CONOMY CLASS
Page 59
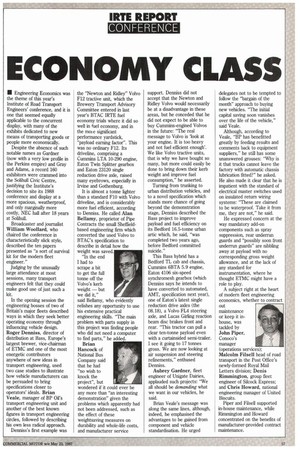
Page 60
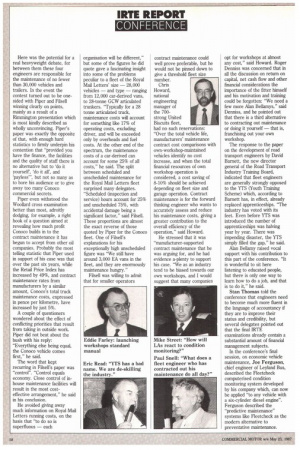
If you've noticed an error in this article please click here to report it so we can fix it.
• Engineering Economics was the theme of this year's Institute of Road Transport Engineers' conference, and it is one that seemed equally applicable to the concurrent display, with many of the exhibits dedicated to new means of transporting goods or people more economically.
Despite the absence of such notable names as Gardner (now with a very low profile in the Perkins empire) and Gray and Adams, a record 160 exhibitors were crammed into the Solihull Civic Centre, justifying the Institute's decision to site its 1988 conference and display at a more spacious, weatherproof, and only marginally more costly. NEC hall after 18 years at Solihull.
Broadcaster and journalist William WooHard, who chaired the conference in characteristically slick style, described the ten papers presented as "a sort of survival kit for the modern fleet engineer."
Judging by the unusually large attendance at most sessions, many transport engineers felt that they could make good use of just such a kit.
In the opening session the engineering bosses of two of Britain's major fleets described ways in which they seek better operating economy through influencing vehicle design. Roger Denniss, director of distribution at Bass, Europe's largest brewer, vice-chairman of ETMC and one of the most energetic contributors anywhere of new ideas in transport engineering, used two case studies to illustrate how vehicle manufacturers can be persuaded to bring specifications closer to operators' ideals. Brian Veale, manager of BP Oil's transport engineering unit and another of the best known figures in transport engineering circles, followed by describing his own less radical approach.
Denniss's first example was the "Newton and Ridley" Volvo F12 tractive unit, which the Brewery Transport Advisory Committee entered in last year's BTAC IRTE fuel economy trials where it did so well in fuel economy, and in the mote significant performance yardstick, "payload earning factor". This was no ordinary F12. Its driveline, comprising a Cununins LTA 10-290 engine, Eaton Twin Splitter gearbox and Eaton 23120 single reduction drive axle, raised many eyebrows, especially in Irvine and Gothenburg.
It is almost a tonne lighter than a standard F10 with Volvo driveline, and is considerably more fuel efficient, according to Denniss. He called Alan Bellamy, proprietor of Pipe Contracts the small Sheffieldbased engineering firm which converted the used Volvo to BTAC's specification to describe in detail how the weight was saved.
"In the end I had to scrape a bit to get the full tonne off the Volvo's kerb weight — but we did it," said Bellamy, who evidently relishes any opportunity to use his extensive practical engineering skills. "The main problem with parts supply in this project was finding people who did not need a computer to find parts," he added.
Brian Hancock of National Bus Company said that he had "no wish to knock the project", but wondered if it could ever be any more than "an interesting demonstration" given the problems which apparently had not been addressed, such as the effect of these weightsaving measures on durability and whole-life costs, and manufacturer service support. Denniss did not accept that the Newton and Ridley Volvo would necessarily be at a disadvantage in these areas, but he conceded that he did not expect to be able to buy Cummins-engined Volvos in the future: "The real message to Volvo is 'look at your engine. It is too heavy and not fuel efficient enough'. We like Volvo tractive units, that is why we have bought so many, but more could easily be done to bring down their kerb weight and improve fuel consumption," he asserted.
Turning from trunking to urban distribution vehicles, and to a novel specification which stands more chance of going beyond the demonstration stage, Denniss described the Bass project to improve payload and fuel efficiency on its Bedford 16.5-tonne urban artic which, he said, "was completed two years ago, before Bedford committed suicide."
This Bass hybrid has a Bedford TL cab and chassis, Cummins 6BTA 5.9 engine, Eaton 4106 six-speed synchromesh gearbox (which Denniss says he intends to have converted to automated, AMT, specification next year), one of Eaton's latest single reduction drive axles (the 08.18), a Volvo FL4 steering axle, and Lucas Girling reaction beam disc brakes front and rear. "This tractor can pull a clear ten-tonne payload even with a curtainsided semi-trailer. I see it going to 17 tonnes gross. We are now looking at air suspension and steering refinements," enthused Denniss.
Aubrey Gardner, fleet engineer of Unigate Dairies, applauded such projects: "We all should be demanding what we want in our vehicles, he said.
Brian Veale's message was along the same lines, although, indeed, he emphasised the advantages to be gained from component and vehicle standardisation. He urged delegates not to be tempted to follow the "bargain of the month" approach to buying new vehicles. "The initial capital saving soon vanishes over the life of the vehicle," said Veale.
Although, according to Veale, "BP has benefitted greatly by feeding results and comments back to equipment suppliers," he still has some unanswered grouses: "Why is it that trucks cannot leave the factory with automatic chassis lubrication fitted?" he asked. He also made it clear that he is impatient with the standard of electrical master switches used on insulated return wiring systems: "These are claimed to be waterproof. Take it from me, they are not," he said.
He expressed concern at the way mandatory add-on components such as spray suppression, rear underrun guards and "possibly soon front underrun guards" are nibbling away at payload with no corresponding gross weight allowance, and at the lack of any standard for instrumentation, where he thought ETMC might have a role to play.
A subject right at the heart of modern fleet engineering economics, whether to contract out maintenance or keep it inhouse, was tackled by John Piper, Conoco's manager (operations services); Malcolm Filsell head of road transport in the Post Office's newly-formed Royal Mail Letters division; Denis Rimmington, group fleet engineer of Silcock Express; and Chris Howard, national engineering manager of United Biscuits.
Piper and Pilsen supported in-house maintenance, while Rinuffington and Howard concentrated on the benefits of manufacturer-provided contract maintenance. Here was the potential for a real heavyweight debate, for between them these four engineers are responsible for the maintenance of no fewer than 30,000 vehicles and trailers. In the event the contest turned out to be onesided with Piper and Filsell winning clearly on points, mainly as a result of a Rimmington presentation which is most kindly described as wholly unconvincing. Piper's paper was exactly the opposite of that, with enough hard statistics to firmly underpin his contention that "provided you have the finance, the facilities and the quality of staff there is no alternative but to 'do it yourself, 'do it all', and 'payless—, but not so many as to bore his audience or to give away too many Conoco commercial secrets.
Piper even withstood the Woollard cross examination better than most, adroitly dodging, for example, a right hook of a question aimed at revealing how much profit Conoco builds in to the contract maintenance it has begun to accept from other oil companies. Probably the most telling statistic that Piper used in support of his case was that over the past six years, while the Retail Price Index has increased by 49%, and contract maintenance rates from manufacturers by a similar amount, Conoco's total truck maintenance costs, expressed in pence per kilometre, have increased by just 5%.
A couple of questioners wondered about the effect of conflicting priorities that result from taking in outside work. Piper did not beat about the bush with his reply: "Everything else being equal, the Conoco vehicle comes first," he said.
The word that kept recurring in Filsell's paper was "control". "Control equals economy. Close control of inhouse maintenance facilities will result in the most costeffective arrangement," he said in his conclusion. organisation will be different," but some of the figures he did quote gave a fascinating insight into some of the problems peculiar to a fleet of the Royal Mail Letters' size — 28,000 vehicles — and type — ranging from 12,000 car-derived vans, to 28-tonne GCW articulated trunkers. "Typically for a 28 tonne articulated truck, maintenance costs will account for something like 17% of operating costs, excluding driver, and will be exceeded only by overheads and fuel costs. At the other end of the spectrum, the maintenance costs of a car-derived can account for some 25% of all costs," he said. The split between scheduled and unscheduled maintenance for the Royal Mail Letters fleet surprised many delegates. "Scheduled (inspection and service) hours account for 25% and unscheduled 75%, with accidental damage being a significant factor," said Easel. These proportions are almost the exact reverse of those quoted by Piper for the Conoco fleet. One of Filsell's explanations for his exceptionally high unscheduled figure was "We still have around 3,000 EA vans in the fleet, and they are enormously maintenance hungry."
Filsell was willing to admit that for smaller operators contract maintenance could well prove preferable, but he would not be pinned down to give a threshold fleet size number.
Chris Howard, national engineering manager of the 700strong United Biscuits fleet, had no such reservations: "Over the total vehicle life, manufacturers' maintenance contract cost comparisons with own-workshop-maintained vehicles identify no cost increase, and when the total financial resources of own workshop operation is considered, a cost saving of 8-10% should be achieved depending on fleet size and garage operation. Contract maintenance is for the forward thinking engineer who wants to accurately assess and reduce his maintenance costs, giving a greater contribution to the overall efficiency of the operation," said Howard.
He stressed that it was "manufacturer-supported contract maintenance that he was arguing for, and he had evidence a-plenty to support his case. "We as an industry tend to be biased towards our own workshops, and I would suggest that many companies opt for workshops at almost any cost," said Howard. Roger Denniss was concerned that in all the discussion on return on capital, net cash flow and other financial considerations the importance of the fitter himself and his motivation and training could be forgotten: "We need a few more Alan Bellarnys," said Denniss, and he pointed out that there is a third alternative to contracting out maintenance or doing it yourself — that is, franchising out your own workshop.
The response to the paper on the development of road transport engineers by David Barnett, the new director general of the Road Transport Industry Training Board, indicated that fleet engineers are generally strongly opposed to the YTS (Youth Training Scheme) which, according to Barnett has, in effect, already replaced apprenticeships "The industry has voted with its feet. Even before YTS was introduced the number of apprenticeships was halving year by year. There was impending disaster, the YTS simply filled the gap," he said.
Alan Bellamy raised vocal support with his contribution to this part of the conference. "It is wonderful to sit here listening to educated people, but there is only one way to learn how to do a job, and that is to do it," he said.
Stan Thomas told the conference that engineers need to become much more fluent in the language of accountancy if they are to improve their status and credibility, but several delegates pointed out that the final IRTE examinations already contain a substantial amount of financial management subjects.
In the conference's final session, on economic vehicle maintenance, Joe Ferguson, chief engineer of Leyland Bus, described the Eleetcheck computerised condition monitoring system developed by his company which, can now be applied "to any vehicle with a six-cylinder diesel engine". Ferguson described the "predictive maintenance" systems like Fleetcheck as the modern alternative to preventative maintenance.