Special handling for refrigerated loads „....dy
Page 53
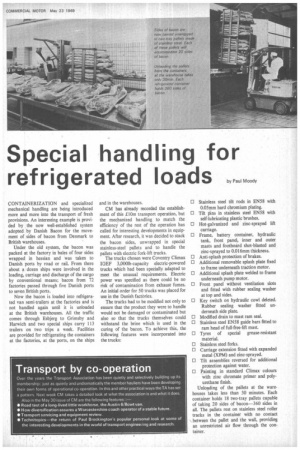
If you've noticed an error in this article please click here to report it so we can fix it.
CONTAINERIZATION and specialized mechanical handling are being introduced more and more into the transport of fresh provisions. An interesting example is provided by the now well-established system adopted by Danish Bacon for the movement of sides of bacon from Denmark to British warehouses.
Under the old system, the bacon was packed at the factory in bales of four sides wrapped in hessian and was taken to Danish ports by road or rail. From there about a dozen ships were involved in the loading, carriage and discharge of the cargo by conventional means; bacon from 72 factories passed through five Danish ports to seven British ports.
Now the bacon is loaded into refrigerated van semi-trailers at the factories and is not handled again until it is unloaded at the British warehouses. All the traffic comes through Esbjerg to Grimsby and Harwich and two special ships carry 113 trailers on two trips a week. Facilities are provided for refrigerating the containers at the factories, at the ports, on the ships and in the warehouses.
CM has already recorded the establishment of this £10m transport operation, but the mechanized handling to match the efficiency of the rest of the operation has called for interesting developments in equipment. After research, it was decided to stack the bacon sides, unwrapped in special stainless-steel pallets and to handle the pallets with electric fork-lift trucks.
The trucks chosen were Coventry Climax IGEF 3,000lb-capacity electric-powered trucks which had been specially adapted to meet the unusual requirements. Electric power was specified as there could be no risk of contamination from exhaust fumes. An initial order for 50 trucks was placed for use in the Danish factories.
The trucks had to be modified not only to ensure that the product they were to handle would not be damaged or contaminated but also so that the trucks themselves could withstand the brine which is used in the curing of the bacon. To achieve this, the following features were incorporated into the trucks: O Stainless steel tilt rods in EN58 with 0.05mm hard chromium plating.
El Tilt pins in stainless steel EN58 with self-lubricating plastic brushes.
O Hot-galvanized and zinc-sprayed lift carriage. o Frame, battery container, hydraulic tank, front panel, inner and outer masts and footboard shot-blasted and zinc-sprayed to 0.016mm thickness. o Anti-splash protection of brakes.
O Additional removable splash plate fixed to frame underneath traction motor.
O Additional splash plate welded to frame underneath pump motor.
O Front panel without ventilation slots and fitted with rubber sealing washer at top and sides.
O Key switch on hydraulic cowl deleted. Rubber sealing washer fitted underneath side plate.
O Modified drain to mast ram seal.
O Stainless steel ENS 8 guide bars fitted to ram head of full-free-lift mast.
O Tyres of special grease-resistant material.
O Stainless steel forks.
O Carriage extension fitted with expanded metal (XPM) and zinc-sprayed.
O Tilt assemblies reversed for additional protection against water.
El Painting in standard Climax colours with zinc chromate primer and polyurethane finish.
Unloading of the pallets at the warehouses takes less than 30 minutes. Each container holds 18 two-tray pallets capable of taking 20 sides of bacon-360 sides in all. The pallets rest on stainless steel roller tracks in the container with no contact between the pallet and the wall, providing an unrestricted air flow through the container.