From the BOEIF by Graham Montgomerie There's other things apart
Page 66
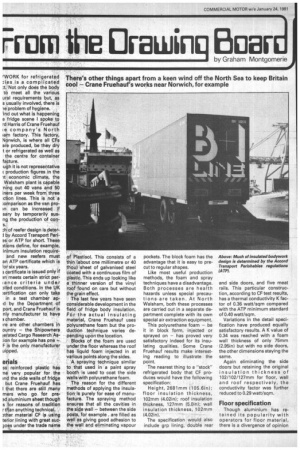
Page 67
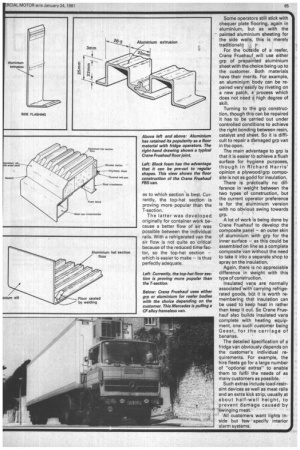
If you've noticed an error in this article please click here to report it so we can fix it.
from a keen wind off the North Sea to keep Britain cool — Crane Fruehauf's works near Norwich, for example 'WORK for refrigerated 3 I e s is a complicated e. Not only does the body to meet all the various ural requirements but, as
s usually involved, there is le problem of hygiene.
'Ind out what is happening e fridge scene I spoke to rd Harris of Crane Fruehauf le company's North !am factory. This factory, Norwich, is where all CFs are produced, be they dry t or refrigerated as well as the centre for container facture.
ugh it is not representative c production figures in the It economic climate, the Walsham plant is capable 'ning out 40 vans and 50 iners per week from three ction lines. This is not a :omparison as the van pro m can be increased if sary by temporarily suing the production of _cops, h of reefer design is deter] by Accord Transport Pen-. as or ATP for short. These ations define, for example, inimum insulation require and new reefers must an ATP certificate which is or six years.
certificate is issued only if an meets certain strict per
lance criteria under Deed conditions. In the uk :ertification can only take in a test chamber apd• by the Department Of port, and Crane Fruehauf is nly manufacturer to have 3 chamber. !re are other chambers in ountry — the Shipowners ierated Cargo Research As7 :ion for example has one F is the only manufacturer uipped.
erials
ss reinforced plastic has ne very popular for the n d the side walls of fridge but Crane Fruehauf has I that there are still Many mers who go for pread aluminium sheet though a for reasons of tradition r filen anything technical. )ther material CF is using tenor lining with great sucdoes under the trade name of Plastisol. This consists of a thin (about one millimetre or 40 thou) sheet of galvanised steel coated with a continuous film of plastic. This ends up looking like a thinner version of the vinyl roof found on cars but without the grain effect.
The last few years have seen considerable development in the field of fridge body insulation. For the actual insulating material, Crane Fruehauf uses polyurethane foam but the production technique varies depending upon the location.
Blocks of the foam are used under the floor whereas the roof has liquid foam injected in at various points along the sides.
A spraying technique similar to that used in a paint spray booth is used to coat the side walls with polyurethane foam.
The reason for the different methods of applying the insulation is purely for ease of manufacture. The spraying method ensures that all the cavities in the side wall — between the side posts, for example. are filled as well as giving good adhesion to the wall and eliminating vapour pockets. The block foam has the advantage that it is easy to precut to regular shapes.
Like most useful production methods, the foam and spray techniques have a disadvantage. Both processes are health hazards unless special precautions are taken. At North Walsham, both these processes are carried out in a separate department complete with its own special air extraction equipment.
This polyurethane foam — be it in block form, injected or sprayed on — has proved very satisfactory indeed for its insulating qualities. Some Crane Fruehauf results make interesting reading to illustrate the point.
The nearest thing to a "stock" refrigerated body that CF produces would have the following specification: Height, 2681mm (105.6in); floor insulation thickness, 102mm (4.02in); roof insulation thickness, 127mm (5.0in); wall insulation thickness, 102mrn (4.02in).
The specification would also include grp lining, double rear and side doors, and five meat rails. This particular construction, according to CF test results, has a thermal conductivity K factor of 0.36 watt/sqm compared with the ATP minimum standard of 0.40 watt/sqm.
Variations in the detail specification have produced equally satisfactory results. A K value of 0.34 was reached with a foam wall thickness of only 75mm (2.95in) but with no side doors, the other dimensions staying the same.
Again eliminating the side doors but retaining the original insulation thickness of 102/102/127mm for floor, wall and roof respectively, the conductivity factor was further reduced to 0.29 watt/sqm.
Floor specification
Though aluminium has retained its popularity with operators for floor material, there is a divergence of opinion as to which section is best. Currently, the top-hat section is proving more popular than the T-section.
The latter was developed originally for container work because a better flow of air was possible between the individual rails. With a refrigerated van the air flow is not quite so critical because of the reduced time factor, so the top-hat section — which is easier to make — is thus perfectly adequate. Some operators still stick with chequer plate flooring, again in aluminium, but as with the painted aluminium sheeting for the side walls, this is merely traditional:!
For the outside of a reefer, Crane Fruehauf will use either grp of prepairfted aluminium sheet with the choice being up to the customer. Both materials have their merits. For example, an aluminium body can be repaired very easity by riveting on a new patch, a' process which does not need a high degree of skill.
Turning to the grp construction, though this can be repaired it has to be carried out under -controlled conditions to achieve the right bonding between resin, catalyst and sheet. So it is difficult to repair a ctamaged grp van in the open.
The main advantage to grp is that it is easier to achieve a flush surface for hygiene purposes, though in RiChard Harris' opinion a plywood/grp composite is not as good for insulation.
There is practically no difference in weight between the two types of construction, but the current operator preference is for the aluniinium version with no obvious swing towards grp.
A lot of work is being done by Crane Fruehauf to develop the composite panel — an outer skin of aluminium With grp for the inner surface — as this could be assembled on line as a complete composite van without the need to take it into a separate shop to spray on the insulation.
Again, there is no appreciable difference in weight with this type of construction.
Insulated vans are normally associated with carrying refrigerated goods, bat it is worth remembering that insulation can be used to keep heat in rather than keep it out. So Crane Fruehauf also builds insulated vans complete with heating equipment, one such customer being Geest, for the carriage of bananas.
The detailed Specification of a fridge van obviously depends on the customer's individual requirements. For example, the hire fleets go for a large number of "optional extras" to enable them to fulfil the needs of as many customers as possible.
Such extras include load-restraint devices as well as meat rails and an extra kick strip, usually at about half-wall height, to prevent damage caused by 'swinging meat: ' All customers want lights inside but few specify interior alarm systems.