Passing Comments
Page 24
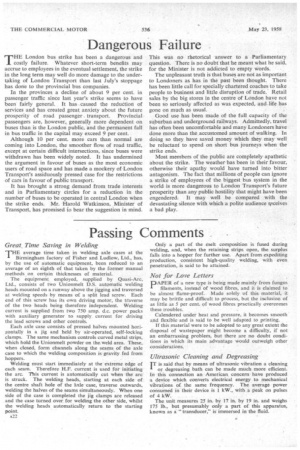
Page 25
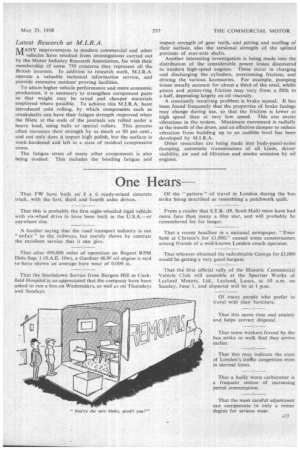
If you've noticed an error in this article please click here to report it so we can fix it.
Great. Time Saving in Welding
THE average time taken in welding axle cases at the I Birmingham factory of Fisher and Ludlow, Ltd., has, by the use of automatic equipment, been reduced to an average of an eighth of that taken by the former manual methods on certain thicknesses of material.
The equipment employed, supplied by Quasi-Arc, Ltd., consists of two Unionmelt D.S. automatic welding heads mounted on a runway above the jigging and traversed at welding speeds by means of a split lead screw. Each end of this screw has its own driving motor, the traverse of the two heads being therefore independent. Welding current is supplied from two 750 amp, d.c. power packs with auxiliary generator to supply current for driving the lead screws and other controls.
Each axle case consists of pressed halves mounted horizontally in a jig and held by air-operated, self-locking clamps. The same mechanism controls curved metal strips, which hold the UnionmeIt powder on the weld arca. These, when closed, form channels along the seams of the axle case to which the welding composition is gravity fed from hoppers.
Welding must start immediately at the extreme edge of each seam. Therefore H.F. current is used for initiating the arc. This current is automatically cut when the arc is struck. The welding heads, starting at each side of the centre shaft hole of the axle case, traverse outwards, welding the halves of the seams simultaneously. When one side of the case is completed the jig clamps are released and the case turned over, for welding the other side, whilst the welding heads automatically return to the starting point.
A22
Only a part of the melt composition is fused during welding, and, when the retaining strips open, the surplus falls into a hopper for further use. Apart from expediting production, consistent high-quality welding, with even penetration, is said to be attained.
Not for Love Letters
PAPER of a new type is being made mainly from fungus filaments, instead of wood fibres, and it is claimed to be almost flame-proof. Made solely of this material, it may be brittle and difficult to process, but the inclusion of as little as 5 per cent. of wood fibres practically overcomes these troubles.
Calendered under heat and pressure, it becomes smooth and flexible and is said to be well adapted to printing.
If this material were to be adopted to any great extent the disposal of wastepaper might become a difficulty, if not an embarrassing problem, but there are no doubt conditions in which its main advantage Would outweigh other considerations.
Ultrasonic Cleaning and Degreasing
TT is said that by means of ultrasonic vibration a cleaning I or degreasing bath can be made much more efficient. In this connection an American concern have produced a device which converts electrical energy to mechanical vibrations of the same frequency. The average power consumed in their device is 1 kW., with a peak on pulses of 4 kW.
The unit measures 25 in. by 17 in. by 19 in. and weighs 175 lb., but presumably only a part of this apparatus, known as a "transducer," is immersed in the fluid.
Latest Research at
MANY improvements in modern commercial and other
vehicles have resulted from investigations carried out by the Motor Industry Research Association, for with their membership of some 750 concerns they represent all the British interests. In addition to research work, M.I.R.A. operate a valuable technical information service, and provide extensive outdoor proving facilities.
To attain higher vehicle performance and more economic production, it is necessary to strengthen component parts so that weight may be saved and cheaper materials employed where possible. To achieve this M.I.R.A. have introduced cold rolling, by which components such as crankshafts can have their fatigue strength improved when the fillets at the ends of the journals are rolled under a heavy load, using balls or special rollers. This process often increases their strength by as much as 80 per cent, and not only does it impart high polish, but the surface is work-hardened and left in a state of residual compressive stress.
The fatigue stress of many other components is also being studied. This includes the bending fatigue and impact strength of gear teeth, and pitting and scuffing of their surface, also the torsional strength of the splined portions of rear-axle shafts.
Another interesting investigation is being made into the distribution of the considerable power losses discovered in modern high-speed engines. These occur in charging and discharging the cylinders, overcoming friction, and driving the various accessories. For example, pumping losses usually account for about a third of the total, whilst piston and piston-ring friction may vary from a fifth to a half, depending largely on oil viscosity.
A constantly recurring problem is brake squeal. It has been found frequently that the properties of brake facings may' change during use, so that the friction is lower at high speed, than at very low speed. This can 'excite vibrations in the system. Maximum movement is radially at the mouth of the drum, and an effective damper to reduce vibration from building up to an audible level has been developed by M.I.R.A.
Other researches are being made into body-panel-noise damping; automatic transmissions of all kinds, driver visibility, air and oil filtration and smoke emission by oil engines.