BRAKING EQUIPMENT FOR 5,000 VEHICLES A WEEK
Page 72
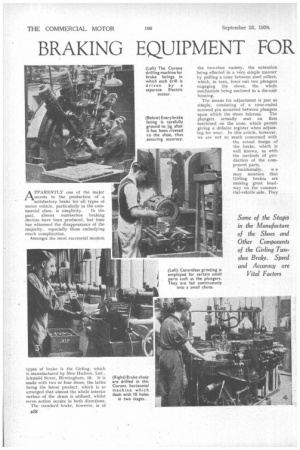
Page 73
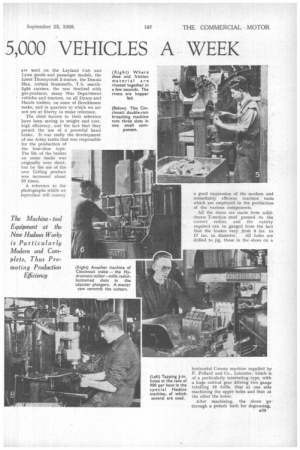
Page 74
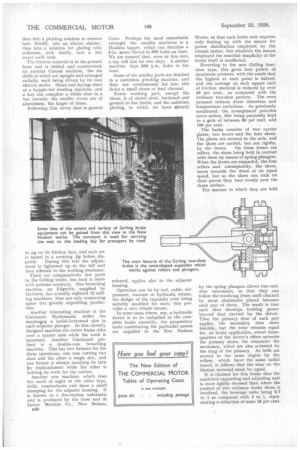
If you've noticed an error in this article please click here to report it so we can fix it.
APPARENTLY one of the major secrets in the production of a satisfactory brake for all types of motor vehicle, particularly in the com
mercial class, is simplicity. In the past, almost numberless braking devices have been produced, but time has witnessed the disappearance of the majority, especially those embodying much complication.
Amongst the most successful modern types of brake is the Girling, which is manufactured by New Hudson, Ltd., Icknield Street, Birmingham, 18. It is made with two or four shoes, the latter being the latest product, which is so arranged that almost the whole interior surface of the drum is utilized, whilst servo action occurs in both directions.
The standard brake, however, is of the two-shoe variety, the extension being effected in a very simple manner by pulling a cone between steel rollers. which, in turn, force out two plungers engaging the shoes, the whole mechanism being enclosed in a die-cast housing.
The means for adjustment is just as simple, consisting of a cone-ended screwed pin mounted between plungers upon which the shoes fulcrum. The plungers actually seat on flats machined on the cone, which permit giving a definite register when adjusting for wear. In this article, however, we are not so much concerned with the actual design of the brake, which is well known, as with the methods of production of the component parts.
Incidentally, w e
may mention that Girling brakes are making great headway on the commercial-vehicle side. They are used on the Leyland Cub and Lynx goods and passenger models, the latest Thornycroft 2-tonner, the Dennis Max, certain Scammells, T.S. searchlight carriers, the new Sentinel with gas-producer, many War Department vehicles and tractors, on all Dyson and Hands trailers, on some of Brockhouse make, and in quarters to which we are not yet at liberty to make reference.
The chief factors in their selection have been saving in weight and cost, high efficiency, and the fact that they permit the use of a powerful hand brake. It was really the development of our Army tanks that was responsible for the production of the four-shoe type. The life of the brakes on some tanks was originally very short, but by the use of the new Girling product was increased about 10 times.
• A reference to the photographs which we reproduce will convey a good impression of the modern and remarkably efficient machine tools which are employed in the production of the various components.
All the shoes are made from soliddrawn T-section steel pressed to the correct radius, and the variety required can be gauged from the fact that the brakes vary from 6 ins. to
17 ins, in diameter. All holes are drilled to jig, those in the shoes on a horizontal Corona machine supplied by F. Pollard and Co., Leicester, which is of a particularly interesting type, with a huge central gear driving two gangs totalling 10 drills, that at one side machining the upper holes and that at• the other the lower,
After machining, the shoes go. through a potash bath for degreasing,
then into a pickling solution to remove rust, thirdly, into an electro cleaner, then into a solution for plating with cadmium, and, finally, into a hot water swill tank, The friction material is in die-pressed form and is drilled and countersunk on another Corona machine, the six drills of which are upright and arranged radially, each being driven by its own electric motor. Shoes and facings meet at a hopper-fed riveting machine, and a boy can complete a whole shoe in a few seconds; the smaller rivets are of aluminium, the larger of brass.
Following this, every shoe is ground
to jig on its friction face, and each set is tested in a centring jig before dis patch. During this test the adjustment is tightened up to the full and then released to the working clearance.
There are comparatively few parts in the Girling brake, but each is made with extreme accuracy. One broaching machine, an Edgwick, supplied by Herberts, has actually replaced 12 milling machines, thus not only conserving space but 'greatly expediting production.
Another interesting machine is the Cincinnati Hydromatic miller for machiring a radial-bottomed slot in each adjuster plunger. In this cleverly designed machine the cutter frame rides over a master cam while the work is traversed. Another Cincinnati product is a double-ram broaching machine. This has two fixtures for the three operations, one ram cutting two slots and the other a single slot, and one fixture is always awaiting its turn for replenishment while the other is holding its work for the cutters.
Another new machine, which does the work of eight of the older type, drills, counterbores and faces a small stamping for the adjuster housing. It is known as a five-station automatic and is produced by the Goss and de Leeuw Machine Co., New Britain, B40
Conn. Perhaps the most remarkable amongst the smaller machines is a Haskins tapper, which can machine a f-in. screw thread in DOO holes an hour. We are assured that, even at this rate, a tap will last for two days. A similar machine taps 600 Fin, holes in the hour.
Some of the smaller parts are finished in a centreless grinding machine, and they are continuously fed into this down a small chute or feed channel.
Every working part, except the shoes, is of nickel steel, hardened and ground to line limits, and the cadmium plating, to which we have already referred, applies also to the adjuster housing.
Operation can be by rod, cable, airpressure, vacuum or hydraulic means, the design of the expander cone being suitably modified for each; this provides a very simple means.
In some cases where, say, a hydraulic device is to be embodied in the complete brake assembly, the proprietary units constituting the particular means are supplied to the New Hudson Works, so that each brake unit requires only linking up with the means for power distribution employed by the chassis maker, but whatever the means employed the essential simplicity of the brake itself is unaffected.
Reverting to the new Girling fourshoe type, this gives four points of maximum pressure, with the result that the highest at each point is halved, and the average on each square inch of friction material is reduced by over 40 per cent., as compared with the ordinary two-shoe pattern. The even pressure reduces drum distortion and temperature variations. As previously mentioned, the arrangement provides servo action, this being purposely kept to a gain of between 80 per cent. and 100 per cent.
The brake consists of two carrier plates, two levers and the four shoes. The plates are secured to the axle, and the shoes are carried, but not rigidly, by the levers. On these levers are rollers, the shoes being held in contact with these by means of spring plungers. When the levers are expanded, the four rollers and, consequently, the shoes, move towards the drum. at an equal speed, but as the shoes can rock on their pivots they bear evenly over the drum surface.
The manner in which they are held
by the spring plungers allows free endwise movement, so that they can follow the revolving drum until checked by stout abutments placed between each pair of shoes. The result is that each shoe develops braking power beyond that exerted by the driver. Then the primary shoe of each pair applies the secondary shoe more forcibly, but the wear remains equal for, on brake application, about threequarters of the driver's effort actuates the primary shoes, the remainder the secondary, which are also actuated by the drag of the primary. As both are moved to the same degree by the rollers, which have the same radial travel, it follows that the wear on the friction material must he equal.
It is claimed for this brake that the combined expanding and adjusting unit is more lightly stressed than where the control of two ordinary brake shoes is involved, the leverage ratio being 2.7 to 1 as compared with 2 to 1, representing a reduction of some 35 per cent.