New Lockheed Trailer Brake Tested
Page 39
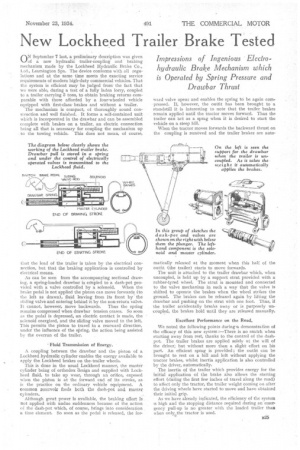
If you've noticed an error in this article please click here to report it so we can fix it.
ONSePtember 7 last, a preliminary description was given of a new hydraulic trailer-coupling and braking mechanism made by the Lockheed Hydraulic Brake Co., Ltd., Leamington Spa. The device conforms with all regulations and at the same time meets the exacting service requirements of modern high-duty commercial vehicles. That the system is efficient may be judged from. the fact that we were able, during a test of a fully laden lorry, coupled to a trailer carrying 3 tons, to obtain braking returns comparable with those afforded by a four-wheeled vehicle equipped with first-class brakes and without a trailer.
The mechanism is compact, of thoroughly sound construction and well finished. It forms a self-contained unit which is incorporated in the drawbar and can be assembled complete with brakes on a trailer, an electric connection being all that is necessary for coupling the mechanism up to the towing vehicle. This does not mean, of course, that the load of the trailer is taken by the electrical connection, but that the braking applicationis controlled by electrical means.
As can be seen from the atcompanying sectional drawing, a spring-loaded drawbar is coupled to a dash-pot provided with a valve controlled by a solenoid. When the brake pedal is not applied the piston can move forwards (to the left as drawn), fluid leaving from its front by the sliding valve and entering behind it by the non-return valve. It cannot, however, move backwards. Thus the spring remains compressed when drawbar tension ceases. So soon as the pedal is depressed, an electric contact is made, the solenoid energized, and the sliding valve moved to the left. This permits the piston. to travel in a rearward direction, under the influence of the spring, the action being assisted by the overrun of the trailer.
' Fluid Transmission of Energy.
A coupling between the drawbar and the piston of a Lockheed hydraulic cylinder enables the energy available to apply the Lockheed brakes on the-trailer wheels.
This is done in the usual Lockheed manner, the master cylinder being of orthodox :design and supplied with Lockheed fluid, to take up wear, through an orifice, exposed when the piston is at the forward end of its stroke, as is the practice on the ordinary vehicle. equipment. A common reservoir feeds beth the dash-pot and master cylinders.
Although great power is available, the braking effort Is not applied with undue suddenness because of the, action of the dash-pot which, of cont-se, brings into consideration a time element. So soon as the pedal is released, the for ward valve opens and enables the spring to be again compressed. If, however, the outfit has been brought to a standstill it is interesting to note that the trailer brakes remain applied until the tractor moves forward. Thus the trailer can act as a sprag when it is desired to start the vehicle on a steep hill.
When the tractor moves forwards the backward thrust on the coupling is removed and the trailer brakes are auto matically released at the moment when this half of the outfit (the trailer) starts to move forwards.
The unit is attached to the trailer drawbar which, when uncoupled, is held up by a support strut provided with a rubber-tyred wheel. The strut is mounted and connected to the valve mechanism in such a way that the valve is shifted to operate the brakes when the wheel strikes the ground. The brakes can be released again by lifting the drawbar and puShing on the strut with one foot. Thus, if, the trailer accidentally breaks away or is purposely uncoupled, the brakes hold until they are released manually,
Excellent Performance on the Road.
We noted the following points durinra demonstration of the efficacy of this new system :—There is no snatch when starting away from rest, thanks to the control of the dashpot. The trailer brakes are applied solely at the will of the driver; hut without more than a slight effort on his part. An efficient sprag is provided ; the outfit can be brought to rest on a hill and left without applying the tractor brakes, whilst inertia application is also controlled by the driver, automatically.
The inertia of the trailer which provides energy for the initial application of the brake also allows the starting effort (during the first few inches of travel along the road) to affect only the tractor, the trailer weight coming on after the driving wheels have started to move and have obtained their initial grip.
As we have already indicated, the efficiency of the system (s high and the stopping distance required during an-emergency pull-up is no greater with the loaded trailer than when only the tractor is used.