Welding in Maintenance
Page 57
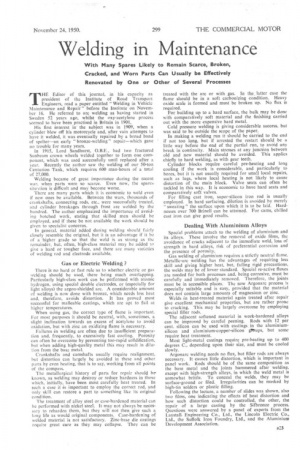
If you've noticed an error in this article please click here to report it so we can fix it.
With Many Spares Likely to Remain Scarce, Broken, Cracked, and Worn Parts Can Usually be Effectively Renovated by One or Other of Several Processes THE Editor of this journal, in his capacity as president of the Institute of Road Transport Engineers, read a paper entitled "Welding in Vehicle Maintenance and Repair" before the Institute on November 16. He referred to arc welding as having started in Sweden 52 years ago, whilst the oxy-acetylene process seemed to have been practised in Britain in 1901.
His first interest in the subject was in 1909, when a cylinder blew off his motorcycle and, after vain attempts to have it welded, it was eventually repaired by a broad band of spelter—an early "bronze-welding" repair—which gave no trouble for many years.
In 1915, Lord Sandhurst, 0.B.E., had two fractured Sunbeam crown wheels welded together to form one component, which was used successfully until replaced after a year. Recently the author saw the welding of our 50-ton Centunion Tank, which requires 600 man-hours of a total of 27,000.
Welding became of great importance during the recent war. when parts were so scarce. Even now, the spares. situation is difficult and may become worse.
There are many parts which it is economic to weld even if new ones be available. Between the wars, thousands of crankshafts, connecting rods. etc.. were successfully treated, and cylinder breakages through frost are welded by the hundred. The author emphasized the importance of avoiding hatched work, stating that skilled men should be employed, and if these be not available the work should he given to specialist concerns.
In general, material added duning welding should fairly closely resemble the original, but it is an advantage if it be of a 'higher grade so that the weld is as strong as the remainder, but, often, high-class material may be added to give a hard or tougher face, and there are many varieties of welding rod and electrode available.
Gas or Electric Welding ?
There is no hard or fast rule as to whether electric or gas welding should be used, there being much overlapping. Particularly high-class work can be performed with atomic hydrogen, using spedal double electrodes, or (especially for light alloys) the argon-shielded arc. A considerable amount of welding is now done with bronze, which needs less heat and, therefore, avoids distortion. It has proved most successful for malleable castings, which are apt to fail at higher temperatures.
When using gas, the correct type of flame is important. For most purposes it should be neutral, with, sometimes, a slight inclination towards an excess of acetylene to avoid oxidation, but with zinc an oxidizing flame is necessary. .
Failures in welding are often due to insufficient preparation and, frequently, to excessively fast cooling. Porosity can often be overcome by preventing too-rapid solidification, but when adding high-quality metal this may result in dilution from the base metal.
Crankshafts and camshafts usually require realignment, hut distortion can largely be avoided in these and other parts by even heating, that is to say, working from all points of the compass.
The metallurgical history of parts for repair should her known, as welding may destroy or reduce hardness in those which, initially, have been most carefully heat treated. In such a case it is important to employ the correct rod, and only skill can restore a part to something like its original condition.
The treatment of alloy steel or case-hardened material can be performed with nickel steel. It may not always be necessary to reharden them, but they will not then give such a long life as would original components. Case-hardening of welded material is not satisfactory. Zinc-base die castings require great care as they may collapse. They can be treated with the arc or with gas. In the, latter case the flame should be in a soft carbonizing condition. Heavy oxide scale is formed and must be broken up. No flux is required.
For building up to a hard surface, the bulk may be done with comparatively soft material and the finishing carried out with the more expensive hard metal.
Cold pressure welding is giving considerable success, but was said to be outside the scope of the paper.
In making a welding run it should be carried to the end if not too long, but if arrested the restart should be a little way before the end of the partial run, to avoid any break in continuity. Main stresses at any junction between old and new material should be avoided. This applies chiefly to hard welding, as with gear teeth.
Cylinder blocks require careful pre-heating and long cooling if the work is considerable, and particularly to bores, but it is not usually required for small local repairs, such as lugs, where local heating is not likely to cause distortion of the main block. Valve seats can often be tackled in this way. It is economic to have hard seats and comparatively soft valves.
For filling cast iron, super-silicon iron rod is usually employed. In hard surfacing, dilution is avoided by merely "sweating" the surface upon which it is to be laid. Hardnesses over 700 Brinell can be attained. For cams, chilled cast iron can give good results.
Dealing With Aluminium Alloys
Special problems attach to the welding of aluminium and its alloys. These involve the removal of oxide films, the avoidance of cracks adjacent to the immediate weld, loss of strength in hard alloys, risk of preferential corrosion and the presence of porosity. Gas welding of aluminium requires a strictly neutral flame. Metallic-arc welding has the advantages of requiring less skill and giving higher heat, but, failing rigid precautions. the welds may be of lower standard. Special re-active fluxes are needed for both processes and, being corrosive, must be carefully and immediately removed. Therefore, the joints must be in accessible places. The new Argonarc process is especially suitable and is easy, provided that the material does not contain large amounts of magnesium or zinc.
Welds in heat-treated material again treated after repair give excellent mechanical properties, but are rather prone to cracking. This may be largely overcome by employing special filler rods. The adjacent softened material in work-hardened alloys can be improved by careful peening. Rods with 12 per cent. silicon can be used with castings in the aluminiumsilicon and aluminium-copper-silicon glaatips, but some require heat treatment.
Most light-metal castings require pre-heating up to 400 degrees C., depending upon their size, and must be cooled slowly. Argonarc welding needs no flux, but filler rods are always necessary. It causes little distortion, which is important in panel work. Rods should be of the same composition as the base metal and the joints hammered after welding. except with high-strength alloys, in which the weld metal is somewhat brittle. To conceal the welds, they may be surface-ground or filed. Irregularities can be masked by high-tin solders or plastic filling.
Following the lecture, a number of slides was shown, also two films, one indicating the effects Of heat distortion and how such distortion could be controlled, the other, the repair of a large casting by the Sifbronze process. Questions were answered by a panel of experts from the Laystall. Engineering Co.. Ltd., the Lincoln Electric Co., Ltd., the Suffolk Iron Foundry, Ltd., and the Aluminium Development Association.