The Technique of Piston Ring Plating
Page 45
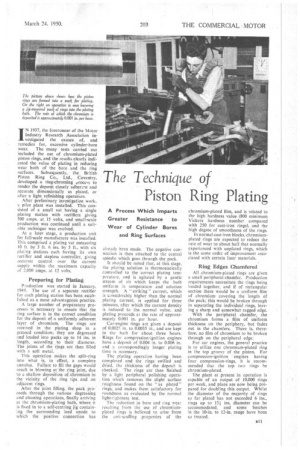
If you've noticed an error in this article please click here to report it so we can fix it.
A Process Which Imparts Greater Resistance to Wear of Cylinder Bores and Ring Surfaces IN 1937, the forerunner of the Motor Industry Research Association investigated the causes of, and remedies for, excessive cylinder-bore
wear. The many tests carried out included the use of chromium-plated piston rings, and the results clearly indicated the value of plating 'in reducing wear both of the bore and the ring surfaces. Subsequently, the British Piston Ring Co., . Ltd., . Coventry, developed a ring-chroming process to render the deposit closely adherent and accurate dimensionally as plated, or after a light refinishing operation.
After preliminary investigation work, a pilot plant was installed. This consisted of a small vat having a single plating station with rectifiers giving 500 amps. at 15 volts, and small-scale production was continued until a suitable technique was evolved.
At a later stage, a production unit for full-scale manufacture was installed. This comprised a plating vat measuring 10 ft. by 3 ft. 6 ins. by 3 ft., with six plating stations each having its own rectifier and stepless controller, giving accurate control over the current supply within the maximum capacity of 2,000 amps. at 12 volts.
Preparing for Plating
Production was started in January, 1949. The use of a separate rectifier for each plating station has been established as a most advantageous practice.
A large number of preparatory processes is necessary to ensure that the ring surface is in the correct condition for the deposit of a uniformly adherent layer of chromium. The rings are received in the plating shop in a greased condition; they are degreased and loaded into packs up to 14 ins, in length, according to their diameter. The joints of the rings are then filled with a soft metal. , This operation makes the split-ring into what is, in effect, a complete annulus. Failure to fill the gaps would result in blowing at the ring joint, due to a shallow deposition of chromium in the vicinity of the ring tips and on adjacent rings.
After the joint filling, the pack proceeds through the various degreasing and cleaning operations, finally arriving at the chromium-plating bath, where it is fixed in to a self-centring jig containing the surrounding lead anode to which the positive connection has already been made. The negative connection is then attached to the central spindle which goes through the pack.
It should be noted that, at this stage, the plating solution is thermostatically controlled to the correct plating temperature, and is agitated by a gentle stream of air which keeps the bath uniform in temperature and solution strength. A "striking" current, which is considerably higher than the normal plating current, is applied for three minutes. after which the current density is reduced to the normal value, and plating proceeds at the rate of approximately 0.001 in. per hour.
Car-engine rings are given a deposit of 0.0025 in. to 0.0035 in., and are kept in the bath for about three hours. Rings for compression-ignition engines have a deposit of 0.004 in. to 0.006 in. and a correspondingly longer plating time is necessary.
The plating operation having been completed and the rings swilled and dried, the thickness of the deposit is checked. The rings are then finished by a light peripheral polishing operation which removes the slight surface roughness found on the "as plated" rings, and makes them satisfactory for roundness as evaluated by the normal light-tightness test.
The reduction in bore and ring wear resulting from the use of chromiumplated rings is believed to arise from the anti-scuffing properties of the chromium-plated film, and is related to the high hardness value (800 minimum Vickers hardness number compared with 250 for cast-iron rings), and the high degree of smoothness of the rings.
In normal cast-iron blocks, chromiumplated rings are expected to reduce the rate of wear to about half that normally experienced with unplated rings, which is the same order of improvement associated with certain liner materials.
Ring Edges Chamfered
All chromium-plated rings are given a small peripheral chamfer. Production requirements necessitate the rings being loaded together, and if of rectangular section there would be a uniform film of chromium covering the length of the pack; this would be broken through in separating the individual rings, leaving a sharp and somewhat ragged edge.
With the peripheral chamfer, the chromium forms a film of uniform thickness on the periphery, but fades out in the chamfers. There is, therefore, no film of chromium to be broken through on the peripheral edge: For car engines, the general practice is to utilize one chromium-plated ring in the top groove of the piston. For compression-ignition engines having four compression-rings, it is recommended that the top two rings be chromium-plated, The plant at present in operation is capable of an output of 10,000 rings per week, and plans are now being prepared for doubling this output. Whilst the diameter of the majority of rings so far plated has not exceeded 6 ins., rings up to 131 ins, diameter can be accommodated, and some batches in the 10-in. to 12-in, range have been so treated.