FROM OILY RAG TO HIGH TECH
Page 48
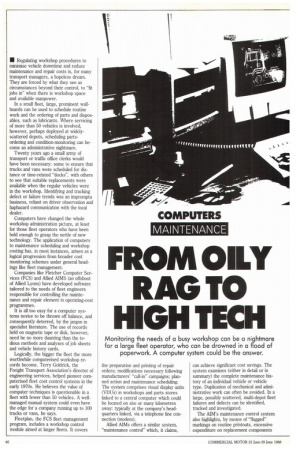
Page 49
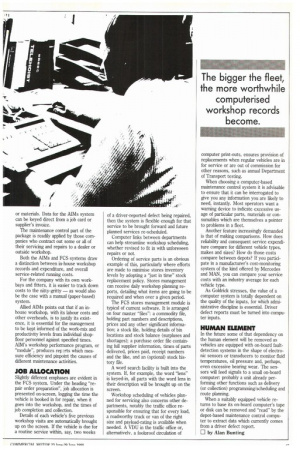
If you've noticed an error in this article please click here to report it so we can fix it.
Monitoring the needs of a busy workshop can be a nightmare for a large fleet operator, who can be drowned in a flood of paperwork. A computer system could be the answer.
• Regulating workshop procedures to minimise vehicle downtime and reduce maintenance and repair costs is, for many transport managers, a hopeless dream. They are forced by what they see as circumstances beyond their control, to "fit jobs in" when there is workshop space and available manpower.
In a small fleet, large, prominent wallboards can be used to schedule routine work and the ordering of parts and disposables, such as lubricants. Where servicing of more than 50 vehicles is involved, however, perhaps deployed at widelyscattered depots, scheduling partsordering and condition-monitoring can become an administrative nightmare.
Twenty years ago a small army of transport or traffic office clerks would have been necessary: some to ensure that trucks and vans were scheduled for distance or time-related "docks", with others to see that suitable replacements were available when the regular vehicles were in the workshop. Identifying and tracking defect or failure trends was an impromptu business, reliant on driver observation and haphazard communication with the local dealer.
Computers have changed the whole workshop administration picture, at least for those fleet operators who have been bold enough to grasp the nettle of new technology. The application of computers to maintenance scheduling and workshop costing has, in most instances, arisen as a logical progression from broader cost monitoring schemes under general headings like fleet management.
Companies like Fletcher Computer Services (FCS) and Allied AIMS (an offshoot of Allied Lyons) have developed software tailored to the needs of fleet engineers responsible for controlling the maintenance and repair element in operating-cost programmes.
It is all too easy for a computer systems novice to be thrown off balance, and consequently deterred, by the jargon in specialist literature. The use of records held on magnetic tape or disk, however, need be no more daunting than the tedious methods and analyses of job sheets and vehicle history cards_ Logically, the bigger the fleet the more worthwhile computerised workshop records become. Terry Goldrick, the Freight Transport Association's director of engineering services, helped pioneer computerised fleet cost control systems in the early 1970s. He believes the value of computer techniques is questionable in a fleet with fewer than 50 vehicles. A wellmanaged manual system could even have the edge for a company running up to 100 trucks or vans, he says.
Fleetplan, the FCS fleet management program, includes a workshop control module aimed at larger fleets. It covers the preparation and printing of repair orders; modifications necessary following manufacturers' "call-in" campaigns; planned action and maintenance scheduling. The system comprises visual display units (VDUs) in workshops and parts stores linked to a central computer which could be located on site or many kilometres away: typically at the company's headquarters linked, via a telephone line connection (modem).
Allied AMU offers a similar system, "maintenance control" which, it claims, can achieve significant cost savings. The system examines (either in detail or in summary) the complete maintenance history of an individual vehicle or vehicle type. Duplication of mechanical and administrative work can often be avoided. In a large, possibly scattered, multi-depot fleet failures and defects can be identified, tracked and investigated.
The AIM's maintenance control system also highlights, by means of "flagged" markings on routine printouts, excessive expenditure on replacement components or materials. Data for the AIMs system can be keyed direct from a job card or supplier's invoice.
The maintenance control part of the package is readily applied by those companies who contract out some or all of their servicing and repairs to a dealer or outside workshop.
Both the AIMs and FCS systems draw a distinction between in-house workshop records and expenditure, and overall service-related running costs.
For the company with its own workbays and fitters, it is easier to track down costs to the nitty-gritty — as would also be the case with a manual (paper-based) system.
Allied AIMs points out that if an inhouse workshop, with its labour costs and other overheads, is to justify its existence, it is essential for the management to be kept informed of the work-mix and productivity levels from individual shopfloor personnel against specified times. AIM's workshop performance program, or "module", produces rep3rts which measure efficiency and pinpoint the causes of different maintenance activities.
JOB ALLOCATION
Slightly different emphases are evident in the FCS system. Under the heading "repair order preparation", job allocation is presented on-screen, logging the time the vehicle is booked in for repair, when it goes into the workshop, and the times of job completion and collection.
Details of each vehicle's five previous workshop visits are automatically brought up on the screen. If the vehicle is due for a routine service within, say, two weeks of a driver-reported defect being repaired, then the system is flexible enough for that service to be brought forward and future planned services re-scheduled.
Computer links between departments can help streamline workshop scheduling, whether revised to fit in with unforeseen repairs or not.
Ordering of service parts is an obvious example of this, particularly where efforts are made to minimise stores inventory levels by adopting a "just in time" stock replacement policy. Stores management can receive daily workshop planning reports, detailing what items are going to be required and when over a given period.
The FCS stores management module is typical of current software. It is arranged on four master "files": a commodity file, holding part numbers and descriptions, prices and any other significant information; a stock file, holding details of bin locations and stock balance (surpluses and shortages); a purchase order file containing full supplier information, times of parts delivered, prices paid, receipt numbers and the like, and an (optional) stock history file.
A word search facility is built into the system. If, for example, the word "lens" is keyed-in, all parts with the word lens in their description will be brought up on the screen.
Workshop scheduling of vehicles planned for servicing also concerns other departments, notably the traffic office responsible for ensuring that for every load, a roadworthy truck or van of the right size and payload-rating is available when needed. A VDU in the traffic office or, alternatively, a foolproof circulation of computer print-outs, ensures provision of replacements when regular vehicles are in for service or are out of commission for other reasons, such as annual Department of Transport testing.
When choosing a computer-based maintenance control system it is advisable to ensure that it can be interrogated to give you any information you are likely to need, instantly. Most operators want a warning device to indicate excessive usage of particular parts, materials or consumables which are themselves a pointer to problems in a fleet.
Another feature increasingly demanded is that of making comparisons. How does reliability and consequent service expenditure compare for different vehicle types, makes and sizes? How do those costs compare between depots? If you participate in a manufacturer's cost-monitoring system of the kind offered by Mercedes and MAN, you can compare your service costs with an industry average for each vehicle type.
As Goldrick stresses, the value of a computer system is totally dependent on the quality of the inputs, for which administrative discipline is essential. Driver defect reports must be turned into computer inputs.
HUMAN ELEMENT
In the future some of that dependency on the human element will be removed as vehicles are equipped with on-board faultdetection systems in the shape of electronic sensors or transducers to monitor fluid temperatures, oil pressure and, perhaps, even excessive bearing wear. The sensors will feed signals to a small on-board computer: probably a unit already performing other functions such as delivery (or collection) programming/scheduling and route planning.
When a suitably equipped vehicle returns to base its on-board computer's tape or disk can be removed and "read" by the depot-based maintenance control computer to extract data which currently comes from a driver defect report.
by Alan Bunting