Plastic balls stop tanker surges
Page 45
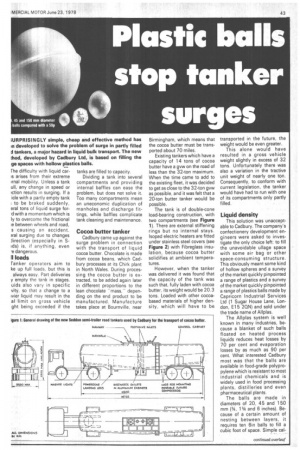
Page 46
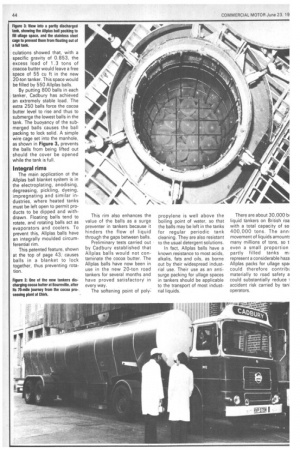
If you've noticed an error in this article please click here to report it so we can fix it.
;URPRISINGLY simple, cheap and effective method has In developed to solve the problem of surge in partly filled cl tankers, a major hazard in liquid bulk transport. The new thod, developed by Cadbury Ltd, is based on filling the ge spaces with hollow plastics balls.
the difficulty with liquid caris arises from their extreme rnal mobility. Unless a tank ull, any change in speed or )ction results in surging. If a icle with a partly empty tank ; to be braked suddenly, eral tons of liquid surge fort! with a momentum which is ly to overcome the frictional :e between wheels and road, s causing an accident. ral surging due to changes Jirection (especially in Sids) is, if anything, even 'e dangerous.
II loads
Tanker operators aim to ke up full loads, but this is always easy. Part deliveries y empty the tank in stages. uids also vary in specific %My, so that a change to a ivier liquid may result in the al limit on gross vehicle ght being exceeded if the tanks are filled to capacity.
Dividing a tank into several compartments and providing internal baffles can ease the problem, but does not solve it. Too many compartments mean an uneconomic duplication of manholes and discharge fittings, while baffles complicate tank cleaning and maintenance.
Cocoa butter tanker
Cadbury came up against the surge problem in connection with the transport of liquid cocoa butter. Chocolate is made from cocoa beans, which Cadbury processes at its Chirk plant in North Wales, During processing the cocoa butter is extracted, to be added again later in different proportions to the lean chocolate "mass," depending on the end product to be manufactured. Manufacture takes place at Bournville, near Birmingham, which means that the cocoa butter must be transported about 70 miles, Existing tankers which have a capacity of 14 tons of cocoa butter have a gvw on the road of less than the 32-ton maximum. When the time came to add to the existing fleet, it was decided to get as close to the 32-ton gvw as possible, and it was felt that a 20-ton butter tanker would be possible.
The tank is of double-cone load-bearing construction, with two compartments (see Figure 1). There are external stiffening rings but no internal stays. lsopad electric heaters are fitted under stainless steel covers (see Figure 2) with Fibreglass insulation, because cocoa butter solidifies at ambient temperatures.
However, when the tanker was delivered it was found that the capacity of the tank was such that, fully laden with cocoa butter, its weight would be 20.3 tons. Loaded with other cocoabased materials of higher density, which will have to be. transported in the future, the weight would be even greater.
This alone would have resulted in a gross vehicle weight slightly in excess of 32 tons. Unfortunately there was also a variation in the tractive unit weight of nearly one ton. Consequently, to conform with current legislation, the tanker would have had to run with one of its compartments only partly filled.
Liquid density
This solution was unacceptable to Cadbury. The company's confectionery development engineers were asked to investigate the only choice left: to fill the unavoidable ullage space with some air bag or other space-consuming structure. This obviously meant some kind of hollow spheres and a survey of the market quickly pinpointed a range of plastics and a survey of the market quickly pinpointed a range of plastics balls made by Capricorn Industrial Services Ltd (1 Sugar House Lane, London, E15 2QN) and sold under the trade name of Allplas.
The Allplas system is well known in many industries, because a blanket of such balls floated on heated process liquids reduces heat losses by 70 per cent and evaporation losses by as much as 90 per cent. What interested Cadbury most was that the balls are available in food-grade polypropylene which is resistant to most industrial chemicals and is widely used in food processing plants, distilleries and even pharmaceutical plants.
The balls are made in diameters of 20, 45 and 150 mm (3/4, 13/4 and 6 inches). Because of a certain amount of nesting between layers, it requires ten 6in balls to fill a cubic foot of space. Simple cal
culations showed that, with a specific gravity of 0.853, the excess load of 1.3 tons of coacoa butter would leave a free space of 55 cu ft in the new 20-ton tanker. This space would be filled by 550 Alit:4as balls.
By putting 800 balls in each tanker, Cadbury has achieved an extremely stable load. The extra 250 balls force the cocoa butter level to rise and thus to submerge the lowest balls in the tank. The buoyancy of the submerged balls causes the ball packing to lock solid. A simple wire cage set into the manhole, as shown in Figure 3, prevents the balls from being lifted out should the cover be opened while the tank is full.
Integral rims
The main application ot the Allplas ball blanket system is in the electroplating, anodising, degreasing, pickling, dyeing, impregnating and similar industries, where heated tanks must be left open to permit products to be dipped and withdrawn. Floating balls tend to rotate, and rotating balls act as evaporators and coolers. To prevent this, Allplas balls have an integrally moulded circumferential rim.
This patented feature, shown at the top of page 43: causes balls in a blanket to lock together, thus preventing rotation. This rim also enhances the value of the balls as a surge preventer in tankers because it hinders the flow of liquid through the gaps between balls.
Preliminary tests carried out by Cadbury established that Allplas balls would not contaminate the cocoa butter. The Allplas balls have now been in use in the new 20-ton road tankers for several months and have proved satisfactory in every way.
The softening point of poly propylene is well above the boiling point of water, so that the balls may be left in the tanks for regular periodic tank cleaning. They are also resistant to the usual detergent solutions.
In fact, Allplas balls have a known resistance to most acids, alkalis, fats and oils, as borne out by their widespread industrial use. Their use as an antisurge packing for ullage spaces in tankers should be applicable to the transport of most industrial liquids. There are about 30,000 IT liquid tankers on British roa with a total capacity of so 400,000 tons. The anni movement of liquids amount! many millions of tons, so t even a small proportion partly filled tanks mi represent a considerable haza Allplas packs for ullage spa( could therefore contribt materially to road safety a could substantially reduce 1 accident risk carried by tanl operators.