Feeling the pressure
Page 88
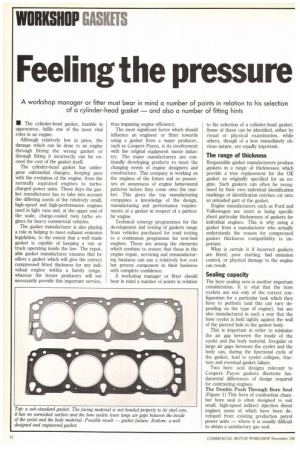
Page 89
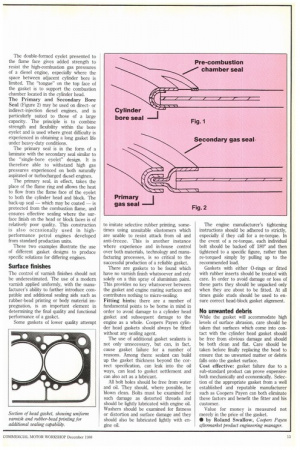
If you've noticed an error in this article please click here to report it so we can fix it.
A workshop manager or fitter must bear in mind a number of points in relation to his selection of a cylinder-head gasket — and also a number of fitting hints
• The cylinder-head gasket, humble in appearance, fulfils one of the most vital roles in an engine.
Although relatively low in price, the damage which can be done to an engine through fitting the wrong gasket or through fitting it incorrectly can far exceed the cost of the gasket itself.
The cylinder-head gasket has undergone substantial changes, keeping pace with the evolution of the engine, from the normally aspirated engines to turbocharged power units. These days the gasket manufacturer has to take into account the differing needs of the relatively small, high-speed and high-performance engines used in light vans and, at the upper end of the scale, charge-cooled twin turbo engines for heavy commercial vehicles.
The gasket manufacturer is also playing a role in helping to meet exhaust emission legislation, to the extent that a well made gasket is capable of keeping a van or truck operating inside the law. The reputable gasket manufacturer ensures that he offers a gasket which will give the correct compressed fitted thickness for any individual engine within a family range, whereas the lesser producers will not necessarily provide this important service, thus impairing engine efficiency.
The most significant factor which should influence an engineer or fitter towards using a gasket from a major producer, such as Coopers Payen, is its involvement with the original equipment motor industry. The major manufacturers are continually developing products to meet the changing needs of engine designers and constructors. This company is working on the engines of the future and so possesses an awareness of engine behavioural patterns before they come onto the market. This gives the top manufacturing companies a knowledge of the design, manufacturing and performance requirements of a gasket in respect of a particular engine.
Technical synergy programmes for the development and testing of gaskets range from vehicles purchased for road testing to a continuous programme for test-bed engines. These are among the elements which combine to ensure that those in the engine repair, servicing and rernanufacturing business can use a relatively low cost but proven component in their business with complete confidence.
A workshop manager or fitter should bear in mind a number of points in relation to his selection of a cylinder-head gasket. Some of these can be identified, either by visual or physical examination, while others, though of a less immediately obvious nature, are equally important.
The range of thickness
Responsible gasket manufacturers produce gaskets in a range of thicknesses which provide a true replacement for the OE gasket as originally specified for an engine. Such gaskets can often be recognised by their own individual identification markings or identification notches cut onto an unloaded part of the gasket, Engine manufacturers such as Ford and Volkswagen are strict in being specific about particular thicknesses of gaskets for individual engines. This is why using a gasket from a manufacturer who actually understands the reason for compressed gasket thickness compatibility is important.
What is certain is if incorrect gaskets are fitted, poor starting, bad emission control, or physical damage to the engine can result.
Sealing capacity
The bore sealing area is another important consideration. It is vital that the bore eyelets are not only of the correct configuration for a particular task which they have to perform (and this can vary depending on the type of engine), but are also manufactured in such a way that the bore eyelet is held tightly against the wall of the pierced hole in the gasket body.
This is important in order to minimise the air gap between the inside of the eyelet and the body material. Irregular or large air gaps between the eyelet and the body can, during the functional cycle of the gasket, lead to eyelet collapse, fracture and eventual gasket failure.
Two bore seal designs relevant to Coopers Payen gaskets illustrate fundamental differences of design required for contrasting engines.
The Double Push Through Bore Seal (Figure 1) This form of combustion chamber bore seal is often designed to suit small, high-speed indirect injection diesel engines some of which have been developed from existing production petrol power units — where it is usually difficult to obtain a satisfactory gas seal.
The double-formed eyelet presented to the flame face gives added strength to resist the high-combustion gas pressures of a diesel engine, especially where the space between adjacent cylinder bore is limited. The "tongue" on the top face of the gasket is to support the combustion chamber located in the cylinder head.
The Primary and Secondary Bore Seal (Figure 2) may be used on director indirect-injection diesel engines, and is particularly suited to those of a large capacity. The principle is to combine strength and flexibility within the bore eyelet and is used where great difficulty is experienced in obtaining a long gasket life under heavy-duty conditions.
The primary seal is in the form of a laminate with the secondary seal similar to the "single-bore eyelet" design. It is therefore able to withstand high gas pressures experienced on both naturally aspirated or turbocharged diesel engines.
The primary seal, in effect, takes the place of the flame ring and allows the heat to flow from the flame face of the eyelet to both the cylinder head and block. The back-up seal — which may be coated — is protected from the combustion flame, and ensures effective sealing where the surface finish on the head or block faces is of relatively poor quality. This construction is also occasionally used in highperformance petrol engines developed from standard production units.
These two examples illustrate the use of different gasket designs to produce specific solutions for differing engines.
Surface finishes
The control of varnish finishes should not be underestimated. The use of a modern varnish applied uniformly, with the manufacturer's ability to further introduce compatible and additional sealing aids such as rubber-bead printing or body material impregnation, is an important element in determining the final quality and functional performance of a gasket.
Some gaskets of lower quality attempt to imitate selective rubber printing, sometimes using unsuitable elastomers which are unable to resist attack from oil and anti-freeze. This is another instance where experience and in-house control over both materials, technology and manufacturing processes, is so critical to the successful production of a reliable gasket.
There are gaskets to be found which have no varnish finish whatsoever and rely solely on a thin spray of aluminium paint. This provides no key whatsoever between the gasket and engine mating surfaces and contributes nothing to micro-sealing.
Fitting hints: there are a number of fundamental points to be borne in mind in order to avoid damage to a cylinder head gasket and subsequent damage to the engine as a whole. Coopers Payen cylinder head gaskets should always be fitted without any sealing agent.
The use of additional gasket sealants is not only unnecessary, but can, in fact, cause gasket failure for a number of reasons. Among them: sealant can build up the gasket thickness beyond the correct specification, can leak into the oil ways, can lead to gasket settlement and can also act as a lubricant.
All bolt holes should be free from water and oil. They should, where possible, be blown clean. Bolts must be examined for such damage as distorted threads and should be lightly lubricated with engine oil. Washers should be examined for flatness or distortion and surface damage and they should also be lubricated lightly with engine oil.
The engine manufacturer's tightening instructions should be adhered to strictly, especially if they call for a re-torque. In the event of a re-torque, each individual bolt should be backed off 1800 and then tightened to a specific figure, rather than re-torqued simply by pulling up to the recommended load.
Gaskets with either 0-rings or fitted with rubber inserts should be treated with care. In order to avoid damage or loss of these parts they should be unpacked only when they are about to be fitted. At all times guide studs should be used to ensure correct head-block gasket alignment.
No unwanted debris
While the gasket will accommodate high levels of surface abrasion, care should be taken that surfaces which come into contact with the cylinder head gasket should be free from obvious damage and should be both clean and flat. Care should be taken before finally replacing the head to ensure that no unwanted matter or debris falls onto the gasket surface.
Cost effective: gasket failure due to a sub-standard product can prove expensive both mechanically and economically. Selection of the appropriate gasket from a well established and reputable manufacturer such as Coopers Payen can both eliminate these factors and benefit the fitter and his customer.
Value for money is measured not merely in the price of the gasket.
• by Roland Swallow, Coopers Payen aftermarket product engineering manager.