• In your strap tests (CM 11-17 June) we were
Page 42
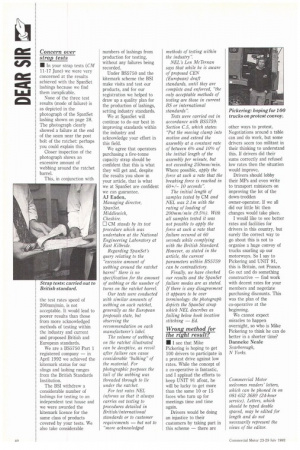
If you've noticed an error in this article please click here to report it so we can fix it.
very concerned at the results achieved with the SpanSet lashings because we find them inexplicable.
None of the three test results (mode of failure) is as depicted in the photograph of the SpanSet lashing shown on page 28. The photograph clearly showed a failure at the end of the seam near the post bolt of the ratchet: perhaps you could explain this.
Closer inspection of the photograph shows an excessive amount of webbing around the ratchet barrel.
the test rates speed of 200mm/min, is not acceptable. It would lead to poorer results than those from more acknowledged methods of testing within the industry and current and proposed British and European standards.
We are a BS5750 Part 1 registered company — in April 1992 we achieved the kitemark status for our slings and lashing ranges from the British Standards Institution.
The BSI withdrew a considerable number of lashings for testing to an independent test house and we were awarded the kitemark licence for the same class of products covered by your tests. We also take considerable numbers of lashings from production for testing, without any failures being recorded.
Under BS5750 and the kitemark scheme the BSI make visits and test our products, and for our registration we helped to draw up a quality plan for the production of lashings, setting industry standards, We at SpanSet will continue to do our best in improving standards within the industry and acknowledge your effort in this field.
We agree that operators purchasing a five-tonne capacity strap should be confident that this is what they will get and, despite the results you show in your article, that is what we at SpanSet are confident we can guarantee.
AJ Eaden, Managing director, SpanSet.
Middlewich, Cheshire.
0 CM stands by its test procedure which was undertaken at the National Engineering Laboratory at East Kilbride.
Regarding SpanSet's query relating to the "excessive amount of webbing around the ratchet barrel" there is no specification for the amount of webbing or the number of turns on the ratchet barrel.
Our tests were conducted with similar amounts of webbing on each ratchet, generally as the European proposals state, but observing the recommendation on each manufacturer's label.
The volume of webbing on The ratchet illustrated can be deceptive, as recoil after failure can cause considerable "bulking" of the material. For photographic Purposes the tail of the webbing was threaded through to lie under the ratchet.
For test rates NEL informs us that it always carries out testing to procedures detailed in British/international standards or to customer requirements — but not to "more acknowledged methods of testing within the industry".
NEL's Len McTernan says that while he is aware of proposed CEN (European) draft standards, until they are complete and enforced, "the only acceptable methods of testing are those in current ES or international standards".
Tests were carried out in accordance with BS5759: Section C.5, which states: "Put the moving clamp into motion and extend the assembly at a constant rate of between 6% and 10% of the initial length of the assembly per minute, but not exceeding 250mm/min. Where possible, apply the force at such a rate that the breaking force is reached in 60+/– 10 seconds".
The initial length of samples tested by CM and NEL was 2.1m with the rating of loading of 200mm/min (9.5%). With all samples tested it was not possible to apply the force at such a rate that failure occured at 60 seconds while complying with the British Standard. However, as stated in the article, the current parameters within BS5759 can be contradictory.
Finally, we have checked our results and the SpanSet failure modes are as stated. If there is any disagreement it appears to be over terminology: the photograph depicts the SpanSet strap which NEL describes as failing below hook location stitching — Ed.
• I see that Mike Pickering is hoping to get 100 drivers to participate in a protest drive against low rates. While the concept of a co-operative is fantastic, and I applaud the efforts to keep UNIT 91 afloat, he will be lucky to get more than the same 10 or 15 faces who turn up for meetings time and time again.
Drivers would be doing an injustice to their customers by taking part in this scheme — there are other ways to protest. Negotiations around a table can and do work, but some drivers seem too militant in their thinking to understand this. If drivers did their sums correctly and refused low rates then the situation would improve.
Drivers should lobby their MPs and even write to transport ministers on improving the lot of the down-trodden owner-operator. If we all did our little bit then changes would take place.
I would like to see better rates and facilities for drivers in this country, but surely the correct way to go about this is not to organise a huge convoy of trucks snarling up our motorways. So I say to Pickering and UNIT 91, this is Britain, not France. Go out and do something constructive — find work with decent rates for your members and negotiate purchasing discounts. This was the plan of the co-operative at the beginning.
We cannot expect miracles to happen overnight, so who is Mike Pickering to think he can do better in a shorter time? Danneke Neale Scarborough, N Yorks.