EC plans for MoT testing
Page 102
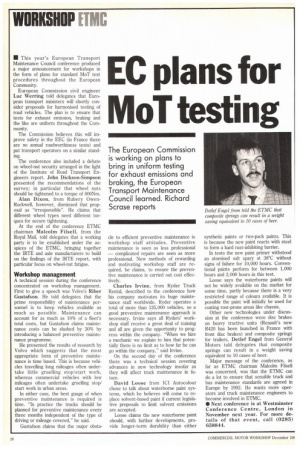
Page 103
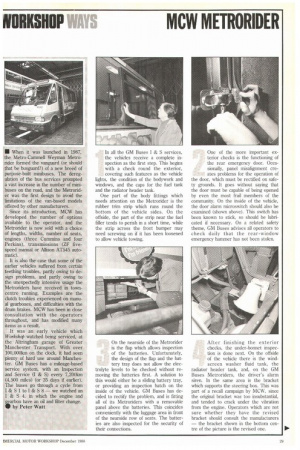
Page 104
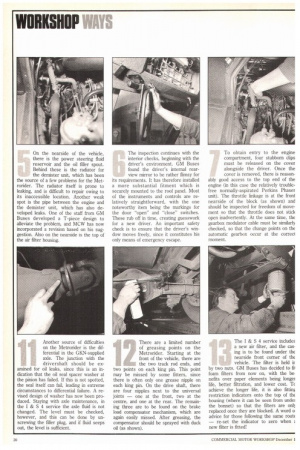
Page 105
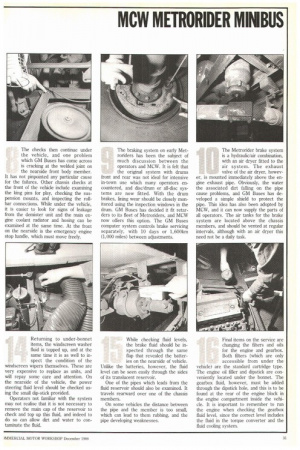
If you've noticed an error in this article please click here to report it so we can fix it.
The European Commission is working on plans to bring in uniform testing for exhaust emissions and braking, the European Transport Maintenance Council learned. Richard Scrase reports
• This year's European Transport Maintenance Council conference produced a major announcement for workshops in the form of plans for standard MoT test procedures throughout the European Community.
European Commission civil engineer Luc Werring told delegates that European transport ministers will shortly consider proposals for harmonised testing of road vehicles. The -plan is to ensure that tests for exhaust emission, braking and the like are uniform throughout the Community.
The Commission believes this will improve safety in the EEC (in France there are no annual roadworthiness tests) and put transport operators on a similar standing.
The conference also included a debate on wheel-nut security arranged in the light of the Institute of Road Transport Engineers report. John Dickson-Simpson presented the recommendations of the survey; in particular that wheel nuts should be tightened to a torque of 800Nm.
Alan Dixon, from Rubery OwenRockwell, however, dismissed that proposal as "irresponsible". He claims that different wheel types need different torques for secure tightening.
At the end of the conference ETMC chairman Malcolm Filsell, from the Royal Mail, told delegates that a working party is to be established under the auspices of the ETMC, bringing together the IRTE and axle manufacturers to build on the findings of the IRTE report, with particular focus on wheel-nut fatigue.
Workshop management A technical session during the conference concentrated on workshop management. First to give a speech was Volvo's Riber Gustafson. He told delegates that the prime responsibility of maintenance personnel is to keep vehicles available as much as possible. Maintenance can account for as much as 10% of a fleet's total costs, but Gustafson claims maintenance costs can be slashed by 30% by introducing a balanced preventive maintenance programme.
He presented the results of research by Volvo which suggests that the most appropriate form of preventive maintenance is time based. This is because vehicles travelling long mileages often undertake little gruelling stop/start work, whereas commercial vehicles with low mileages often undertake gruelling stop/ start work in urban areas.
In either case, the best guage of when preventive maintenance is required is time. "In practice the trucks should be planned for preventive maintenance every three months independent of the type of driving or mileage covered," he said.
Gustafson claims that the major obsta
cle to efficient preventive maintenance is workshop staff attitudes. Preventive maintenance is seen as less professional — complicated repairs are seen as more professional. New methods of rewarding and motivating workshop staff are required, he claims, to ensure the preventive maintenance is carried out cost effectively.
Charles Irvine, from Ryder Truck Rental, described to the conference how his company motivates its huge maintenance staff worldwide. Ryder operates a total of more than 135,000 vehicles, so a good preventive maintenance approach is necessary. Irvine says all Ryders' workshop staff receive a great deal of training and all are given the opportunity to progress within the company. "When we hire a mechanic we explain to him that potentially there is no limit as to how far he can go within the company," said Irvine.
On the second day of the conference there was a technical session covering advances in new technology insofar as they will affect truck maintenance in future.
David Loose from ICI Autocolour chose to talk about waterborne paint systems, which he believes will come to replace solvent-based paint if current legislative proposals to limit solvent emissions are accepted.
Loose claims the new waterborne paint should, with further developments, provide longer-term durability than either synthetic paints or two-pack paints. This is because the new paint reacts with steel to form a hard rust-inhibiting barrier.
In tests the new paint primer withstood an atomised salt spary at 38°C without signs of failure for 10,000 hours. Conventional paints perform for between 1,000 hours and 2,000 hours in this test.
Loose says the waterborne paints will not be widely available on the market for some time, partly because there is a very restricted range of colours available. It is possible the paint will initially be used for coating rust-prone areas like chassis.
Other new technologies under discussion at the conference were disc brakes on heavy tractive units (Renault's new R420 has been launched in France with front disc brakes) and composite springs for trailers. Detlef Engel from General Motors told delegates that composite springs can result in a weight saving equivalent to 10 cases of beer.
Major message of the conference, as far as ETMC chairman Malcolm Filsell was concerned, was that the ETMC can do a lot to ensure that sensible truck and bus maintenance standards are agreed in Europe by 1992. He wants more operators and truck maintenance engineers to become involved in ETMC.
• Next conference is at Westminster Conference Centre, London in November next year. For more details of that event, call (0285) 658844.
ii When it was launched in 1987, the Metro-Cammell Weyman Metro rider formed the vanguard (or should that be busguard?) of a new breed of purpose-built minibuses. The dereg ulation of the bus services prompted a vast increase in the number of minibuses on the road, and the Metrorid er was the first design to avoid the limitations of the van-based models offered by other manufacturers.
Since its introduction, MCW has developed the number of options available to the operator, and the Metrorider is now sold with a choice of lengths, widths, number of seats, engines (three Cummins and four Perkins), transmissions (2F fivespeed manual or Allison AT545 automatic).
It is also the case that some of the earlier vehicles suffered from certain teething troubles, partly owing to de sign problems, and partly owing to the unexpectedly intensive usage the Metroriders have received in town centre running. Examples are the clutch troubles experienced on manu al gearboxes, and difficulties with the drum brakes. MCW has been in close consultation with the operators throughout, and has modified many items as a result.
It was an early vehicle which Workshop watched being serviced, at
the Altringham garage of Greater Manchester Transport. With over 100,000km on the clock, it had seen plenty of hard use around Manches ter. GM Buses has a mileage-based service system, with an Inspection and Service (1 & S) every 7,200km (4,500 miles) (or 35 days if earlier). The buses go through a cycle from I & S 1 to I & S 8 — we watched an I 8z S 4, in which the engine and g.earbox have an oil and filter change. 1111 by Peter Watt In all the GM Buses I & S services, the vehicles receive a complete inspection as the first step. 'This begins with a check round the exterior, covering such features as the vehicle lights, the condition of the bodywork and windows, and the caps for the fuel tank and the radiator header tank.
One part of the body fittings which needs attention on the Metrorider is the rubber trim strip which runs round the bottom of the vehicle sides. On the offside, the part of the strip near the fuel filler tends to perish in a short time, while the strip across the front bumper may need screwing on if it has been loosened to allow vehicle towing.
On the nearside of the Metrorider is the flap which allows inspection of the batteries. Unfortunately, the design of the flap and the battery tray does not allow the electrolyte levels to be checked without removing the batteries first. A solution to this would either be a sliding battery tray, or providing an inspection hatch on the inside of the vehicle. GM Buses has decided to rectify the problem, and is fitting all of its Metroriders with a removable panel above the batteries. This coincides conveniently with the luggage area in front of the nearside row of seats. The batteries are also inspected for the security of their connections. One of the more important exterior checks is the functioning of the rear emergency door. Occasionally, panel misalignment creates problems for the operation of the door, which must be rectified on safety grounds. It goes without saying that the door must be capable of being opened by even the most frail members of the community. On the inside of the vehicle, the door alarm microswitch should also be examined (shown above). This switch has been known to stick, so should be lubricated if necessary. On a related safety theme, GM Buses advises all operators to check daily that the rear-window emergency hammer has not been stolen.
After finishing the exterior checks, the under-bonnet inspection is done next. On the offside of the vehicle there is the windscreen washer fluid tank, the radiator header tank, and, on the GM Buses Metroriders, the driver's alarm siren. In the same area is the bracket which supports the steering box. This was part of a recall campaign by MCW, since the original bracket was too insubstantial, and tended to crack under the vibration from the engine. Operators which are not sure whether they have the revised bracket should consult the manufacturers — the bracket shown in the bottom centre of the picture is the revised one. On the nearside of the vehicle, there is the power steeling fluid reservoir and the oil filler spout. Behind these is the radiator for the demister unit, which has been the source of a few problems for the Metrorider. The radiator itself is prone to leaking, and is difficult to repair owing to its inaccessible location. Another weak spot is the pipe between the engine and the demister unit, which has also developed leaks. One of the staff from GM Buses developed a 1-piece design to alleviate the problem, and MCW has now incorporated a revision based on his suggestion. Also on the nearside is the top of the air filter housing. The inspection continues with the interior checks, beginning with the driver's environment. GM Buses found the driver's internal rearview mirror to be rather flimsy for its requirements. It has therefore installed a more substantial fitment which is securely mounted to the roof panel. Most of the instruments and controls are relatively straightforward, with the one noteworthy item being the markings for the door "open" and "close" switches. These rub off in time, creating guesswork for a new driver. An important safety check is to ensure that the driver's window moves freely, since it constitutes his only means of emergency escape. To obtain entry to the engine compartment, four stubborn clips must be released on the cover alongside the driver. Once the cover is removed, there is reason ably good access to the top end of the engine (in this case the relatively troublefree normally-aspirated Perkins Phaser unit). The throttle linkage is at the front nearside of the block (as shown) and should be inspected for freedom of movement so that the throttle does not stick open inadvertently. At the same time, the gearbox modulator cable must be similarly checked, so that the change points on the automatic gearbox occur at the correct moment. The checks then continue under the vehicle, and one problem which GM Buses has come across is cracking at the welded joint on the nearside front body member.
It has not pinpointed any particular cause for the failures. Other chassis checks at the front of the vehicle include examining the king pins for play, checking the suspension mounts, and inspecting the rollbar connections. While under the vehicle, it is easier to look for signs of leakage from the demister unit and the main engine coolant radiator and hosing can be examined at the same time. At the front on the nearside is the emergency engine stop handle, which must move freely. The braking system on early Metroriders has been the subject of much discussion between the operators and MCW. It is felt that the original system with drums front and rear was not ideal for intensive in-town use which many operators encountered, and disc/drum or all-disc systems are now fitted. With the drum brakes, lining wear should be closely monitored using the inspection windows in the drum. GM Buses has decided it fit retarders to its fleet of Metroriders, and MCW now offers this option. The GM Buses computer system controls brake servicing separately, with 10 days or 1,600km (1,000 miles) between adjustments. The Metrorider brake system is a hydraulic/air combination, with an air dryer fitted to the air system. The exhaust valve of the air dryer, howev er, is mounted immediately above the engine exhaust pipe. Obviously, the water the associated dirt falling on the pipe cause problems, and GM Buses has developed a simple shield to protect the pipe. This idea has also been adopted by MCW, and it can now supply the parts of all operators. The air tanks for the brake system are located above the chassis members, and should be vented at regular intervals, although with an air dryer this need not be a daily task.
Another source of difficulties on the Metrorider is the differential in the GKN-supplied axle. The junction with the drivershaft should be examined for oil leaks, since this is an indication that the oil seal spacer washer at the pinion has failed. If this is not spotted, the seal itself can fail, leading in extreme circumstances to differential failure. A revised design of washer has now been produced. Staying with axle maintenance, in the I & S 4 service the axle fluid is not changed. The level must be checked, however, and this can be done by unscrewing the filler plug, and if fluid seeps out, the level is sufficient.
There are a limited number of greasing points on the Metrorider. Starting at the front of the vehicle, there are the two track rod ends, and two points on each king pin. This point may be missed by some fitters, since there is often only one grease nipple on each king pin. On the drive shaft, there are four nipples next to the universal joints — one at the front, two at the centre, and one at the rear. The remaining three are to be found on the brake load compensator mechanism, which are again easily missed. After greasing, the compensator should be sprayed with duck oil (as shown).
The I & S 4 service includes a new air filter, and the casing is to be found under thE nearside front corner of thE vehicle. The filter is held ir by two nuts. GM Buses has decided to fit foam filters from now on, with the be nefits over paper elements being longei life, better filtration, and tower cost. TE achieve the longer life, it is also fittir4 restriction indicators onto the top of thE housing (where it can be seen from undei the bonnet) so that the filters are oni3 replaced once they are blocked. A word o advice for those following the same rout( — re-set the indicator to zero when new filter is fitted! Returning to under-bonnet items, the windscreen washer fluid is topped up, and at the same time it is as well to inspect the condition of the windscreen wipers themselves. These are very expensive to replace as units, and will repay some care and attention. On the nearside of the vehicle, the power steering fluid level should be checked using the small dip-stick provided.
Operators not familiar with the system may not realise that it is not necessary to remove the main cap of the reservoir to check and top up this fluid, and indeed to do so can allow dirt and water to contaminate the fluid.
While checking fluid levels, the brake fluid should be inspected through the same flap that revealed the batteries on the nearside of vehicle. Unlike the batteries, however, the fluid level can be seen easily through the sides of its translucent reservoir.
One of the pipes which leads from the fluid reservoir should also be examined. It travels rearward over one of the chassis members.
On some vehicles the distance between the pipe and the member is too small, which can lead to them rubbing, and the pipe developing weaknesses. Final items on the service are changing the filters and oils for the engine and gearbox. Both filters (which are only ' accessible from under the vehicle) are the standard cartridge type. The engine oil filler and dipstick are conveniently located under the bonnet. The gearbox fluid, however, must be added through the dipstick hole, and this is to be found at the rear of the engine block in the engine compartment inside the vehicle. It is important to remember to run the engine when checking the gearbox fluid level, since the correct level includes the fluid in the torque converter and the fluid cooling system.