24th March 1984, Page 48
24th March 1984
Page 48
Page 49
Page 48, 24th March 1984
—
Close
Noticed an error?
If you've noticed an error in this article please click here to report it so we can fix it.
IT DOES not take a cynic to realise that sooner or later any commercial vehicle will break down, whatever the manufacturer may claim. For the operator, unscheduled downtime is just another aspect of the transport business to be dealt with as best as possible. However, nothing annoys a haulier more than having an expensive vehicle standing idle in his workshop while a vital part is "Out of stock, Sir" at his local dealer.
In the late Seventies Leyland Trucks attracted more than its share of moaning whenever spares were mentioned. The problem was not helped by AEC, Guy, Scammell and Albion all holding their own extensive parts, while Terrier spares, as a legacy of the old BMC days, were treated as car parts and held at Cowley.
In order to improve its service back-up and regain operator confidence, Leyland Vehicles invested £17m in a new parts warehouse, which opened in September 1981, and bought 95 per cent of all Leyland captive parts (ones that can be obtained only from a Leyland dealer) into a central complex.
The Leyland Parts International Distribution Centre, built on the site of the old Leyland Parts warehouse at Chorley, Lancashire, stocks the complete range of Leyland Truck and Bus spare parts, with an inventory extending to some 150,000 individual parts valued at E100m. Truck parts are held for at least 10 years, while bus spares are stocked for 15 years. To support non-current vehicles with components, Leyland Parts also has its own manufacturing unit at Chorley producing individual replacements.
Fifteen minutes drive from the Truck manufacturing plant at Leyland, the Chorley warehouse — 43,000 cubic metres storage capacity — is also the central warehouse for Leyland's Multipart operation. Multipart, launched in February, 1980, supplies its dealers with "competitive parts" produced by outside component manufacturers and common to a number of commercial marques.
While many manufacturers besides Leyland have invested heavily in automated centralised parts warehousing, with rapid parts picking, all the robots in the world will not help an operator if his dealer takes two weeks to send a parts order.
To give a more rapid response to normal stock orders as well as urgent Vehicle Off Road (VOR: parts request, Leyland Vehicles has been developing a series 01 computerised links between it central parts complex and its 91 UK truck dealers by means of E system known as CAT or Corn puter Action Terminals.
CAT, however, is no nev invention; the first CAT systen was installed as early as 1978 ii most Leyland dealer premise with ITT Teletype equipmem The early terminals consisted c a keyboard and printer whic were connected by normal telE phone lines to the old part centre at Chorley.
The dealer simply typed in IT stock request, which was ser via phone lines to the IBM mail frame at Chorley. The ITT term nals allowed a dealer not only I place VOR and stock request but also gave him an on-line i quiry facility for parts inform tion, allowing him to find out any parts had been discon nued. By being in direct tow With Charley, the dealer could also see how his latest order was progressing, allowing him to let his customer know when his part would arrive.
To give dealers greater flexi bility, the teletype system was further expanded by incorporating a tape facility that could be used to assemble a single "batch" of parts orders and transmit it overnight to the Chorley warehouse.
This improvement, however, was not without its problems. Unlike a normal telex message, the stock data was placed in digital form on a magnetic tape cassette. Although this could be transmitted via a conventional phone land-line using a special connector or "modem" supplied by the Post Office, the order data was often disrupted by normal interference on the phone lines.
This would cause the transmission to be shut off and need to be re-transmitted by the dealer the next day. An extended tape-running period created further difficulties, for with a playing time of between 35 and 40 minutes, stock entry transmissions were not only vulnerable to line interference but were difficult to edit or amend quickly. Each tape had to be run through completely before every entry could be read. Faced with these operational limitations on the ITT terminals, in 1982 Leyland undertook a programme of system evaluations to find a suitable alternative. In 1983 it replaced the ITT equipment with Systime S500 microcomputers, which not only supplied the same facilities to the dealer as the old CAT terminal but also gave him additional functions designed to help him with his own business.
Among the new facilities is a vehicle locator system. VOL allows the dealer to track down a Leyland chassis at another distributor's premises if necessary, as well as check the status of any of his vehicle orders on the assembly line. A technical data system also provides him with all the latest chassis parts applicability and any details regarding the latest models.
Further new facilities for the dealer using the CAT system include an invoice or credit note inquiry function as well as a warranty inquiry facility, and a parts locator scheme that can track down parts held by other Leyland dealers, when the parts are unavailable at Chorley. Being in touch with the Leyland manufacturing computer, the dealer also has access to additional techni cal data should he require it.
The Systime CAT equipment features a number of improvements over the old Teletype. In addition to a normal printer there is a visual display unit or vdu which allows easier order entry and compilation. A dealer can also have any additional number of these units with data entry keyboards situated in different locations throughout his premises. The old cassette storage tape has been replaced by a magnetic floppy disc unit which allows quicker editing. With the micro, a dealer can quickly review and adjust his own stock levels.
While VOR orders will be sent at any time, normal stock orders are usually assembled throughout the day ready for transmission late in the afternoon. Having compiled an order the CAT operator dials the Chorley complex to connect the CAT micro with the IBM mainframe and transmits the stock requirement, which now only takes minutes. The previous problems with Telecom line interference have been eliminated by Leyland which has incorporated error correcting modems into the Charley mainframe; continual transmission is guar anteed.
A short time after transmis sion the dealer re-dials Charley to check that the order has been received and is valid. If there are any problems the order can be quickly amended and re transmitted. Once accepted by Leyland parts, the process of picking the components begins. Next morning the dealer can again dial Charley to check how his order is progressing and be advised of delivery times.
Each of the 91 Leyland dealers has a specific delivery day for his parts, although any VOR order transmitted to Leyland before 4pm will be delivered to the dealer the next day.
Seventy-four Leyland Truck dealers have so far converted from the ITT teletype to the Systime micro-computers. Most dealers are familiar with direct link transmission and staff retraining has been kept to a minimum. Any operating problems arising that cannot be solved by the dealer can be rectified by Chorley, which has a reverse dial-back facility using a micro-computer of its own.
To see how well the CAT system works I paid a brief visit to Gilbraith Commercials at Chorley which replaced its Teletype equipment with the Systime micro six months ago.
Gilbraith, based close to the Leyland parts complex, also has dealerships in Accrington and Carlisle and uses CAT not only for parts location within Leyland but also within its own group. Gilbraith has already invested heavily in its own computer systems, but feels that the additional Systime micro is particularly useful for VOR part orders.
Tony Howarth, Gilbraith's computer manager, picked out eight VOR orders for Ribble Bus transmitted at 1.40pm. According to our 2.30pm VOR inquiry, the parts were being picked at Charley at 2.04pm and would be ready for collection soon after 3pm. As Gilbraith was situated so close to Leyland parts the firm would make its own collection.
Apart from VORs, which are dispatched on average every half hour, Gilbrath uses the CAT micro to submit its weekly parts" order of between 1,500 to 1,600 lines per order each with an average of 20 items per line.
It is perhaps fitting that Gilbraith at Chorley should bp actively using the CAT system particularly as its managing director, Sam Newton, the newly elected chairman of the Leyland Trucks Distributors Association (CM, March 10), believes strongly that the key to Leyland's recovery lies firmly in the hands of its dealers and the service they provide to commercial vehicle customers.
Page 48
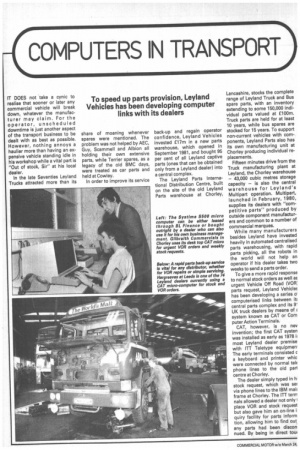
Page 49
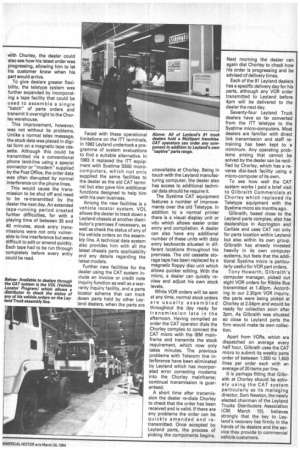
If you've noticed an error in this article please click here to report it so we can fix it.
IT DOES not take a cynic to realise that sooner or later any commercial vehicle will break down, whatever the manufacturer may claim. For the operator, unscheduled downtime is just another aspect of the transport business to be dealt with as best as possible. However, nothing annoys a haulier more than having an expensive vehicle standing idle in his workshop while a vital part is "Out of stock, Sir" at his local dealer.
In the late Seventies Leyland Trucks attracted more than its share of moaning whenever spares were mentioned. The problem was not helped by AEC, Guy, Scammell and Albion all holding their own extensive parts, while Terrier spares, as a legacy of the old BMC days, were treated as car parts and held at Cowley.
In order to improve its service back-up and regain operator confidence, Leyland Vehicles invested £17m in a new parts warehouse, which opened in September 1981, and bought 95 per cent of all Leyland captive parts (ones that can be obtained only from a Leyland dealer) into a central complex.
The Leyland Parts International Distribution Centre, built on the site of the old Leyland Parts warehouse at Chorley, Lancashire, stocks the complete range of Leyland Truck and Bus spare parts, with an inventory extending to some 150,000 individual parts valued at E100m. Truck parts are held for at least 10 years, while bus spares are stocked for 15 years. To support non-current vehicles with components, Leyland Parts also has its own manufacturing unit at Chorley producing individual replacements.
Fifteen minutes drive from the Truck manufacturing plant at Leyland, the Chorley warehouse — 43,000 cubic metres storage capacity — is also the central warehouse for Leyland's Multipart operation. Multipart, launched in February, 1980, supplies its dealers with "competitive parts" produced by outside component manufacturers and common to a number of commercial marques.
While many manufacturers besides Leyland have invested heavily in automated centralised parts warehousing, with rapid parts picking, all the robots in the world will not help an operator if his dealer takes two weeks to send a parts order.
To give a more rapid response to normal stock orders as well as urgent Vehicle Off Road (VOR: parts request, Leyland Vehicles has been developing a series 01 computerised links between it central parts complex and its 91 UK truck dealers by means of E system known as CAT or Corn puter Action Terminals.
CAT, however, is no nev invention; the first CAT systen was installed as early as 1978 ii most Leyland dealer premise with ITT Teletype equipmem The early terminals consisted c a keyboard and printer whic were connected by normal telE phone lines to the old part centre at Chorley.
The dealer simply typed in IT stock request, which was ser via phone lines to the IBM mail frame at Chorley. The ITT term nals allowed a dealer not only I place VOR and stock request but also gave him an on-line i quiry facility for parts inform tion, allowing him to find out any parts had been discon nued. By being in direct tow With Charley, the dealer could also see how his latest order was progressing, allowing him to let his customer know when his part would arrive.
To give dealers greater flexi bility, the teletype system was further expanded by incorporating a tape facility that could be used to assemble a single "batch" of parts orders and transmit it overnight to the Chorley warehouse.
This improvement, however, was not without its problems. Unlike a normal telex message, the stock data was placed in digital form on a magnetic tape cassette. Although this could be transmitted via a conventional phone land-line using a special connector or "modem" supplied by the Post Office, the order data was often disrupted by normal interference on the phone lines.
This would cause the transmission to be shut off and need to be re-transmitted by the dealer the next day. An extended tape-running period created further difficulties, for with a playing time of between 35 and 40 minutes, stock entry transmissions were not only vulnerable to line interference but were difficult to edit or amend quickly. Each tape had to be run through completely before every entry could be read. Faced with these operational limitations on the ITT terminals, in 1982 Leyland undertook a programme of system evaluations to find a suitable alternative. In 1983 it replaced the ITT equipment with Systime S500 microcomputers, which not only supplied the same facilities to the dealer as the old CAT terminal but also gave him additional functions designed to help him with his own business.
Among the new facilities is a vehicle locator system. VOL allows the dealer to track down a Leyland chassis at another distributor's premises if necessary, as well as check the status of any of his vehicle orders on the assembly line. A technical data system also provides him with all the latest chassis parts applicability and any details regarding the latest models.
Further new facilities for the dealer using the CAT system include an invoice or credit note inquiry function as well as a warranty inquiry facility, and a parts locator scheme that can track down parts held by other Leyland dealers, when the parts are unavailable at Chorley. Being in touch with the Leyland manufacturing computer, the dealer also has access to additional techni cal data should he require it.
The Systime CAT equipment features a number of improvements over the old Teletype. In addition to a normal printer there is a visual display unit or vdu which allows easier order entry and compilation. A dealer can also have any additional number of these units with data entry keyboards situated in different locations throughout his premises. The old cassette storage tape has been replaced by a magnetic floppy disc unit which allows quicker editing. With the micro, a dealer can quickly review and adjust his own stock levels.
While VOR orders will be sent at any time, normal stock orders are usually assembled throughout the day ready for transmission late in the afternoon. Having compiled an order the CAT operator dials the Chorley complex to connect the CAT micro with the IBM mainframe and transmits the stock requirement, which now only takes minutes. The previous problems with Telecom line interference have been eliminated by Leyland which has incorporated error correcting modems into the Charley mainframe; continual transmission is guar anteed.
A short time after transmis sion the dealer re-dials Charley to check that the order has been received and is valid. If there are any problems the order can be quickly amended and re transmitted. Once accepted by Leyland parts, the process of picking the components begins. Next morning the dealer can again dial Charley to check how his order is progressing and be advised of delivery times.
Each of the 91 Leyland dealers has a specific delivery day for his parts, although any VOR order transmitted to Leyland before 4pm will be delivered to the dealer the next day.
Seventy-four Leyland Truck dealers have so far converted from the ITT teletype to the Systime micro-computers. Most dealers are familiar with direct link transmission and staff retraining has been kept to a minimum. Any operating problems arising that cannot be solved by the dealer can be rectified by Chorley, which has a reverse dial-back facility using a micro-computer of its own.
To see how well the CAT system works I paid a brief visit to Gilbraith Commercials at Chorley which replaced its Teletype equipment with the Systime micro six months ago.
Gilbraith, based close to the Leyland parts complex, also has dealerships in Accrington and Carlisle and uses CAT not only for parts location within Leyland but also within its own group. Gilbraith has already invested heavily in its own computer systems, but feels that the additional Systime micro is particularly useful for VOR part orders.
Tony Howarth, Gilbraith's computer manager, picked out eight VOR orders for Ribble Bus transmitted at 1.40pm. According to our 2.30pm VOR inquiry, the parts were being picked at Charley at 2.04pm and would be ready for collection soon after 3pm. As Gilbraith was situated so close to Leyland parts the firm would make its own collection.
Apart from VORs, which are dispatched on average every half hour, Gilbrath uses the CAT micro to submit its weekly parts" order of between 1,500 to 1,600 lines per order each with an average of 20 items per line.
It is perhaps fitting that Gilbraith at Chorley should bp actively using the CAT system particularly as its managing director, Sam Newton, the newly elected chairman of the Leyland Trucks Distributors Association (CM, March 10), believes strongly that the key to Leyland's recovery lies firmly in the hands of its dealers and the service they provide to commercial vehicle customers.