DEMOUNTABLE DISTRIBUTION-17
Page 56
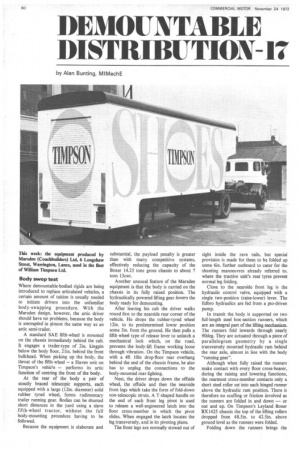
Page 57

If you've noticed an error in this article please click here to report it so we can fix it.
Body swop test Where demountable-bodied rigids are being introduced to replace articulated vehicles, a certain amount of tuition is usually needed to initiate drivers into the unfamiliar body-swapping procedure. With the Marsden design, however, the artic driver should have no problems, because the body is uncoupled in almost the same way as an artic semi-trailer.
A standard SAE fifth-wheel is mounted on the chassis immediately behind the cab. It engages a trailer-type of 2in. kingpin below the body floor, 21in. behind the front bulkhead. When picking up the body, the throat of the fifth-wheel — a Slaver' unit on Timpson's vehicle — performs its artic function of centring the front of the body.
At the rear of the body a pair of stoutly braced telescopic supports, each equipped with a large (12in. diameter) solid rubber tyred wheel, forms rudimentary trailer running gear. Bodies can be shunted short distances in the yard using a slave fifth-wheel tractor, without the full body-mounting procedure having to be followed.
Because the equipment is elaborate and substantial, the payload penalty is greater than with many competitive systems, effectively reducing the capacity of the Boxer 14.25 tons gross chassis to about 7 tons 13cwt.
Another unusual feature of the Marsden equipment is that the body is carried on the chassis in its fully raised position. The hydraulically powered lifting gear lowers the body ready for demounting.
After leaving his cab the driver walks round first to the nearside rear corner of the vehicle. He drops the rubber-tyred wheel 12in. to its predetermined lower position some 3M. from the ground. He then pulls a fifth-wheel type of' release lever to unlatch a mechanical lock which, on the road, prevents the body-lift frame working loose through vibration. On the Timp son vehicle, with a 4ft 10in drop-floor rear overhang behind the end of the chassis frame, he also has to unplug the connections to the body-mounted rear-lighting.
Next, the driver drops down the offside wheel, the offside and then the nearside front legs which take the form of fold-down non-telescopic struts. A T-shaped handle on the end of each front leg pivot is used to release a well-engineered latch into the floor cross-member in which the pivot slides. When engaged the latch locates the leg transversely, and in its pivoting plane.
The front legs are normally stowed out of sight inside the rave rails, but special provision is made for them to be folded up some 6in. further outboard to cater for the shunting manoeuvres already referred to, where the tractive unit's rear tyres prevent normal leg folding.
Close to the nearside front leg is the hydraulic control valve, equipped with a single two-position (raise-lower) lever. The Edbro hydraulics are fed from a pto-driven pump.
In transit the body is supported on two full-length steel box-section runners, which are an integral part of the lifting mechanism. The runners fold inwards through nearly 90deg. They are actuated through a piece of parallelogram geometry by a single transversely mounted hydraulic ram behind the rear axle, almost in line with the body "running gear".
Although when fully raised the runners make contact with every floor cross-bearer, during the raising and lowering functions, the rearmost cross-member contacts only a short steel roller set into each hinged runner above the hydraulic ram position. There is therefore no scuffing or friction involved as the runners are folded in and down — or out and up. On Timpson's Leyland Boxer BX1425 chassis the top of the lifting rollers dropped from 48.5in. to 42.5in. above ground level as the runners were folded.
Folding down the runners brings the body's rear wheels on to the ground, where they must be chocked using bricks or pieces of timber. It is a pity a simple brake — possibly acting against the outside of the tyre — could not be incorporated. The fifth wheel jaws are then released in the usual way and the chassis can be driven out. As the kingpin rubbing plate below the body slides back it drops down a ramped sub-frame behind the fifth-wheel, to lower the front legs to the ground.
Picking up is essentially a reversal of the procedure. The ramped frame on Timpson's Boxer chassis is located far enough back so that, when remounting, the front of the body is raised before the Luton head can foul the back of the cab.
Misalignment of body and chassis at the rear end is taken care of automatically, through one or other hinged runner contacting one of a pair of longitudinals below the body floor to push it across on the rollers. This would not normally occur until the body wheels are off the ground, so that sideways scuffing is avoided.
As the folding runners are raised to the vertical, a pair of short +in.-thick welded flanges just behind the rollers, which overhang the outer edges of the runners by only fin. "hook" over the top of the body longitudinals. This is the only means by which the body is held down at the rear, and one feels that in the event of an accident, a small amount of distortion in the body floor structure could result in the body breaking loose. At the front of course the SAE coupling provides more than adequate body location in all planes.
Finally, raising the rear wheels calls for a good deal of physical effort. Each wheel and inner leg weighs about 501b, and a 12in. vertical lift is involved, using a piece of timber dowel or tube (normally carried in the cab) which is inserted into the hollow stub-axle of the wheel.
One of Timpson's more experienced drivers (an LDoY area finalist) put the Marsden equipment through its paces -in a very polished performance. The body, which was almost empty, was dropped in 1min 25sec and picked up again in a total of lmin 35sec.
Largely because of the fifth-wheel installation, the body floor height is more than with many rival swop-body systems, at 4ft 4in. The drop-well at the rear of the glass-fibre panelled Marsden Luton van body is 4ft 6in. long. The floor height in the well is exactly half that of the main 25ft 6in.-long deck — at 2ft 2in.
William Timpson, one of the country's leading shoe manufacturers, operates four Marsden-equipped Boxer demountables, currently with six bodies, although this number is due to rise to eight, giving a 2 to 1 body-chassis ratio. The demountables have replaced Leyland Laird tractive units and Boden van semi-trailers of almost identical length and capacity to the new swop bodies.
After moving from an artic to one of the Marsden-equipped Boxer demountables, Timpson's driver Keith Graham can now drop and pick up a body as quickly as a semi-trailer. The tedious winding of landing gear is avoided. At the same time he appreciates the safer handling of a rigid vehicle in winter conditions.
Although our appraisal of the equipment was carried out at Timpson's Kettering factory, bodies are normally dropped only at the company's large warehouse and distribution centre at Wythenshawe, Manchester, where the vehicles are based.
Full consignments are loaded in Manchester, ready for distribution next day to shoe shops all over the country. A total of 10 to 15 deliveries a day is typical. The same vehicles are employed for the collection of batches of footwear from scattered manufacturing plants, in addition to Timpson's own Kettering works, destined for the Manchester warehouse.
Timpson's transport controller, Mr F. Potts, is favourably impressed with the working of the Marsden demountables, which, he says, because of their similarity in principle to existing artics in the fleet have been phased into operation with the minimum disruption.