TIMBER!
Page 50
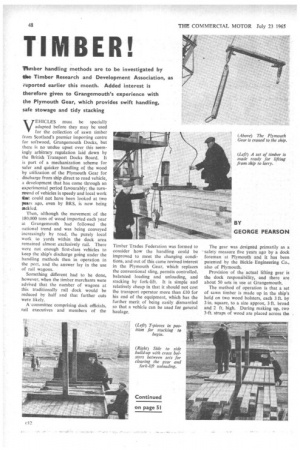
Page 53
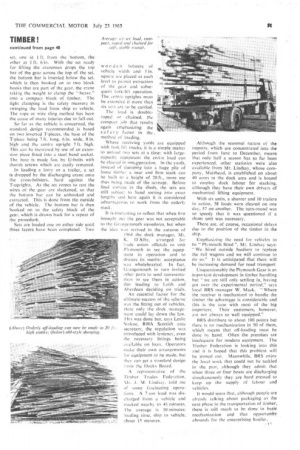
If you've noticed an error in this article please click here to report it so we can fix it.
Timber handling methods are to be investigated by Moe Timber Research and Development Association, as i,eported earlier this month. Added interest is therefore given to Grangemouth's experience with the Plymouth Gear, which provides swift handling, safe stowage and tidy stacking VEHICLES must be specially adapted before they may be used for the collection of sawn timber from Scotland's premier importing centre for softwood, Grangemouth Docks, but there is no undue upset over this seemingly arbitrary regulation laid down by the British Transport Docks Board. It is part of a mechanization scheme for safer and quicker handling of the wood by utilization of the Plymouth Gear for discharge from ship direct to road vehicle, a development that has come through an experimental period favourably; the turnround of vehicles is speedy and local work that could not have been looked at two years ago, even by BRS, is now being tack led.
Then, although the movement of the 180,000 tons of wood imported each year at Grangemouth had followed the national trend and was being conveyed increasingly by road, the purely local work to yards within the dock area remained almost exclusively rail. There were not enough first-class vehicles to keep the ship's discharge going under the handling methods then in operation in the port, and the answer lay in the use of rail wagons.
Something different had to be done, however, when the timber merchants were advised that the number of wagons at this traditionally rail dock would be reduced by half and that further cuts were likely.
A -committee comprising dock officials, rail executives and members of the
Timber Trades Federation was formed to consider how the handling could be improved to meet the changing conditions, and out of this came revived interest in the Plymouth Gear, which replaces the conventional sling, permits controlled. balanced loading and unloading, and stacking by fork-lift. It is simple and relatively cheap in that it should not cost the transport operator more than £.10 for his end of the equipment, which has the further merit of being easily dismantled so that a vehicle can be used for general haulage, The gear was designed primarily as a safety measure five years ago by a dock foreman at Plymouth and it has been patented by the Bickle Engineering Co., also of Plymouth.
Provision of the actual lifting gear is the dock responsibility, and there are about 50 sets in use at Grangemouth.
The method of operation is that a set of sawn timber is made up in the ship's hold on two wood bolsters, each 3 ft. by 3 in, square, to a size approx. 3 ft. broad and 2 ft. high. During making up, two 3-ft. straps of wood are placed across the
set, one at 1 ft. from . the bottom, the other at 1 ft. 6 in. With -the' set .ready for lifting the craneman drops the top bar of the gear across the top of the set, the bottom bar is inserted below the set, which is then hooked on to two block hooks that are part of the gear, the crane taking the weight to clamp the " heave " into a compact block of timber. The tight clampins is the safety measure in swinging the load from ship to vehicle. The rope or wire sling method has been the cause of many injuries due tQfall-out.
So far as the vehicle is concerned, the standard, design recommended , is based on two inverted T-Pieces, the base of the T-piece being 7 ft. long, 6 in, wide, 8 in. high and the centre upright 7 ft. high. This can he increased by use of an extension piece titled into a steel, hand socket. The base is made fast by U-bolts with thumb screws which are easily removed.
In loading a lorry or a trailer, a set is dropped by the discharging crane onto the cross-bolsters, hard against the T-uprights. As the set comes to rest the wires of the gear are slackened, so that the bottom bar can be unhooked and extracted. This is done from the outside of the vehicle. The bottom bar is then hooked on to the safely block of the gear, which is drawn back for a repeat of the procedure.
Sets are loaded one on either side until three layers have been completed. Two wooden bolsters of vehicle width and 3 in, square are placed at each level to permit extraction of the gear and subsequent fork-lift operation. The centre uprights must be extended if more than six sets are to be carried.
The load is doubleroped or chained, the compact job that results_ again emphasizing the saf c I y factor in the, method of loading.
Where receiving yards are equipped with fork-lift trucks, it is a simple matter to unload two sets at a time: with largecapacity equipment the entire load can be cleared in one,pperation. In the yards, instead of dumping into a huge pile of loose Muller a neat and firm stack can be built to a height of 20 ft., more use thus being made of the acreage. Before final storage in the sheds, the sets are still subject to hand sorting into exact lengths titta here again it is considered advantageous to work from the orderly stack, It is interesting to reflect that when first brought out the gear was not acceptable to the rangemouth stevedores, but when the idea was revived in the autumn of 1964 the dock manager, Mr. K. D'Alby, arranged for trade union officials to visit Plymouth to see the equipment in operation and to discuss its merits: acceptance was wholehearted. In fact, Grangemouth in turn invited other ports to send representatives to see them in action. this leading to T..eith and Aberdeen deciding on trials.
An essential factor for the ultimate success of the scheme was the fitting out of vehicles. Here only the dock manage: ment could lay down the law. This was done but, says Leslie Stokoe, RHA Scottish area secretary, the regulation was introduced with leniency, even the necessary fittings being available on loan. Operators make their own arrangements for equipment to he made, hut they can get a standard design from the Docks Board.
A representative _of the Timber Trades Federation. \Ir. A, N4. Lindsay. told me of some fascinating operations. A 7-ton load. was discharged freim as vehicle and stacked nearby in 4+ minutes. The average is 10 minutes; loading time. shin to vehicle, about 15 minutes. 'Although the seasonal nature of the imports, which are concentrated into the period from June to December, means that only half a season has so far been experienced, other statistics were also available from Mr. Lindsay, whose cornpany, Muirhead, is establishedon about 40 acres in the dock area and is bound to employ dock labour for stacking, although they have their own drivers of mechanical lifting equipment.
With six units, a shunter and 10 trailers in action, 58 loads were cleared on one day, 57 on another. The turn-round was so speedy that it was questioned if a shunt unit was necessary.
There are, of course, occasional delays due to the position of the timber in the ship.
Emphasizing the need for vehicles to " Plymouth fitted ", Mr. Lindsay says: " We hired outside hauliers to replace the rail wagons and we will continue to do so." It is anticipated that there will he increasing demand for road transport.
Unquestionably the Plymouth Gear is an important development in timber handling but " we are still only settling in, having got over the experimental period," says local BRS manager W. Mack. " Where the receiver is mechanized to handle the timher the advant4ge is considerable and this is the case with most of the big importers. Their customers, however, are not always so well equipped."
FIRS distribute to about 100 points but there is no mechanization in 50 of them, which means that off-loading must be done by hand. Often the premises are inadequate for modern equipment. The Timber Federation is looking into this and it is hoped that this problem will be ironed out. Meanwhile, BRS enjoy the local work that could not be tackled in the past, although they admit that when three or four boats are discharging simultaneously they are hard pressed to keep up the supply of labour arid vehicles.
It would seem that, although people are already talking about packaging as the next phase in the transportation of timber, there is still much to he done in basic mechanization and that opportunity abounds for the enterprising haulier.