An Ingenious Pipe Coupling
Page 58
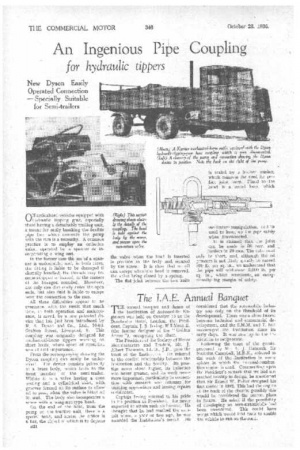
If you've noticed an error in this article please click here to report it so we can fix it.
for hydraulic tippers
New Dyson Easily Operated Connection — Specially Suitable for Semi-trailers
ON articulated vehicles equipped with hydraulic tipping gear, especially those having a detachable trailing unit, a means for easily breaking the flexible pipe line which connects the pump with the ram is a necessity. A common practice is to employ an orthodox union, operated by a spanner or incorporating a wing nut.
In the former case the use of a spanner is undesirable, and, in both cases, the fitting is liable to be damaged if clumsily handled; the threads may become stripped or burred, or the corners of the hexagon rounded. Moreover, not only can dirt easily enter the open ends, but also fluid is liable to escape from the connection to the ram.
All these difficulties appear to be overcome, with the result that much time, in both operation and maintenance, is saved, by a new patented device that has just been introduced by R. A. Dyson and Co., Ltd., 76-80, Grafton Street, Liverpool, 8. This coupling was originally designed for mechanical-horse tippers working on short hauls, where speed of operation was of first importance.
From the accompanying drawing the Dyson coupling can easily be understood. The device consists primarily of a brass body, which bolts to the front member of the semi-trailer. Within it is a valve having a cone seating and a cylindrical skirt, with grooves formed on its surface to allow" oil to pass, when the valve is lifted off its seat. The body also incorporates a screw with a wing-nut-type head.
On the end of the hose, from the pump on the tractive unit, there is a special heal, and across the orifice is a bar, the object of which ii to depress B24
the valve when the head is inserted in position in the body and secured by the screw. It is clear that no oil can escape whewthe head is removed, the valve being closed by a .spring.
The flat joint between the two units
facilitates,. manipulation, and 'is used to hang up the pipe safely when disconnected.
It is claimed that the joint can be made in 30 secs, and broken in 20 secs. The tube need only be short, and, although the oil pressure is not likely greatly to exceed 800 lb. per sq. in., we understand that the pipe will withstand 3,000 lb. per sq. in., which represents_ an exceptionally big margin of safety.