Econolite slides in
Page 18
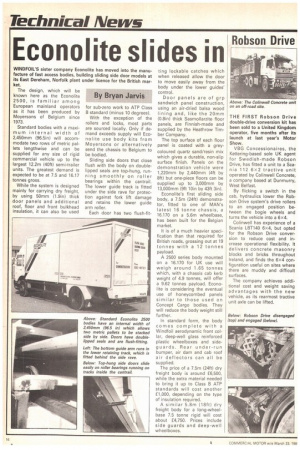
If you've noticed an error in this article please click here to report it so we can fix it.
WINDFOIL'S sister company Econolite has moved into the manufacture of fast access bodies, building sliding side door models at its East Dereham, Norfolk plant under licence for the British market.
By Bryan Jarvis
The design, which will be known here as the Econolite 2500, is familiar among European mainland operators as it has been produced by Moyersons of Belgium since 1973.
Standard bodies with a maximum internal width of 2,450mm (96.5in) will accommodate two rows of metric pallets lengthwise and can be supplied for any size of rigid commercial vehicle up to the largest 12.2m (40ft) semi-trailer units. The greatest demand is expected to be at 7.5 and 16.17 tonnes gross.
While the system is designed mainly for carrying dry freight, by using 50mm (1.9in) thick door panels and additional roof, floor and front bulkhead insulation, it can also be used for sub-zero work to ATP Class B standard (minus 10 degrees).
With the exception of the rollers and locks, most parts are sourced locally. Only if demand exceeds supply will Econolite use body kits from Moyersons or alternatively send the chassis to Belgium to be bodied.
Sliding side doors that close flush with the body on doublelipped seals are top-hung, running smoothly on roller bearings within the cantrail. The lower guide track is fitted under the side rave for protection against fork lift damage and retains the lower guide arm roller. ting lockable catches which when released allow the door to move easily away from the body under the lower guides' control.
Door panels are of grp sandwich panel construction, using an air-dried balsa wood lining and, like the 20mm (0.8in) thick Sasmollarzite floor panels, are Finnish-made and supplied by the Heathrow Timber Company.
The top surface of each floor panel is coated with a grey coloured quartz sand/resin mix which gives a durable, non-slip surface finish. Panels on the demonstration vehicle were 1,220mm by 2,440mm (4ft by 8ft) but one-piece floors can be supplied up to 3,000mm by 13,000mm (9ft 10in by 43ft 3in).
Econolite's first sliding side body, a 7.5m (24ft) demonstrator, fitted to one of MAN's latest 16 tonne chassis, a 16.170 on a 5.6m wheelbase, has been built for the Belgian market.
It is of a much heavier specification than that required for British roads, grossing out at 19 tonnes with a 12 tonnes payload.
A 2500 series body mounted on a 16.170 for UK use will weigh around 1.65 tonnes which, with a chassis cab kerb weight of 4.9 tonnes, will offer a 9.62 tonnes payload. Econolite is considering the eventual use of honeycombed panels similar to those used on Concept Cargo bodies. They will reduce the body weight still further.
In standard form, the body comes complete with a Windfoil aerodynamic front collar, deep-well glass reinforced plastic wheelboxes and sideguards. Rear under-run bumper, air dam and cab roof air deflectors can all be supplied.
The price of a 7.5m (24ft) dry freight body is around £6,500, while the extra material needed to bring it up to Class B ATP standards will cost another £1,000, depending on the type of insulation required.
A similar 5.8m (18ft) dry freight body for a long-wheelbase 7.5 tonne rigid will cost about £4,750. Prices include side guards and deep-well wheelboxes. THE FIRST Robson Drive double-drive conversion kit has been sold to a United Kingdom operator, five months after its launch at last year's Motor Show.
VBG Concessionaires, the Kettering-based sole UK agent for Swedish-made Robson Drive, has fitted a unit to a Scania 112 6x2 tractive unit operated by Colinwell Concrete, a company based at Dunmurry, West Belfast.
By flicking a switch in the cab, hydraulics lower the Robson Drive system's drive rollers to an engaged position between the bogie wheels and turns the vehicle into a 6x4.
Colinwell has experience of a Scania LBT140 6x4, but opted for the Robson Drive conversion to reduce cost and increase operational flexibility. It delivers concrete masonry blocks and bricks throughout Ireland, and finds the 6x4 configuration useful on sites where there are muddy and difficult surfaces.
The company achieves additional cost and weight saving advantages with the new vehicle, as its rearmost tractive unit axle can be lifted.