Three-minute Turn-round for 6/7-tonners
Page 26
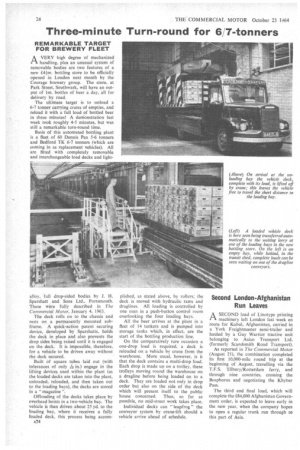
If you've noticed an error in this article please click here to report it so we can fix it.
REMARKABLE TARGET FOR BREWERY FLEET
AVERY high degree of mechanized handling, plus an unusual system of removable bodies are two features of a new f4lsin. bottling store to be officially opened in London next month by the Courage brewery group. The store, at Park Street, Southwark, will have an output of lm. bottles of beer a day, all for delivery by road.
The ultimate target is to unload a 6-7 tonner carrying crates of empties, and reload it with a full load of bottled beer in three minutes! A denionstration last week took roughly 4-5 minutes, but was still a remarkable turn-round time.
Basis of this automated bottling plant is a fleet of 60 Dennis Pax 5-6 tonners and Bedford TK 6-7 tonners (which are coming in as replacement vehicles). All are fitted with completely removable and interchangeable load decks and light
alloy, full drop-sided bodies by J. H. Sparshatt and Sons Ltd., Portsmouth. These were fully described in The Commercial Motor, January 4, 1963.
The deck rolls on to the chassis and rests on a permanently mounted subframe. A quick-action patent securing device, developed by Sparshatts, holds the deck in place and also prevents the drop sides being raised until it is engaged on the deck. It is impossible, therefore, for a vehicle to be driven away without the deck secured.
Built of square tubes laid out (with tolerances of only sly in.) engage in the lifting devices used within the plant (as the loaded decks are taken into the plant, unloaded, reloaded, and then taken out to the loading bays), the decks are stored in a "magazine ".
Offloading of the decks takes place by overhead hoists in a two-vehicle bay. The vehicle is then driven about 25 yd. to the loading bay, where it receives a fully loaded deck, this process being accom
A24 plished, as stated above, by rollers; the deck is moved with hydraulic rams and draglines. All loading is controlled by one man in a push-button control room overlooking the four loading bays.
All the beer arrives at the plant in a fleet of 14 tankers and is pumped into storage tanks which, in effect, are the start of the bottling production line.
On the comparatively rare occasion a one-drop load is required, a deck is reloaded on a vehicle by crane from the warehouse. More usual, however, is it that the deck contains a multi-drop load. Each drop is made up on a trolley, these trolleys moving round the warehouse on a dragline before being loaded on to a deck. They are loaded not only in drop order but also on the side of the deck which will present itself to the public house concerned. Thus, so far as possible, no mid-street work takes place.
Individual decks can " leapfrog " the conveyor system by crane-lift should a vehicle arrive ahead of schedule.