Safer with ABS
Page 86
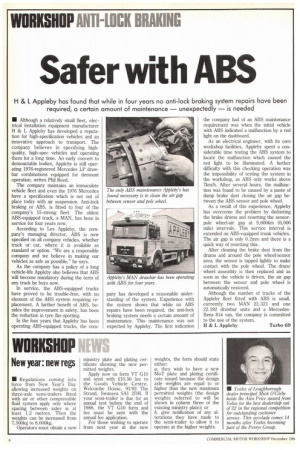
If you've noticed an error in this article please click here to report it so we can fix it.
H & L Appleby has found that while in four years no anti-lock braking system repairs have been required, a certain amount of maintenance — unexpectedly — is needed
• Although a relatively small fleet, electrical installation equipment manufacturer H & L Appleby has developed a reputation for high-specification vehicles and an innovative approach to transport. The company believes in specifying highquality, high-spec vehicles and operating them for a long time. An early convert to demountable bodies, Appleby is still operating 1976-registered Mercedes LP drawbar combinations equipped for demount operation, writes Phil Reed.
The company maintains an immaculate vehicle fleet and even the 1976 Mercedes have a specification which is not out of place today with air suspension. Anti-lock braking or ABS, is fitted to four of the company's 15-strong fleet. The oldest ABS-equipped truck, a MAN, has been in service for four years now.
According to Les Appleby, the company's managing director, ABS is now specified on all company vehicles, whether truck or car, where it is available as standard or option. "We are a responsible company and we believe in making our vehicles as safe as possible," he says.
As the company has a policy of a long vehicle-life Appleby also believes that ABS will become mandatory during the term of any truck he buys now.
In service, the ABS-equipped trucks have proved to be trouble-free, with no element of the ABS system requiring replacement. A further benefit of ABS, besides the improvement in safety, has been the reduction in tyre flat-spotting.
In the four years that Appleby has been operating ABS-equipped trucks, the corn pony has developed a reasonable understanding of the system. Experience with the system shows that while no ABS repairs have been required, the anti-lock braking system needs a certain amount of maintenance. This maintenance was not expected by Appleby. The first indication the company had of an ABS maintenance requirement was when the initial vehicle with ABS indicated a malfunction by a red light on the dashboard.
As an electrical engineer, with its own workshop facilities, Appleby spent a considerable time testing the ABS system to locate the malfunction which caused the red light to be illuminated. A further difficulty with this checking operation was the impossibility of testing the system in the workshop, as ABS only works above 71(m/h. After several hours, the malfunction was found to be caused by a paste of damp brake dust closing the air gap between the ABS sensor and pole wheel.
As a result of this experience, Appleby has overcome the problem by dedusting the brake drums and resetting the sensorpole wheel-air gap at 9,600km (6,000 mile) intervals. This service interval is extended on ABS-equipped trunk vehicles. The air gap is only 0.2mm and there is a quick way of resetting this.
After cleaning the brake dust from the drums and around the pole wheel/sensor area, the sensor is tapped lightly to make contact with the pole wheel. The drum/ wheel assembly is then replaced and as soon as the vehicle is driven, the air gap between the sensor and pole wheel is automatically restored.
Although the number of trucks of the Appleby fleet fitted with ABS is small, currently two MAN 22.321 and one 22.192 drawbar units and a MercedesBenz 814 van, the company is committed to the use of the system.
H & L Appleby Turbo 69