Marked Progress in New
Page 42
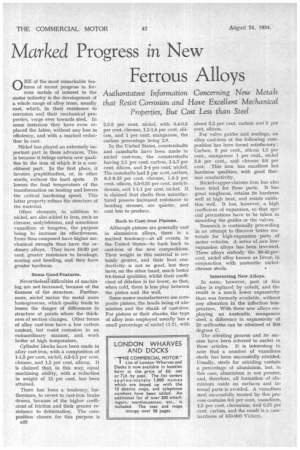
Page 43
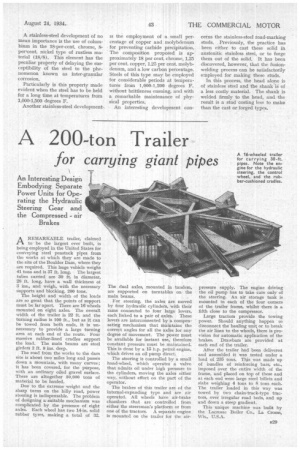
If you've noticed an error in this article please click here to report it so we can fix it.
Ferrous Alloys
Authoritative Information Concerning New Metals that Resist Corrosion and Have Excellent Mechanical Properties, But Cost Less than Steel
0 NE of the most remarkable features of recent progress in ferrous metals of interest to the motor industry is the development of a whole range of alloy irons, usually cast, which, in their resistance to corrosion and their mechanical properties, verge ever towards steel. In some instances they have even replaced the latter, without any loss in efficiency, and with a marked reduction in cost.
Nickel has played an extremely important part in these advances. This is because it brings certain new qualities to the iron of which it is a constituent part. In the first place, it favours graphitization, or, in other words, reduces the hard spots. It lowers the final temperature of the transformation on heating and lowers the critical hardening speed. This latter property refines the structure of the material.
Other elements, in addition to nickel, are also added to iron, such as chrome, molybdenum, and sometimes vana dium or tungsten, the purpose being 'to increase its effectiveness. Irons thus composed have higher mechanical strength than have the ordinary alloys. They have 10-20 per cent. greater resistance to breakage, scoring and bending, and they have greater hardness.
Some Good Features.
Neverthelesirdifficulties of machining are not increased, because of the fineness of the structure. Furthermore, nickel makes the metal more homogeneous, which quality tends to lessen the danger of differences in structure at points where the thickness of section changes. Other forms of alloy cast-iron have a low carbon content, but resist corrosion in an extraordinary manner, and work better at high temperature.
Cylinder blocks have been made in alloy cast-iron, with a composition of 1-1.5 per cent. nickel, 0.3-0.5 per cent. chrome, and 1.5 per cent silicon. It is claimed that, in this way, equal machining ability, with a reduction in weight of 15 per cent, has been attained.
There has been a tendency, furthermore, to revert to cast-iron brake drums, because of the higher coefficient of friction and their greater resistance to deformation. The composition chosen for this purpose is B28 2.5-3 per cent, nickel, with 0.4-0.6 per cent. chrome, 1.5-1.8 per cent, silicon, and 1 per cent, manganese, the carbon percentage being 2.8.
In the United States, countershafts and camshafts have been made in nickel cast-iron, the countershafts having 2.5 per cent. carbon, 1-15 per cent, silicon, and 3-4 per cent. nickel. The camshafts had 3 per cent carbon, 0.2-0.25 per cent. chrome, 1.8-2 per cent. silicon, 0.3-0.35 per cent, molybdenum, and 1-1.1 per cent, nickel. It is claimed that shafts thus manufactured possess increased resistance to bending stresses, are quieter, and cost less to produce.
Back to Cast-iron Pistons.
Although pistons are generally cast in aluminium alloys, there is a marked tendency—at all events, in the United States—to hark back to cast-iron of the new compositions. Their weight in this material is certainly greater, and their heat conductivity is not so good, but they have, on the other hand, much better frictional qualities, whilst their coefficient of dilation is far lower, so that, when cold, there is less play between the piston and the wall.
Some motor manufacturers use composite pistons, the beads being of aluminium and the shank of cast-iron. For pistons or their shanks, the type of alloy iron employed usually has a small percentage of nickel (1-2), with
about 3.5 per cent, carbon and 3 per cent. silicon.
For valve guides and seatings, an alloy cast-iron of the following composition has been found satisfactory : Carbon, 3 per cent., silicon 1.5 per cent., manganese 1 per cent., nickel 3.8 per cent., and chrome 0.8 per cent. This iron has excellent hot hardness qualities, with good thermal conductivity.
Nickel-copper-chrome iron has also been tried for these parts. It has great toughness, retains its hardness well at high heat, and resists oxidation well. It has, however, a high coefficient of expansion, so that special precautions have to be taken in mounting the guides or the valves.
Research is continually proceeding in an attempt to discover better materials for high-expansion parts of motor vehicles. A series of new lowexpansion alloys has been invented. These alloys embody the 3642-percent nickel alloy known as Invar, in conjunction with austenitic nickel chrome steels. • Interesting New Alloys.
In some, however, part of this alloy is replaced by cobalt, and the result is a much lower expansivity than was formerly available, without any alteration in the inflection temperature. With these new alloys employing an austenitic manganese -steel, a difference in expansivity of 20 millionths can be obtained at 300 degrees C.
The nitriding process and its success have been referred to earlier in these articles. It is interesting to note that a number of vanadium steels has been successfully nitrided. Usually, steels for nitriding contain a percentage of aluminium, but, in this case, aluminium is not present, and, therefore, all formation of aluminium oxide on surfaces and internal parts is avoided. A vanadium steel successfully treated by this process contains 0.6 per cent. vanadium, L5 per cent, chromium, and 0.25 per cent, carbon, and the result is a casehardness of 850-000 Vickers. A stainless-steel development of no mean importance is the use of columbium in the 18-per-cent. chrome, 8pevcent. nickel type of rustless material (18/8). This element has the peculiar property of delaying the susceptibility of the steel to the phenomenon known as inter-granular corrosion, Particularly is this property made evident when the steel has to be held for a long time at temperatures from 1,000-1,500 degrees F.
Another stainless-steel development, is the employment of a small percentage of copper and molybdenum for preventing carbide precipitation. The composition proposed is approximately 18 per cent. chrome, 1.25 per cent. copper, 1.25 per cent, molybdenum, and a low carbon percentage. Steels of this type may be employed for considerable periods at temperatures from 1,000-1,200 degrees F. without brittleness ensuing, and with a remarkable maintenance of physical properties.
An interesting development con
cerns the stainless-steel road-marking studs. Previously, the practice has been either to cast these solid in austenitic stainless steel, or to forge them out of the solid. It has been discovered, however, that the fusionwelding process can be satisfactorily employed for making these studs.
In this process, the head alone is of stainless steel and the shank is of a less costly material. The shank is welded firmly to the head, and the result is a stud costing less to make than the cast or forged types.