Standard Plastics Parts Cut Body Costs
Page 62
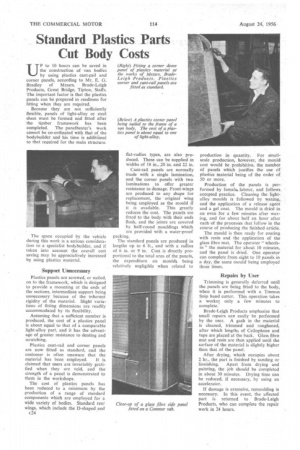
If you've noticed an error in this article please click here to report it so we can fix it.
UP to 10 hours can be saved in the construction of van bodies by using plastics cant-sail and corner panels, according to Mr. E. G. Bradley of Messrs. Brade-Leigh Products, Great Bridge, Tipton, Staffs. The important factor is that the plastics panels can be prepared in readiness for fitting when they are required.
Because they are not sufficiently flexible, panels of light-alloy or steel sheet must be formed and fitted after the timber framework has been completed. The partelbeater's work cannot be co-ordinated with that of the bodybuilder and his time is additional to that required for the main structure.
The space occupied by the vehicle during this work is a serious consideration to a specialist bodybuilder, and if taken into account the overall cost saving may be appreciatively increased by using plastics material.
Support Unnecessary
Plastics panels are screwed, or nailed, on to the framework, which is designed to provide a mounting at the ends of the sections, intermediate support being unnecessary because of the inherent rigidity of the material. Slight variations of fitting dimensions are readily accommodated by its flexibility.
Assuming that a sufficient number is produced, the cost of a plastics panel is about equal to that of a comparable light-alloy part, and it has the advantage of greater resistance to denting and scratching.
Plastics cant-rail and corner panels are now fitted as standard, and the customer is often unaware that the material has been employed. It is claimed that users are invariably gratified when they are told, and the strength of a panel is demonstrated to them in the workshops.
The cost of plastics panels has been reduced to a minimum by the production of a range of standard components which are employed for a wide variety of bodies. Standard rear wings, which include the D-shaped and
c24 flat-radius types, are also produced. These can be supplied in widths of 18 in.„20 in. and 22 in.
Cant-rail panels are normally Made with a single lamination, and the corner panels with two laminations to offer greater resistance to damage, Frontwings are produced to any shape for replacement, the • original wing being employed as the mould if it is available. This greatly reduces the cost. The panels are fitted to the body with their ends flush, and the joints are covered by half-round mouldings which are provided with a water-proof packing.
The standard panels are produced in lengths up to 6 ft., and with a ralius of 6 in. or 9 in. Cost is directly proportional to the total area of the panels, the expenditure on moulds being relatively negligible when related :o production in quantity. For smallscale production, however, the mould cost would be prohibitive, the number of panels which justifies the use of plastics material being of the order of 50 or more.
Production of the panels is performed by female, labour, and follows accepted practice. Cleaning the lightalloy moulds is followed by waxing, and the application of a release agent and a gel coat. The mould is dried in an oven for a few minutes after waxing, and for about half an hour after each of the processes that follow in the course of producing the finished article.
The mould is then ready for coating with resin and the application of the glass fibre mat. The operator "wheelsin" the material for about 10 minutes, and the panel is dried. One operator can complete from eight to 10 panels in a day, the same mould being employed three times.
Repairs by User Trimming is generally deferred until the panels are being fitted to the body, when it is performed with a Tinman Snip hand cutter. This operation takes a worker only a few minutes to complete.
Brade-Leigh Products emphasize that small repairs can easily be performed by the user. A gash in the material is cleaned, trimmed and roughened, after which lengths of Cellophane and tape are placed at the back. Glass fibre mat and resin are then applied until the surface of the material is slightly higher than that of the panel.
After drying, which occupies about 2 hr., the part is finished by sanding or linnishing. Apart from drying and painting, the job should be completed in about 30 minutes. Drying time can be reduced, if necessary, by using an accelerator.
If damage is extensive, remoulding is necessary. In this event, the affected part is returned to Brade-Leigh Products, who can complete the repair work in 24 hours.