Pop goes the diesel so it's remake timE
Page 38
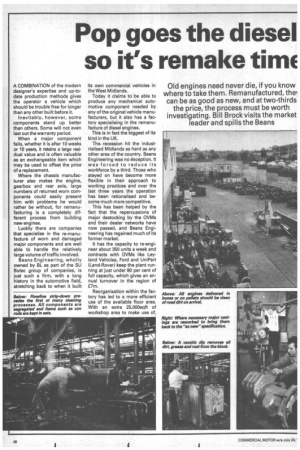
Page 39
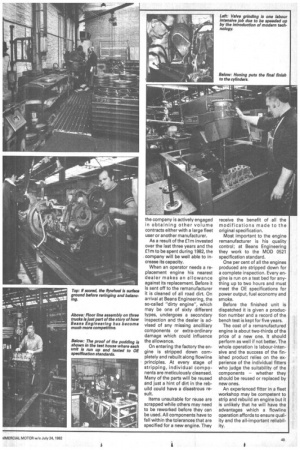
If you've noticed an error in this article please click here to report it so we can fix it.
A COMBINATION of the modern designer's expertise and up-todate production methods gives the operator a vehicle which should be trouble free for longer than any other built before it.
Inevitably, however, some components stand up better than others. Some will not even last out the warranty period.
When a major component fails, whether it is after 10 weeks or 10 years, it retains a large residual value and is often valuable as an exchangeable item which. may be used to offset the price of a replacement.
Where the chassis manufacturer also makes the engine, gearbox and rear axle, large numbers of returned worn components could easily present him with problems he would rather be without, for remanufacturing is a completely different process from building new engines.
Luckily there are companies that specialise in the re-manufacture of worn and damaged major components and are well able to handle the relatively large volume of traffic involved.
Beans Engineering, wholly owned by BL as part of the SU Butec group of companies, is just such a firm, with a long history in the automotive field, stretching back to when it built its own commercial vehicles in the West Midlands.
Today it claims to be able to produce any mechanical automotive component needed by any of the original vehicle manufacturers, but it also has a factory specialising in the remanufacture of diesel engines.
This is in fact the biggest of its kind in the UK.
The. recession hit the industrialised Midlands as hard as any other area of the country. Beans Engineering was no exception. It was forced to reduce its workforce by a third. Those who stayed on have become more flexible in their approach to working practices and over the last three years the operation has been rationalised and become much more competitive.
This has been helped by the fact that the repercussions of major destocking by the OVMs and their dealer networks have now passed, and Beans Engineering has regained much of its former market.
It has the capacity to re-engineer about 350 units a week and contracts with OVMs like Leyland Vehicles, Ford and UniPart (Land-Rover) keep the plant running at just under 80 per cent of full capacity, which gives an annual turnover in the region of £7m.
Reorganisation within the factory has led to a more efficient use of the available floor area. With an extra 25,000sqft of workshop area to make use of, the company is actively engaged in obtaining other volume contracts either with a large fleet user or another manufacturer.
As a result of the Elm invested over the last three years and the Elm to be spent during 1982, the company will be well able to increase its capacity.
When an operator needs a replacement engine his nearest dealer makes an allowance against its replacement. Before it is sent off to the remanufacturer it is cleaned of all road dirt. On arrival at Beans Engineering, the so-called "dirty engine", which may be one of sixty different types, undergoes a secondary inspection and the dealer is advised of any missing ancilliary components or extra-ordinary damage which could influence the allowance.
On entering the factory the engine is stripped down cornpletely and rebuilt along flowline principles. At every stage of stripping, individual components are meticulously cleansed. Many of the parts will be reused and just a hint of dirt in the rebuild could have a disastrous result.
Items unsuitable for reuse are scrapped while others may need to be reworked before they can be used. All components have to fall within the tolerances that are specified for a new engine. They receive the benefit of all the modifications made to the original specification.
Most important to the engine remanufacturer is his quality control; at Beans Engineering they work to the MOD 0521 specification standard.
One per cent of all the engines produced are stripped down for a complete inspection. Every engine is run on a test bed for anything up to two hours and must meet the OE specifications for power output, fuel economy and smoke.
Before the finished unit is dispatched it is given a production number and a record of the bench test is kept for five years.
The cost of a remanufactured engine is about two-thirds of the price of a new one. It should perform as well if not better. The whole operation is labour-intensive and the success of the finished product relies on the experience of the individual fitters who judge the suitability of the components — whether they should be reused or replaced by new ones.
An experienced fitter in a fleet workshop may be competent to strip and rebuild an engine but it is unlikely that he will have the advantages which a flowline operation affords to ensure quality and the all-important reliability.