What goes on behin closed curtains
Page 56
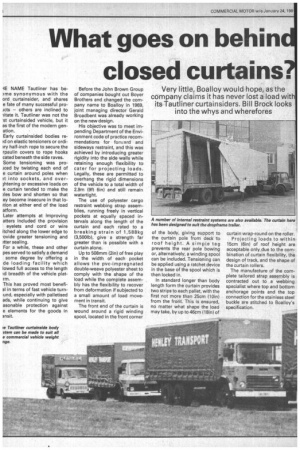
Page 57
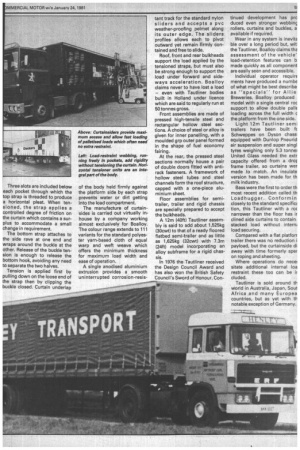
If you've noticed an error in this article please click here to report it so we can fix it.
Very little, Boalloy would hope, as the company claims it has never lost a load with its Tautliner curtainsiders. Bill Brock looks into the whys and wherefores
-IE NAME Tautliner has be)me synonymous with the ord curtainsider, and shares e fate of many successful proacts — others are inclined to .litate it. Tautliner was not the .st curtainsided vehicle, but it as the first of the modern genation.
Early curtainsided bodies re3d on elastic tensioners or ordi3ry half-inch rope to secure the rpaulin covers to rope hooks cated beneath the side raves. Some tensioning was proaced by twisting each end of e curtain around poles when 3t into sockets, and over)htening or excessive loads on e curtain tended to make the )Ies bow and shorten so that ey become insecure in that lotion at either end of the load atform.
Later attempts at improving atters included the provision
eyelets and cord or wire itched along the lower edge to .ovide greater tensioning and 3tter sealing.
For a while, these and other pes served to satisfy a demand some degree by offering a de loading facility which lowed full access to the length id breadth of the vehicle platrm.
This has proved most benefial in terms of fast vehicle turnund, especially with palletised ads, while continuing to give asonable protection against e elements for the goods in ansit. Before the John Brown Group of companies bought out Boyer Brothers and changed the company name to Boalloy in 1969, joint managing director Gerald Broadbent was already working on the new design.
His objective was to meet impending Department of the Environment code of practice recommendations for forv.ard and sideways restraint, and this was achieved by introducing greater rigidity into the side walls while retaining enough flexibility to cater for projecting loads. Legally, these are permitted to overhang the rigid dimensions of the vehicle to a total width of 2.9m (9ft 6in) and still remain watertig ht.
The use of polyester cargo restraint webbing strap assemblies, running freely in vertical pockets at equally spaced intervals along the length of the curtain and each rated to a breaking strain of 1,58 8kg (3,500Ib), give a strength far greater than is possible with a curtain alone.
Up to 508mm (2in) of free play in the width of each pocket allows the pvc-impregnated double-weave polyester sheet to comply with the shape of the load while the complete assembly has the flexibility to recover from deformation if subjected to a small amount of load movement in transit.
The front end of the curtain is wound around a rigid winding spool, located in the front corner of the body, giving support to the curtain pole from deck to roof height. A simple tag prevents the rear pole bowing or, alternatively, a winding spool can be included. Tensioning can be applied using a ratchet device in the base of the spool which is then locked in.
In standard longer than body length form the curtain provides two strips to each pallet, with the first not more than 25cm (10in) from the front. This is ensured, no matter what shape the load may take, by up to 46cm (18in) of curtain wrap-round on the roller.
Projecting loads to within 15cm (6in) of roof height are acceptable only due to the combination of curtain flexibility, the design of track, and the shape of the curtain rollers.
The manufacture of the complete tailored strap assembly is contracted out to a webbing specialist where top and bottom anchorage points and the top connection for the stainless steel buckle are stitched to Boalloy's specification. Three slots are included below each pocket through which the top strap is threaded to produce a horizontal pleat. When tensioned, the strap applies a controlled degree of friction on the curtain which contains a surplus to accommodate a small change in requirement.
The bottom strap attaches to the side rave at one end and wraps around the buckle at the other. Release of the buckle tension is enough to release the bottom hook, avoiding any need to separate the two halves.
Tension is applied first by pulling down on the loose end of the strap then by clipping the buckle closed. Curtain underlap of the body held firmly against the platform side by each strap prevents water or dirt getting into the load compartment.
The manufacture of curtainsides is carried out virtually inhouse by a company working almost exclusively for Boalloy. The colour range extends to 111 variants for the standard polyester yarn-based cloth of equal warp and weft weave which offers the minimum thickness for maximum load width and ease of operation.
A single anodised aluminium extrusion provides a smooth uninterrupted corrosion-resis
tant track for the standard nylon sliders and accepts a pvc weather-proofing pelmet along its outer edge. The sliders profiles allows each to pivot outward yet remain firmly contained and free to slide.
Roof, front and rear bulkheads support the load applied by the tensioned straps, but must also be strong enough to support the load under forward and sideways acceleration. Boalloy claims never to have lost a load — even with Tautliner bodies built in Holland under licence which are said to regularly run at 50 tonnes gross.
Front assemblies are made of pressed high-tensile steel and rectangular hollow steel sections. A choice of steel or alloy is given for inner panelling, with a moulded grp outer panel formed in the shape of fuel economy fairing.
At the rear, the pressed steel sections normally house a pair of double doors fitted with antirack fasteners. A framework of hollow steel tubes and steel channels form the roof structure, capped with a one-piece aluminium sheet.
Floor assemblies for semitrailer, trailer and rigid chassis are specially prepared to accept the bulkheads.
A 12m (40ft) Tautliner assembly is said to add about 1,525kg (30cwt) to that of a ready floored flatbed semi-trailer and as little as 1,625kg (32cwt) with 7.3m (24ft) model incorporating an alloy subframe for a rigid chassis.
In 1976 the Tautliner received the Design Council Award and has also Won the British Safety Council's Sword of Honour. Con
tinued development has pro duced even stronger webbinc_ rollers, curtains and buckles, a available if required.
Wear in any system is inevita ble over a long period but, wit! the Tautliner, Boalloy claims the assessment of the vehicle' load-retention features can b made quickly as all component are easily seen and accessible.
Individual operator requirE ments have produced a numbe of what might be best describe as "specials" for Allie Breweries. Boalloy produced model with a single central roc support to allow double pallE loading across the full width e the platform from the one side.
Light 12m Tautliner semi trailers have been built fr Schweppes on Dyson chassi equipped with Dunlop Pneurid air suspension and super singl tyres weighing only 5.3 tonnel United Glass needed the extr capacity offered from a dror frame trailer, so curtains wer made to match. An insulate version has been made for th • milk industry.
Bass were the first to order th most recent addition called th Loadhugger. Conformin closely to the standard specific,E tion, this Tautliner with a roc narrower than the floor has ir dined side curtains to contain stacked load without interm load securing.
Compared with a flat platforr trailer there was no reduction i payload, but the curtainside di away with time formerly sper on roping and sheeting.
Where operations do necei sitate additional internal loa restraint these too can be if eluded.
Tautliner is sold around th World in Australia, Japan, Sout Africa and many Europea countries, but as yet with th notable exception of Germany.