WORKSHOP WELDING
Page 124
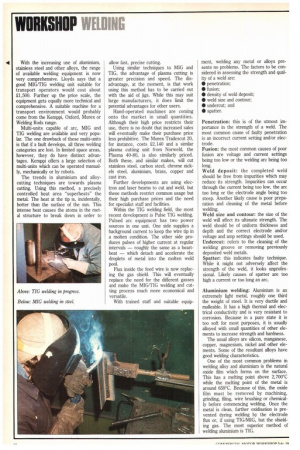
Page 125
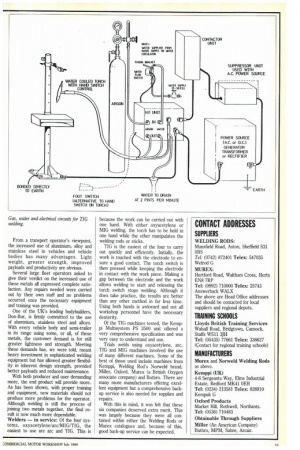
If you've noticed an error in this article please click here to report it so we can fix it.
With the increasing use of aluminium, stainless steel and other alloys, the range of available welding equipment is now very comprehensive. Lloyds says that a good MIG/TIG welding unit suitable for transport operators would cost about 1,500. Further up the price scale, the equipment gets equally more technical and comprehensive. A suitable machine for a transport environment would probably come from the Kemppi, Oxford, Murex or Welding Rods range.
Multi-units capable of arc, MIG and TIG welding are available and very popular. The one drawback of these multi-units is that if a fault develops, all three welding categories are lost. In limited space areas, however, they do have distinct advantages. Kemppi offers a large selection of multi-units which can be operated manually, mechanically or by robots.
The trends in aluminium and alloycutting techniques are towards plasma cutting. Using this method, a precisely controlled heat area "superheats" the metal. The heat at the tip is, incidentally, hotter than the surface of the sun. This intense heat causes the atoms in the metal structure to break down in order to allow fast, precise cutting.
Using similar techniques to MIG and TIG, the advantage of plasma cutting is greater precision and speed. The disadvantage, at the moment, is that work using this method has to be carried out with the aid of jigs. While this may suit large manufacturers, it does limit the potential advantages for other users.
Hand-operated machines are coming onto the market in small quantities. Although their high price restricts their use, there is no doubt that increased sales will eventually make their purchase price less prohibitive. The Murex Tradescut 20, for instance, costs £2,140 and a similar plasma cutting unit from Norweld, the Plasma 40-80, is also similarly priced. Both these, and similar makes, will cut stainless steel, carbon steel, chrome nickels steel, aluminium, brass, copper and cast iron.
Further developments are using electron and laser beams to cut and weld, but these methods restrict common usage but their high purchase prices and the need for specialist staff and facilities.
Within the TIG welding field, the most recent development is Pulse TIG welding. Pulsed arc equipment has two power sources in one unit. One side supplies a background current to keep the wire tip in a molten condition. The other side produces pulses of higher current at regular intervals — roughly the same as a heartbeat — which detach and accelerate the droplets of metal into the molten weld pool.
Flux inside the feed wire is now replacing the gas shield. This will eventually replace the need for the different gasses and make the miGrriG welding and cutting process much more economical and versatile.
With trained staff and suitable equip ment, welding any metal or alloys presents no problems. The factors to be considered in assessing the strength and quality of a weld are: • penetration; • fusion; • density of weld deposit; • weld size and contour; • undercut; and • spatter.
Penetration: this is of the utmost importance in the strength of a weld. The most common cause of faulty penetration is an incorrect current setting and/or electrode.
Fusion: the most common causes of poor fusion are voltage and current settings being too low or the welding arc being too long.
Weld deposit: the completed weld should be free from impurities which may reduce its strength. Impurities can occur through the current being too low, the arc too long or the electrode angle being too steep. Another likely cause is poor preparation and cleaning of the metal before welding.
Weld size and contour: the size of the weld will affect its ultimate strength. The weld should be of uniform thickness and depth and the correct electrode and/or voltage and amp settings should be used. Undercut: refers to the cleaning of the welding groove or removing previously deposited weld metals.
Spatter. this indicates faulty technique. While it might not adversely affect the strength of the weld, it looks unprofessional. Likely causes of spatter are too high a current or too long an arc.
Aluminium welding: Aluminium is an extremely light metal, roughly one third the weight of steel. It is very ductile and malleable. It has a high thermal and electrical conductivity and is very resistant to corrosion. Because in a pure state it is too soft for most purposes, it is usually alloyed with small quantities of other elements to increase strength and hardness.
The usual alloys are silicon, manganese, copper, magnesium, nickel and other elements. Some of the resultant alloys have good welding characteristics.
One of the most common problems in welding alloy and aluminium is the natural oxide film which forms on the surface. This has a melting point above 2,700°C while the melting point of the metal is around 659°C. Because of this, the oxide film must be removed by machining, grinding, filing, wire brushing or chemically before commencing welding. Once the metal is clean, further oxidisation is prevented dyring welding by the electrode flux or, if using TIG/MIG, but the shielding gas. The most superior method of welding aluminium is TIG. Gas, water and electrical circuits for TIG welding.
From a transport operator's viewpoint, the increased use of aluminium, alloy and stainless steel in vehicles and vehicle bodies has many advantages. Light weight, greater strength, improved payloads and productivity are obvious.
Several large fleet operators asked to give their verdict on the increased use of these metals all expressed complete satisfaction. Any repairs needed were carried out by their own staff and no problems occurred once the necessary equipment and training was provided.
One of the UK's leading bodybuilders, Don-Bur, is firmly committed to the use of aluminium, stainless steel and alloys. With every vehicle body and semi-trailer in its range using some, or all, of these metals, the customer demand is for still greater lightness and strength. Meeting these demands has, we were told, meant heavy investment in sophisticated welding equipment but has allowed greater flexibility in inherent design strength, provided better payloads and reduced maintenance.
With both producer and user demanding more, the end product will provide more. As has been shown, with proper training and equipment, new materials should not produce more problems for the operator. Although welding is still the process of joining two metals together, the final result is now much more dependable.
Welders — in service: Of the four systems, oxyacetylene/arc/MIG/TIG, the easiest to use are arc and TIG. This is because the work can be carried out with one hand. With either oxyacetylene or MIG welding, the torch has to be held in one hand while the other manipulates the welding rods or sticks.
TIG is the easiest of the four to carry out quickly and efficiently. Initially, the work is touched with the electrode to ensure a good contact. The torch switch is then pressed while keeping the electrode in contact with the work piece. Making a gap between the electrode and the work allows welding to start and releasing the torch switch stops welding. Although it does take practice, the results are better than any other method in far less time. Using both hands is awkward and not all workshop personnel have the necessary dexterity.
Of the TIG machines tested, the Kemppi Multisystem PS 3500 unit offered a very comprehensive specification and was very easy to understand and use.
Trials welds using oxyacetylene, arc, TIG and MIG machines involved the use of many different machines. Some of the best of those used include machines from Kemppi, Welding Rod's Norweld brand, Miller, Oxford, Murex (a British Oxygen associate company) and Butbro. There are many more manufacturers offering excellent equipment but a comprehensive backup service is also needed for supplies and repairs.
With this in mind, it was felt that these six companies deserved extra merit. This was largely because they were all contained within either the Welding Rods or Murex catalogues and, because of this, good back-up service can be expected.