DISTRIBUTION ... and how two big firms solve problems
Page 27
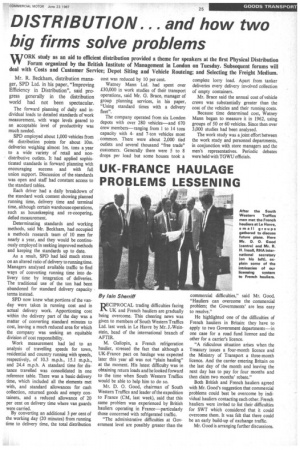
If you've noticed an error in this article please click here to report it so we can fix it.
WORK study as an aid to efficient distribution provided a theme for speakers at the first Physical Distribution Forum organized by the British Institute of Management in London on Tuesday. Subsequent forums will deal with Costs and Customer Service; Depot Siting and Vehicle Routeing; and Selecting the Freight Medium.
Mr. R. Beckham, distribution manager, SPD Ltd. in his paper, "Improving Efficiency in Distribution", said progress generally in the distribution world had not been spectacular.
The forward planning of daily and individual loads to detailed standards of work measurement, with wage levels geared to an acceptable level of productivity was much needed.
SPD employed about 1,000 vehicles from 46 distribution points for about 10m. deliveries weighing almost lm. tons a year to a wide variety of retail and nondistributive outlets. It had applied sophisticated standards in forward planning with encouraging success and with full union support. Discussion of the standards was open and staff had constant access to the standard tables.
Each driver had a daily breakdown of the standard work content showing planned running time, delivery time and terminal time, although certain warehouse operations, such as housekeeping and re-coopering, defied measurement.
Determinating standards and working methods, said Mr. Beckham, had occupied a methods research team of 10 men for nearly a year, and they would be continuously employed in seeking improved methods and keeping the standards up to date.
As a result, SPD had laid much stress on an altered ratio of delivery to running time. Managers analysed available traffic to find ways of converting running time into delivery time by integration of deliveries. The traditional use of the ton had been abandoned for standard delivery capacity terms instead.
SPD now knew what portions of the vanday were taken in running cost and in actual delivery work. Apportioning cost within the delivery part of the day was a matter of converting standard minutes to cost, leaving a much reduced area for which the company was seeking an equitable division of cost responsibility.
Work measurement had led to an analysis of travelling speeds for town, residential and country running with speeds, respectively, of 10.3 m.p.h., 15.1 m.p.h., and 24.4 m.p.h. A standard time for distance travelled was consolidated in one reference table. There was a basic delivery time, which included all the elements met with, and standard allowances for cash collection, returned goods and empty containers, and a reduced allowance of 20 per cent on delivery time where van guards were carried.
By converting an additional 3 per cent of the working day (20 minutes) from running time to delivery time, the total distribution cost was reduced by 10 per cent.
Watney Mann Ltd. had spent over 00,000 in work studies of their transport operations, said Mr. G. Brace, manager of group planning services, in his paper, "Using standard times with a delivery fleet".
The company operated from six London depots with over 280 vehicles—and 670 crew members—ranging from 1 to 14 tons capacity with 4and 7-ton vehicles most common. There were about 2,000 tied outlets and several thousand "free trade" customers. Generally there were 5 to 8 drops per load but some houses took a complete lorry load. Apart from tanker deliveries every delivery involved collection of empty containers.
Mr. Brace said the annual cost of vehicle crews was substantially greater than the cost of the vehicles and their running costs.
Because time determined cost, Watney Mann began to measure it in 1962, using groups of 50 or 60 vehicles. Since then over 3,000 studies had been analysed.
The work study was a joint effort between the work study and personnel departments, in conjunction with store managers and the men's representatives. Periodic debates were held with TGWU officials.