Cutting Lorry-body Weight with Safety
Page 50
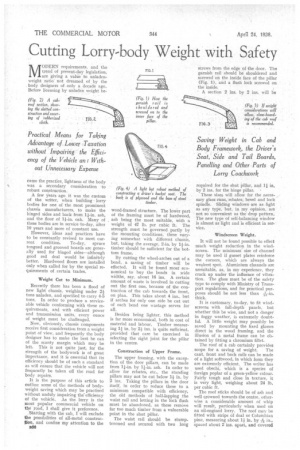
Page 51
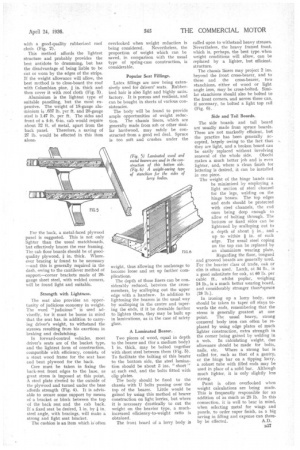
If you've noticed an error in this article please click here to report it so we can fix it.
MODERN requirements, and the trend of present-day legislation, are giving a value to unladenweight ratio not dreamed of by the body designers of only a decade ago. Before licensing by unladen weight be
came the practice, lightness of the body was a secondary consideration to robust construction.
A few years ago it was the custom of the writer, when building • lorry bodies for one of the most prominent chassis manufacturers, to make the hinged sides and back from 11-in, ash, and the floor of 11-in. oak. Many of these bodies are in service to-day, after 10 years and more of constant use.
However, ideas and practices have to be constantly revised to meet current condition. To-day, spruce tongued and grooved boards are generally used for hinged sides—although good red deal would be infinitely better. Hardwood floors are installed only when called for by the special requirements of certain trades.
Weight Cut to Minimum.
Recently there has been a flood of new light chassis, weighing under 21 tons unladen, and specified to carry 4-5 tons. In order to produce a serviceable vehicle conforming with these requirements, and with efficient power and transmission units, every ounce of weight must be challenged.
Now, obviously, chassis components receive first consideration from a weight point of view, and frequently the body designer has to make the best he can of the scanty margin which may be left. This is not quite just, for the strength of the bodywork is of great importance, and it is essential that its efficiency .should be of such a standard as will ensure that the vehicle will not frequently be taken off the road for body repairs.
It is the purpose of this article to outline some of the methods of bodyweight saving which may be practised without unduly impairing the efficiency of the vehicle. As the lorry is the most popular commercial vehicle on the road, I shall give it preference.
Starting with the cab, I will exclude the possibilities of all-metal construction,• and confine my attention to the 11216
wood-framed stru,cture. The lower part of the framing must be of hardwood, ash being the most suitable, with a weight of 47 lb. per cubic ft. The strength must be governed partly by the mounting conditions, these varying somewhat with different chassis, but, taking the average, 2-in. by 11-in_ timber should be sufficient for the bottom frame.
By cutting the wheel-arches out of a bend, a saving of timber will be effected. It will be found most economical to buy the bends in wide widths, say, about 16 ins. A certain amount of waste is involved in cutting out the first one, because of the contraction of the cab towards the front, on plan. This takes about 4 ins., but if arches for only one side be cut out of each bend one wastage serves for all.
Besides being lighter, this method is far more economical, both in cost of material and labour. Timber measuring 11 in. by 21 ins, is quite sufficient, provided that care be exercised in selecting the right joint for the pillar in the centre.
Construction of Upper Frame.
The upper framing, with the exception of the door pillars, can be made from 11-in. by II-in. ash. In order to allow for rebates, etc., the standing pillars may not be cut below 11 in. by 2 ins. Taking the pillars in the door itself, in order to reduce these to a minimum compatible with efficiency, the old methods of half-lapping the waist rail and letting in the lock flush must be abandoned, as these remove far too much timber from a vulnerable point in the shut pillar.
The waist rail should be stumptenoned and secured with two long required for the shut pillar, and 11 in. by 2 ins, for the hinge pillar.
These sizes will allow for the necessary glass runs, rebates, bevel and lock spindle. Sliding windows are as light as any type, but, in my opinion, are not so convenient as the drop pattern. The new type of self-balancing window is almost as light and is efficient in service.
Windscreen Weight.
It will not be found possible to effect much weight reduction in the windscreen. The minimum size of channel may be used if gusset plates reinforce the corners, which are always the weakest spot. Aluminium channels are unsuitable, as, in my experience, they crack up under the influence of vibration. The glass must be of the safety type to comply with Ministry of Transport regulations, and for practical purposes should be not less than +6-in. thick.
It is customary, to-day, to fit windscreens with full-depth panels, but whether this be wise, and not a danger in foggy weather, is extremely doubtful. A little weight may possibly be saved by mounting the fixed glasses direct in the wood framing, and the illusion of a metal frame can be obtained by fitting a chromium fillet.
The roof of a cab certainly provides scope for a saving of weight. The cant, front and back rails can be made of a light softwood, in which form they are extremely efficient. The writer has used obechi, which is a species of foreign poplar of a green-yellow colour. Fairly tough and close in texture, it is very light, weighing about 24 lb. per cubic ft.
The roof sticks should be of ash and well c_rowned towards the centre, otherwise a considerable amount of whip will result, particularly when used on an oil-engined lorry. The roof may be fitted with strips of deal or Columbian pine, measuring about 11 in. by 1.56
spaced about 2 ins. apart, and covered with a good-quality rubberized roof cloth (Fig. 2).
This method affords the lightest structure and probably provides the best antidote to drumming, but has the disadvantage of being liable to be cut or worn by the edges of the strips. If the weight allowance will allow, the best method is to close-board the roof with Columbian pine, in. thick and then cover it with roof cloth (Fig. 3).
Aluminium is the lightest type of suitable panelling, but the most expensive. The weight of 18-gauge aluminium is .637 lb. per ft. and 20-gauge steel is 1.47 lb. per ft. The sides and front of a 4-ft. 6-in, cab would require about 32 ft. of metal, apart from the back panel. Therefore, a saving of 27 lb. would be effected in this item alone.
For the back, a metal-faced plywood panel is suggested. This is not only lighter than the usual matchboards, but effectively braces the rear framing. The cab floor boards should be of goodquality plywood, in. thick. Whereever bracing is found to be necessary —and this is generally required in the dash, owing to the cantilever method of support—corner brackets made of 20gauge sheet steel, with welded corners, will be found light and suitable.
Strength with Lightness.
The seat also provides an opportunity of judicious economy in weight. The word " judicious " is used advisedly, for it must be borne in mind that the seat has, in addition to carrying driver's weight, to withstand the stresses resulting from his exertions in braking and declutching.
In forward-control vehicles, most driver's seats are of the bucket type, and the lightest form of construction, compatible with efficiency, consists of a stout wood frame for the seat base and bent plywood for the back.
Care must be taken in fixing the back-rest front edges to the base, as great stress is imposed at this point. A steel plate riveted to the outside of the plywood and turned under the base affords strength (Fig. 4). It is advisable to secure some support by means of a bracket or block between the top of the back rest and the cab back. If a fixed seat be desired, 1 in. by in. steel angle, with bracings, will make a strong and light seat bracket.
The cushion is an item which is often overlooked when weight reduction is being considered. Nevertheless, the proportion of weight which can be saved, in comparison with the usual type of spring-case construction, is considerable.
Popular Seat Fillings.
Latex fillings are now being extensively used for drivers' seats. Rubberized hair is also light and highly satisfactory. It is porous and resilient, and can be bought in sheets of various consistencies.
The body will be found to provide ample opportunities of weight reduc tion. The chassis liners, which are generally made from ash or other similar hardwood, may safely be constructedfrom a good red deal. Spruce is too soft and crushes under the weight, thus allowing the anchorage to become loose and set up further complications.
The depth of these liners can be considerably reduced, between the crossmembers, by scalloping out the upper edge with a handsaw. In addition to lightening the bearers in the usual way by scalloping in the centre and tapering the ends, if it be desirable further to lighten them, they may be built up. in laminations, as in the case of safety glass.
A Laminated Bearer.
Two pieces of wood, equal in depth to the bearer and (for a medium body) 1 in. thick. may be bolted together with sheet steel between them (Fig. 5). To facilitate the bolting of this beater to the bottom side, the steel lamination should be about 3 ins. " short " at each end, and the bolts fitted with clip plates.
The body should be fixed to the chassis with U bolts passing over the top of the bearer. Little would be gained by using this method of bearer construction on light lorries, but where it is necessary drastically to cut the weight on the heavier type, a muchincreased efficiency-to-weight ratio is obtained.
The front board of a lorry body is called upon to withstand heavy stresses. Nevertheless, the heavy framed front, which is, perhaps, the best type when weight conditions will allow, can be replaced by a lighter, but efficient, structure.
The chassis liners may project 2 ins. beyond the front cross-bearer, and to these and the cross-bearer, two stanchions, either of wood or light angle iron, may be cross-bolted. Similar stanchions should also be bolted to the front corners, and across these can, if necessary, be bolted a light top rail (Fig. 6).
Side and Tail Boards.
The side boards and tail board are usually made from spruce boards. These are not markedly efficient, but the practice has been generally accepted, largely owing to the fact that they are light, and a broken board can be easily replaced without involving renewal of the whole side. Obechi makes a much better job and is even lighter, and, where a clean finish for lettering is desired, it can be installed in one piece.
The weight of the hinge bands can be minimized by employing a light section of steel channel for the legs, welding on the hinge bosses. The top edges and ends should be protected with steel channels, the end ones being deep enough to allow of bolting through. The bottom or fixed sides can be lightened by -scalloping out to a depth of about in., and up to within in. of each edge. The usual steel coping on the top can be replaced by an aluminium wearing plate.
Regarding the floor, tongued and grooved boards are generally ured. For the heavier class of trade, oak Or elm is often used. Larch, at 34 lb., is a good substitute for oak, at 60 lb. per cubic ft., whilst poplar, weighing 24 lb., is a much better wearing hoard, and considerably stronger than-' spruce (28 lb.).
In ironing up a lorry body, care should be taken to taper off stays towards the ends, remembering that the stress is generally greatest at one point. The usual heavy, strong cornered body iron can often be replaced by using edge plates of much lighter construction, extra strength in the corner being gained by welding in a web. In calculating weight, due allowance should be made for bolts, nails, etc. Where a strong bar is called for, such as that of a gantry, or the hinge bar• on a tipping lorry, a robust tube with filled ends may be used in place of a solid bar. Although much lighter, it is only slightly less strong.
Paint is often overlooked when weight calculations are being made. This is frequently responsible for an addition of as much as 28 lb. In this connection, it is well to bear in mind, when selecting metal for wings and panels, to order super finish, as a big saving in filling and expense can there by be effected. A.D.