGH inflation may appear to present its maximum impact to the financial administrators of a company, in reality everyone is concerned — employees, supervisors and managers. Company operations yield the information — and revenue—by which performance can eventually be measured.
When Mr Stan Rayfield spoke on " Operations " at the recent RTITB seminar on "Managing during inflation" he reminded course members of the basic concept of all transport operations: adequate rates to sustain an on-going business.
Mr Rayfield quoted an approach of over 120 years ago when the Virginia Central Railroad and Transportation Company in its "Tariff of Toll " document stated: 1:1 No commodity should be carried for less than the actual cost of its conveyance, added to the cost of storage and handling and the value of the risk which you (the carrier) incur in case the item transported is injured, lost or stolen while in your care.
o No commodity should be charged so much as to entirely prohibit its transportation by the service. (Except in cases where the actual cost of transportation is itself prohibitory).
These two rules—remembering the simplicity of transport operations in 1854—furnished the industry with two "limits of rating " : first, that if charges are too low the number of tons carried will be large but the traffic will yield no profit ; and secondly, that if you charge prohibitive rates you will price yourself out of the market.
Profitable level
Somewhere between the upper and lower limits lies the "most profitable" level of rates to which transport companies must identify. This presupposes effective control of operations with an effective flow of information to ensure that costs are where necessary updated and decisionmaking is based on relevant facts.
Major operating areas identified by Mr Rayfield relate to manpower, materials, equipment, space and time. Each is important in itself and there is an inter-relationship between them. In every area of operations it lies with individual employees to limit the effect of inflation, thus furthering the aims and interests of the company.
Mr Rayfield said that it was not unusual for manpower to absorb as much as 50 per cent of overall expenditure in a service industry like road haulage. The cost of labour had been inflated by shortages of skilled drivers and fitters in many areas and by the need for higher vehicle maintenance standards. In the economy as a whole it was believed that the rise in labour cost accounted for 80 per cent.
Driver agencies introduced several worrying factors. Ownaccount operators were taking their toll of skilled men from the haulage industry with incentives and conditions often " subsidised " out of manufacturing costs. Other industries too attracted skilled staff for a variety of reasons. Our "leisureconscious" society and family pressures combined to induce labour turnover in road haulage.
Empty running
Hence the stress on management to make effective use of the expensive resource of labour. The RTITB's experience was that driver-utilisation figures of 40 to 60 per cent were commonplace, with the exception of 85 per cent as a maximum. Under-utilisation to such an extent is nothing short of criminal, declared Mr Rayfield. The felony was compounded when it was obvious that a proportion of this wasted time involved empty running.
Workshop utilisation figures were often around the 50 per cent figure, reflecting a waste of costly labour. Mr Rayfield challenged his audience to look at their own company figures. He hoped that a close analysis of financial and operating matters would not reveal anything as bad as one organisation he knew of where 200 vehicles and 200 trailers required a managerial staff of 1001
Crewing costs
The likelihood of lorry routes was yet another burden for the industry in that it would increase crewing costs. Mr Rayfield contrasted the intelligent co-operation of groups of haulage companies in West Germany, France and Scandinavia where combined facilities led to more efficient and profitable operations.
Dealing with the effect of incentives, Mr Rayfield said the life-span of work study based schemes was short, at maximum five to seven years. Often, long before schemes had outlived their usefulness there was pressure from the employees for consolidation of average earnings, even to new salary structures. He gave some telling figures of varying productivity in container handling at British ports.
Mr Rayfield gave details of the Board's experience in noting the control exercised by companies on material costs—fuel/oil, spare parts, accessories, etc. In the past year diesel fuel alone had increased in cost by 11 per cent.
In one company it was found there was a discrepancy of 20 per cent in the details of fuel used and mileage run ! How many companies kept adequate records of this vital cost area ? Mr Rayfield commended the practice of some large companies in appointing "energy controllers" ; in every company one person should have specific responsibility for checking on fuel wastage, etc. A number of ideas were put forward by Mr Rayfield to stimulate thought. He noted service testing of three 'buses in Paris of diesel buses converted to run on liquid natural gas. Rolls-Royce was converting " B " series petrol engines to run on LPG and there was much international experience of extensive LPG tests in a variety of vehicles. Chloride/Lucas were continuing research into electric propulsion vehicles.
There was a growing interest in vehicle drag reduction to promote fuel economy. Wind drag reducers had been found to reduce fuel bills by over 10 per cent on a high-bodied articulated van. It might in some instances be possible to reduce frontal areas of vehicles by using a lower body height and there was the expedient of streamlining, as yet little exploited in road haulage vehicles. Loosely secured tarpaulins were prodigious wasters of fuel and could often be seen on motorways.
Mr Rayfield defined equipment to include the actual vehicles and handling equipment used on the ground or attached to the vehicle. Palletisation, sheets and ropes were other items under this heading. The equipment sector often received insufficient attention since care in use could save a lot of money. Fleet operators with drag-inducing signs or illuminated name plates above cabs should be reminded of the extra fuel such fitments involved.
The effect of inflation on vehicle renewal costs was touched on. Using the example of an artic costing £8,000 with a life of five years and an inflation rate of 20 per cent it was likely that a replacement vehicle would cost £19,906, so that adequate depreciation reserves were a vital necessity. Even assuming that inflation reduces to 10 per cent in the 1980s tlae cost of replacing the £19,906 vehicle in 1985 would be £32,058 — a frightening sequence.
In terms of reduced traffic, Mr Rayfield argued the case for drastic fleet reductions since to retain surplus vehicles would compel a spread of their overheads to the vehicles operating profitably and lead to all opera
tions being unprofitable. Operators were faced with the choice of laying up vehicles, selling them or cannibalising to get necessary spare parts.
Another expensive resource was space. Mr Rayfield said many operators had been faced with much higher rates as a result of changes in rateable values. Inflated land values and high interest rates made the use of space an expensive matter but operators often needed considerable space for their activities though much of it was not used for the bulk of the time. Companies operating in areas where freight flows had diminished over time should consider closing down surplus depots or moving premises to more attractive areas commercially.
In his concluding remarks Mr Rayfield spoke of the importance of time which was inter-related with all other factors. The Board's experience was that of the total costs associated with company operation, as much as 70 per cent were time-related.
Time factors
Among factors to be considered under the heading of time were the following:
EEC regulations — maximum hours/distance Shorter working week
Longer holidays
Changes in shop/factory hours in future
Tachometer
Speed limits (fuel conservation, etc)
Demurrage
Handling methods Vehicle scheduling and routeing Analytical approach to improvement (standard, times, etc) The Dykes Act
This sombre analysis of current operating problems led to Mr Rayfield's conclusion—that road haulage companies must strive to achieve their potential, by efficient operating practices and, if feasible, by specialisation. It was necessary to set standards—and agree them with the workforce. Effective planning and control was indispensable. Businesses which utilised their human and equipment resources to the best advantages would deserve to survive but others would not.
Next week: Inflation and personnel.