FTA data has the answers
Page 14
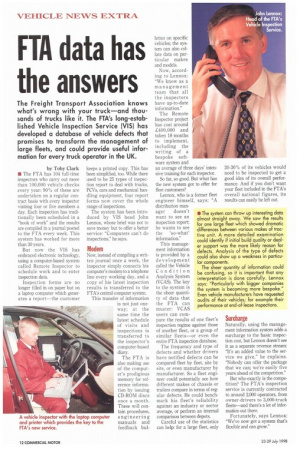
If you've noticed an error in this article please click here to report it so we can fix it.
The Freight Transport Association knows what's wrong with your truck—and thousands of trucks like it. The FTA's long-established Vehicle Inspection Service (VIS) has developed a database of vehicle defects that promises to transform the management of large fleets, and could provide useful information for every truck operator in the UK.
by Toby Clark • The FTA has 104 full-time inspectors who carry out more than 100,000 vehicle checks every year: 90% of these are undertaken on a regular contract basis with every inspector visiting four or five members a day. Each inspection has traditionally been scheduled in a "book of work" and the results are compiled in a journal posted to the FTA every week. This system has worked for more than 30 years.
But now the VIS has embraced electronic technology, using a computer-based system called Remote Inspector to schedule work and to enter inspection data.
Inspection forms are no longer filled in on paper but on a laptop computer which generates a report—the customer keeps a printed copy. This has been simplified, too. While there used to be 25 types of inspection report to deal with trucks, PCVs, cars and mechanical handling equipment, four report forms now cover the whole range of inspections.
The system has been introduced by VIS head John Lennox, whose brief was not to save money but to offer a better service: "Computers can't do inspections," he says.
Modem
Now, instead of compiling a written journal once a week, the inspector simply connects his computer's modem to a telephone line every working day, and a copy of his latest inspection results is transferred to the FTA's central computer system.
This transfer of information is not just oneway; at the same time the latest schedule of visits and inspections is transferred to the inspector's computer-based diary.
The FTA is also making use of the computer's prodigious memory for reference information by issuing CD-ROM discs once a month. These will contain procedures, engineering manuals and feedback bul
letins on specific vehicles; the system can also collate data on particular makes and models.
Now, according to Lennox: "We know as a management team that all the inspectors have up-to-date information."
The Remote Inspector project has cost around £400,000 and taken 18 months to implement, including the writing of a bespoke software system and an average of three days' intensive training for each inspector.
So far, so good. But what has the new system got to offer for fleet customers?
Lennox, who is a former fleet engineer himself, says: "A distribution man ager doesn't want to see an inspection report; he wants to see the 'so-what' information."
This management information is provided by a development called the Vehicle Condition Analysis System (VCAS). The key to the system is the sheer quantity of data that the FTA can muster: VCAS users can compare the results of one fleet's inspection regime against those of another fleet, or a group of similar fleets—or even the entire FTA inspection database.
The frequency and type of defects and whether drivers have notified defects can be compared fleet by fleet, site by site, or even manufacturer by manufacturer. So a fleet engineer could potentially see how different makes of chassis or trailers compare in terms of regular defects. He could benchmark his fleet's reliability against an industry or sector average, or perform an internal comparison between depots.
Careful use of the statistics can help: for a large fleet, only 20-30% of its vehicles would need to be inspected to get a good idea of its overall performance. And if you don't want your fleet included in the FTA's overall national figures, its results can easily be left out.
Surcharge
Naturally, using the management information system adds a surcharge to the basic inspection cost, but Lennox doesn't see it as a separate revenue stream: "It's an added value to the service we give," he explains. "Nobody can offer the package that we can; we're easily five years ahead of the competition."
But who exactly is the competition? The FTA's inspection service is currently contracted to around 2,000 operators, from owner-drivers to 3,000-truck fleets—and there's a lot of information out there.
Fortunately, says Lennox: "We've now got a system that's flexible and can grow." • The system can throw up interesting data almost straight away. We saw the results for one large fleet which showed dramatic differences lbetween various makes of tractive unit. A more detailed examination could identify if initial build quality or dealer support was the more likely reason for defects. Analysis of the type of defects could also show up a weakness in particular components. The sheer quantity of information could be confusing, so it is important that any interpretation is done carefully. Lennox says: "Particularly with bigger companies the system is becoming more bespoke." Even vehicle manufacturers have requested audits of their vehicles; for example their performance at end-of-lease inspections.