THE FAD BREAK RS
Page 46
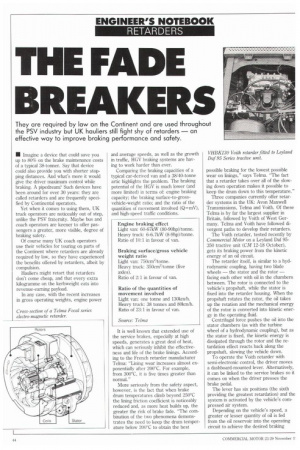
Page 47
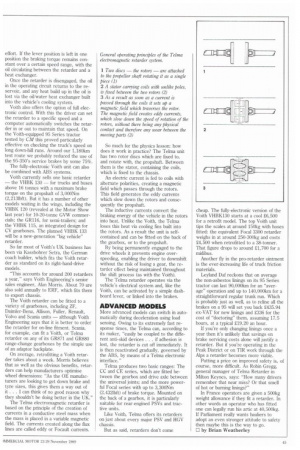
If you've noticed an error in this article please click here to report it so we can fix it.
They are required by law on the Continent and are used throughout the PSV industry but UK hauliers still fight shy of retarders — an effective way to improve braking performance and safety.
• Imagine a device that could save you up to 80% on the brake maintenance costs of a typical 38-tonner. Say that device could also provide you with shorter stopping distances. And what's more it would give the driver maximum control while braking. A pipedream? Such devices have been around for over 30 years: they are called retarders and are frequently specified by Continental operators.
Yet when it comes to using them, UK truck operators are noticeably out of step, unlike the PSV fraternity. Maybe bus and coach operators are keener to offer passengers a greater, more visible, degree of braking safety.
Of course many UK coach operators use their vehicles for touring on parts of the Continent where retarders are already required by law, so they have experienced the benefits offered by retarders, albeit by compulsion.
Hauliers might retort that retarders don't come cheap, and that every extra kilogramme on the kerbweight eats into revenue-earning payload.
In any case, with the recent increases in gross operating weights, engine power and average speeds, as well as the growth in traffic, HGV braking systems are having to work harder than ever.
Comparing the braking capacities of a typical car-derived van and a 38/40-tonne artic highlights the problem. The braking potential of the HGV is much lower (and more limited) in terms of: engine braking capacity; the braking surface-to-grossvehicle-weight ratio; and the ratio of the quantities of movement involved (Q=mV), and high-speed traffic conditions.
It is well known that extended use of the service brakes, especially at high speeds, generates a great deal of heat, which can seriously inhibit the effectiveness and life of the brake linings. According to the French retarder manufacturer Telma: "Lining wear increases almost exponentially after 200°C. For example, from 300°C, it is five times greater than normal."
More seriously from the safety aspect, however, is the fact that when brake drum temperatures climb beyond 250°C the lining friction coefficient is noticeably reduced and, as more heat builds up, the greater the risk of brake fade. "The combination of the two phenomena demonstrates the need to keep the drum temperature below 200°C to obtain the best possible braking for the lowest possible wear on linings," says Telma. "The fact that a retarder takes over all of the slowing down operation makes it possible to keep the drum down to this temperature."
Three companies currently offer retarder systems in the UK: Avon Maxwell Transmissions, Telma and Voith. Of these Telma is by far the largest supplier in Britain, followed by Voith of West Germany. Telma and Voith have followed divergent paths to develop their retarders.
The Voith retarder, tested recently by Commercial Motor on a Leyland Daf 95350 tractive unit (CM 12-18 October), gets its braking power from the kinetic energy of an oil circuit.
The retarder itself, is similar to a hydrodynamic coupling, having two blade wheels — the stator and the rotor — facing each other with oil in the chambers between. The rotor is connected to the vehicle's propshaft, while the stator is fixed into the retarder housing. When the propshaft rotates the rotor, the oil takes up the rotation and the mechanical energy of the rotor is converted into kinetic energy in the operating fluid.
Centrifugal force pushes the oil into the stator chambers (as with the turbine wheel of a hydrodynamic coupling), but as the stator is fixed, the kinetic energy is dissipated through the rotor and the retardation effect reacts back along the propshaft, slowing the vehicle down.
To operate the Voith retarder with semi-electronic control, the driver moves a dashboard-mounted lever. Alternatively, it can be linked to the service brakes so it comes on when the driver presses the brake pedal.
The lever has six positions (the sixth providing the greatest retardation) and the system is activated by the vehicle's compressed air system.
Depending on the vehicle's speed, a greater or lesser quantity of oil is fed from the oil reservoir into the operating circuit to achieve the desired braking effort. lithe lever position is left in one position the braking torque remains constant over a certain speed range, with the oil circulating between the retarder and a heat exchanger.
Once the retarder is disengaged, the oil in the operating circuit returns to the reservoir, and any heat build up in the oil is lost via the oil/water heat exchanger built into the vehicle's cooling system.
Voith also offers the option of full electronic control. With this the driver can set the retarder to a specific speed and a computer automatically switches the retarder in or out to maintain that speed. On the Voith-equipped 95 Series tractor tested by CM this proved particularly effective on checking the truck's speed on long down-hill runs. Around our 1,1801un test route we probably reduced the use of the 95-350's service brakes by some 75%.
The fully-electronic Voith unit can also be combined with ABS systems.
Voith currently sells one basic retarder — the VHBK 130 — for trucks and buses above 16 tonnes with a maximum brake torque on the propshaft of 3,000Nm (2,2131bft). But it has a number of other models waiting in the wings, including the VHBK 120 (revealed at the Motor Show last year) for 10-20-tonne GVW commercials; the GR116, for semi-trailers; and the VHBK 115, an integrated design for CV gearboxes. The planned VHBK 133 will be a new-generation "big vehicle" retarder.
So far most of Voith's UK business has been via Kassbohrer Setra, the German coach builder, which fits the Voith retarder as standard on its right-hand-drive models.
"This accounts for around 200 retarders a year," says Voith Engineering's senior sales engineer, Alan Morris. About 70 are also sold annually to ERF, which fits them to export chassis.
The Voith retarder can be fitted to a variety of gearboxes, including ZF, Daimler-Benz, Allison, Fuller, Renault, Volvo and Scania units — although Voith Engineering says that it is better to order the retarder for on-line fitment. Scania, for example, can fit a Voith, or Telma retarder on any of its GR871 and GR880 range-change gearboxes by the simple use of an adaptor backplate.
On average, retrofitting a Voith retarder takes about a week. Morris believes that as well as the obvious benefits, retarders can help manufacturers optimise wheel dimensions: "As the OE manufacturers are looking to get down brake and tyre sizes, this gives them a way out of it. . . 1 can think of no good reason why they shouldn't be doing better in the UK."
The Telma electromagnetic retarder is based on the principle of the creation of currents in a conductive steel mass when the mass is placed in a variable magnetic field. The currents created along the flux lines are called eddy or Focault currents. General operating principles of the Telma electromagnetic retarder system.
1 Two discs — the rotors — are attached to the propellor shaft rotating it as a single Piece (I)
2 A stator carrying coils with unlike Poles, is fixed between the two rotors (2)
3 As a result as soon as a current is Passed through the coils it sets uP a magnetic field which traverses the rotor. The magnetic field creates eddy currents, which slow down the speed of rotation of the rotors, without there being any physical contact and therefore any wear between the moving parts (3) So much for the physics lesson: how does it work in practice? The Telma unit has two rotor discs which are fixed to, and rotate with, the propshaft. Between them is the stator, containing the coils, which is fixed to the chassis.
An electric current is fed to coils with alternate polarities, creating a magnetic field which passes through the rotors. This field generates the eddy currents which slow down the rotors and consequently the propshaft.
The inductive currents convert the braking energy of the vehicle in the rotors into heat. Unlike the Voith, the Telma loses this heat via cooling fins built into the rotors. As a result the unit is selfcontained and can be fitted on the back of the gearbox, or to the propshaft.
By being permanently engaged to the drive wheels it prevents engine overspeeding, enabling the driver to downshift without the risk of losing a gear, the retarder effect being maintained throughout the shift process (as with the Voith).
The Telma retarder operates via the vehicle's electrical system and, like the Voith, can be activated by a simple dashboard lever, or linked into the brakes.
ADVANCED MODELS
More advanced models can switch in automatically during deceleration using load sensing. Owing to its extremely fast response times, the Telma can, according to its maker, "easily be coupled to the different anti-skid devices. . . if adhesion is lost, the retarder is cut off immediately. It is then reactivated gradually, governed by the ABS, by means of a Telma electronic interface."
Telma produces two basic ranges: The CC and CE series, which are fitted between the gearbox and drive axle between the universal joints; and the more powerful Focal series with up to 3,300Nm (2,4321bft) of brake torque. Mounted on the back of a gearbox, it is particularly suitable for rear-engined PSVs and tractive units.
Like Voith, Telma offers its retarders on just about every major PSV and HGV chassis.
But as said, retarders don't come cheap. The fully-electronic version of the Voith VHI3K130 starts at a cool 26,500 for a retrofit model. The top Voith unit tips the scales at around 150kg with hoses fitted: the equivalent Focal 3300 retarder weighs in at around 250-300kg and costs 24,500 when retrofitted to a 38-tonner. That figure drops to around 21,700 for a midibus.
Another fly in the pro-retarder ointment is the ever-increasing life of truck friction materials.
Leyland Daf reckons that on average the non-asbestos linings on its 95 Series tractor can last 90,000km for an "average" operation and up to 140,000km for a straightforward regular trunk run. Which is probably just as well, as to reline all the brakes on a 95 will set you back 2435.94 ex-VAT for new linings and 2336 for the cost of "doctoring" them, assuming 17.5 hours, at a typical 219.20 an hour.
If you're only changing linings once a year then it's unlikely that savings on brake servicing costs alone will justify a retarder. But if you're operating in the Peak District or on TIR work through the Alps a retarder becomes more viable.
Putting a price on improved safety is, of course, more difficult. As Robin Gregg, general manager of Telma Retarder in Milton Keynes, says: "How many drivers remember that near miss? Or that smell of hot or burning linings?"
In France operators are given a 500kg weight allowance if they fit a retarder. In other words an operator who has fitted one can legally run his artic at 40,500kg. If Parliament really wants hauliers to adopt an even stronger attitude to safety then maybe this is the way to go. I=1 by Brian Weatherley