Heat's on for better welds
Page 122

Page 123
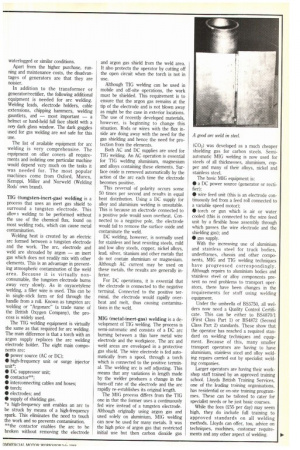
If you've noticed an error in this article please click here to report it so we can fix it.
As new metals and alloys have been developed, so have improved welding techniques. We look at what's available
• Welding is described as "to join by heating and hammering". While this dictionary definition is correct, it is also out of date. The days of metals being heated in a forge and joined by hammering on an anvil are long gone. Today, welding is achieved by the use of complex machines and accessories in highly skilled hands. As new metals and alloys have been developed, so have improved welding techniques.
Starting with the most basic method, there are four types of welding equipment in general use. These are: oxyacetylene; arc; MIG/MAG (metal-inert-gas/ metal-active-gas); and TIG (tungsteninert-gas).
Oxyacetylene welding is still very popular but restricted in application. It is a fusion process in which the weld is made by melting the edges of the parent metal with an intense heat. This heat, which is approximately 3200°C, is produced by the combustion of acetylene gas with oxygen. Used in conjunction with metal filler rods, the prime advantage of this method of welding is that it can be carried out virtually anywhere. The equipment needed consists of: • cylinders of oxygen and acetylene; • pressure regulators for the above; • welding blowpipe with various nozzles; • rubber/canvas hoses with appropriate spanners, spindle key for gas cylinders and goggles; and • welding rods. For certain applications, oxyacetylene welding has definite advantages. Because of its controllable heat output, it is ideal for welding thin materials, cast iron, die castings and for brazing aluminium. For increased portability, there are "mini" oxyacetylene outfits on the market.
The Saffu-e FN Welding and Cutting outfit consists of small gas bottles in a lightweight carrier and a case containing a selection of nozzles. Called the Portapak, it is just that: a comprehensive, miniature outfit for difficult locations and on-the-spot maintenance. Butbro markets a similar outfit called the Caddypak.
For more precise workshop cutting operations, there are semi-automatic cutting machines. Once set up, these can cut plates up to 150mm thick without constant attendance. Others can be used off-site and are powered by car batteries if no alternative power source is available. The IMP flame-cutting machine from Saffire offers both on and off-site versatility.
Electric arc welding is used in many branches of industry. It is by far the most widely used welding process. The process of electric arc welding is achieved by transmitting a suitable supply of electrical energy to where a weld is required. This electrical energy is then converted into heat energy.
In simple terms, the item on which welding is to be carried out is earthed. An electrode, attached to a live electrical supply, is then used to strike an arc with the earthed item and the resulting arc of electricity melts the electrode to form a strong weld.
Because the mains electricity supply does not have the characteristics needed for arc welding, extra equipment is required. The purpose of this equipment is to reduce the mains voltage to a suitable level or provide an independent alternative. Arc welding needs an open circuit voltage of 60-100 volts and an arc voltage of 20-40 volts. This is achieved by a transformer which reduces the current for AC (alternating current) welding. Alterna tively, a generator or rectifier can be used for DC (direct current) welding.
As transformers do not generate electricity, they can only be used with an AC mains supply. The function of a step-down transformer is to convert the high voltage/ low amperage mains supply to a low voltage/high amperage supply. Most transformers have a voltage range between 70100 volts and an amperes capacity of 150900 amps.
DC welding generators are generally of the single-operator type and have an open circuit voltage of 40-60 volts. Different current capacities are available to suit the work for which they are required. The most popular generators have ampere capacities of 150, 300, 600 and 900amps. These portable generators can be either petrol or diesel powered.
There are many portable types available offering outputs to suit operators' needs. Welding Rods, one of the leading suppliers for welding and cutting equipment, offers several in its current catalogue. The smallest, the MPM 5/170 CXD uses only 1.1 litres of diesel per hour on full load. Weighing only 110kg, it is powerful enough at 170amps DC welding current for most off-site repairs.
At the other end of the scale, the diesel-powered MPM 20/600 generator offers a massive 600 amps, comes mounted on towing gear and can tackle virtually any job.
A rectifier is a separate unit connected to the AC transformer. Its function is to convert the alternating current to a direct current. Rectifiers are being used increasingly as power sources for semiautomatic gas shielded (MIG) welding and in transformer/rectifier AC/DC units for metal-arc and tungsten-arc (TIG) welding operations. Again, a large selection is available. The Welding Rods catalogue offers seven models and the Murex catalogue lists six. The Welding Rods NL301 or the NL401 are designed for severe conditions in both production and repairs.
The advantage of the transformer is that it is cheaper to purchase and to use than a generator. It is quiet in operation, free from moving parts and will function for a long time with minimum maintenance. The disadvantages are that a transformer cannot be used without a mains supply and it requires a higher operating voltage than a DC generator/rectifier.
The risk of electric shock is greater with an AC unit and some types of lightly covered and non-ferrous electrodes will not perform satisfactorily with alternating current.
Generators are more popular than transformers because of their mobility. On sites where mains supply power is not available, an engine driven generator is essential. A DC supply is safer than an AC supply and can be used in confined, waterlogged or similar conditions.
Apart from the higher purchase, running and maintenance costs, the disadvantages of generators are that they are noisier.
In addition to the transformer or generator/rectifier, the following additional equipment is needed for arc welding. Welding leads, electrode holders, cable extensions, chipping hammers, welding gauntlets, and — most important — a helmet or hand-held full face shield with a very dark glass window. The dark goggles used for gas welding are not safe for this use.
The list of available equipment for arc welding is very comprehensive. The equipment on offer covers all requirements and isolating one particular machine would depend very much on the tasks it was needed for. The most popular machines come from Oxford, Murex, Kemppi, Miller and Norweld (Welding Rods' own brand).
TIG (tungsten-inert-gas) welding is a process that uses an inert gas shield to surround a tungsten electrode. This
s welding to be performed without the use of the chemical flux, found on most welding rods, which can cause metal contamination.
Welding heat is created by an electric arc formed between a tungsten electrode and the work. The arc, electrode and weld are shrouded by argon — an inert gas which does not readily mix with other elements. This is an advantage in preventing atmospheric contamination of the weld area. Because it is virtually nonconsumable, the tungsten electrode burns away very slowly. As in oxyacetylene welding, a filler wire is used. This can be in single-stick form or fed through the handle from a roll. Known as tungsten arc welding or "Argonarc" (a trade name of the British Oxygen Company), the process is widely used.
The TIG welding equipment is virtually the same as that required for arc welding. The main difference is that a torch with an argon supply replaces the arc welding electrode holder. The eight main components are: • power source (AC or DC);
• high-frequency unit or surge injector unit*;
• DC suppressor unit;
• contactor**;
• interconnecting cables and hoses; • torch; • electrodes; and • supply of shielding gas.
*a high-frequency unit enables an arc to be struck by means of a high-frequency spark. This eliminates the need to touch the work and so prevents contamination. **the contactor enables the arc to be broken without removing the electrode
and argon gas shield from the weld area. It also protects the operator by cutting off the open circuit when the torch is not in use.
Although TIG welding can be used in mobile and off-site operations, the work must be shielded. This requirement is to ensure that the argon gas remains at the tip of the electrode and is not blown away as might be the case in exterior locations. The use of recently developed materials, however, is beginning to change this situation. Rods or wires with the flux inside are doing away with the need for the gas shielding and hence the need for protection from the elements.
Both AC and DC supplies are used for TIG welding. An AC operation is essential for TIG welding aluminium, magnesium and alloys containing these elements. Surface oxide is removed automatically by the action of the arc each time the electrode becomes positive.
This reversal of polarity occurs some 50 times per second and results in equal heat distribution. Using a DC supply for alloy and aluminium welding is unsuitable_ This is because an electrode connected to a positive pole would soon overheat. Connected to a negative pole, the electrode would fail to remove the surface oxide and contaminate the weld.
DC welding, however, is normally used for stainless and heat resisting steels, mild and low alloy steels, copper, nickel alloys, lead, silver, titanium and other metals that do not contain aluminium or magnesium. Although AC current may be used on these metals, the results are generally inferior.
For DC operations, it is essential that the electrode is connected to the negative terminal. Connected to the positive terminal, the electrode would rapidly overheat and melt, thus causing contaminations in the weld.
MIG (metal-inert-gas) welding is a development of TIG welding, The process is semi-automatic and consists of a DC arc burning between a thin bare metal wire electrode and the workpiece. The arc and weld areas are enveloped in a protective gas shield. The wire electrode is fed automatically from a spool, through a torch which is connected to the positive terminal. The welding arc is self adjusting. This means that any variations in length made by the welder produces a change in the burn-off rate of the electrode and the arc rapidly re-establishes its original length.
The MIG process differs from the TIG one in that the former uses a continuously fed wire instead of a tungsten electrode. Although originally using argon gas and used solely on aluminium, MIG welding can now be used for many metals. It was the high price of argon gas that restricted initial use but then carbon dioxide gas (CO2) was developed as a much cheaper shielding gas for carbon steels. Semiautomatic MIG welding is now used for steels of all thicknesses, aluminium, copper and many of their alloys, nickel and stainless steel.
The basic MIG equipment is: • a DC power source (generator or rectifier); • wire feed unit (this is an electrode continuously fed from a feed roll connected to a variable speed motor); • torch or gun which is air or water cooled (this is connected to the wire feed unit by a flexible hose assembly through which passes the wire electrode and the shielding gas); and • gas supply.
With the increasing use of aluminium and stainless steel for truck bodies, underframes, chassis and other components. MIG and TIG welding techniques have progressed correspondingly. Although repairs to aluminium bodies and stainless steel or alloy components present no real problems to transport operators, there have been changes in the requirements for staff using welding equipment.
Under the umbrella of BS5750, all welders now need a Quality Control Certificate. This can be either to BS4870/1 (First Class Part 1) or BS482 (Second Class Part 2) standards. These show that the operator has reached a required standard on welding techniques and equipment. Because of this, many smaller transport operators are having to have aluminium, stainless steel and alloy welding repairs carried out by specialist welding companies.
Larger operators are having their workshop staff trained by an approved training school. Lloyds British Training Services, one of the leading training organisations, has residential or on-site training programmes. These can he tailored to cater for specialist needs or he just basic courses.
While the fees (E55 per day) may seem high, they do include full training to approved standards on all welding methods. Lloyds can offer, too, advice on techniques, machines, customer requirements and any other aspect of welding.