Lubrication Systems for Commercial Vehicles.
Page 5
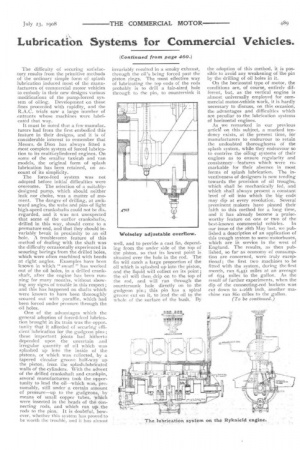
If you've noticed an error in this article please click here to report it so we can fix it.
The difficulty of securing satisfactory results from the primitive methods of the ordinary simple form of splash lubrication induced most of the manufacturers of commercial motor vehicles to embody in their new designs various modifications of the pump-forced system of oiling. Development on these fines proceeded with rapidity, and the R.A.C. trials saw a large number of entrants whose machines were lubricated that way.
It must be noted that a few manufac_ turers had from the first embodied this feature in their designs, and it is of considerable interest to remember that Messrs. de Dion has always fitted a Most complete system of forced lubrication to its multi-cylindered engines. On some of the smaller taxicab and van models, the original form of splash lubrication has been retained, on account of its simplicity.
The force-feed system was not adopted before initial difficulties were overcome. The selection of a suitablydesigned pump, which should neither leak nor choke, was a matter of moment. The danger of drilling, at awkward angles, the webs and pins of light high-speed crankshafts could not he dis_ regarded, and it was not unexpected that some of the earlier crankshafts, drilled in this way, should come to a premature end, and that they should invariably break in proximity to an oil hole. A troublesome feature of this method of dealing with the shaft was the difficulty occasionally experienced in scouring borings from the drilled holes, which were often machined with bends at right angles. Examples have been known in which " swarf " has worked out of the oil holes, in a drilled crankshaft, after the engine has been running for many months, without showing any signs of trouble in this respect ; and this has happened on shafts which were known to have been thoroughly scoured out with paraffin, which had been forced under pressure through the oil holes.
One of the advantages which the general adoption of forced-feed lubrication brought in its train was the oppor_ tunity that it afforded of securing efficient lubrication for the gudgeon pins ; these important joints had hitherto depended upon the uncertain and irregular quantity of oil which was splashed up into the inside of the pistons, or which was collected, by a tapered circular groove half-way up the piston, from the splash-lubricated walls of the cylinders. With the advent of the drilled crankshaft and crankpin, several manufacturers took the Opportunity to lead the oil—which was; pre
sumably, still under a certain amount of pressure—up to the gudg-eons, by means of small copper tubes, which were inserted in the beads of the
önnecting rods, and which ran up. the rods to the pins. It is doubtful, however, whether this system has proved to be worth the trouble, and it has almost
invariably resulted in a smoky exhaust, through the oil's being forced past the piston rings. The most effective way of lubricating the top ends of the rods probably is to drill a fair-sized hole through to the pin, to countersink it
well, and to provide a east fin, depending from the under side of the top of the piston, so that its lowest point is situated over the hole in the rod. The fin will catch a large proportion of the oil which is splashed up into the piston, and the liquid will collect on its point ; the oil will then, drip on to the top of the rod, and will run through the countersunk hole directly on to the gudgeon pin ; this pin has a spiral groove cut en it, to lead the oil to the whole of the surface of the bush. By the adoption of this method, it is possible to avoid any weakening of the pin by the drilling of oil holes in it.
On the horizontal type of motor, the conditions are, of course, entirely different, but, as the vertical engine is almost universally employed for commercial motor-vehicle work, it is hardly necessary to discuss, on this occasion, the advantages and difficulties which are peculiar to the lubrication systems of horizontal engines.
As we remarked in our previous article' on this subject, a marked tendency exists, at the present time, for manufacturers to endeavour to retain the undoubted thoroughness of the splash system, while they endeavour so to contrive the oiling systems of their engines as to ensure regularity and consistency—features which were remarkable for their absence in most forms of splash lubrication. The inventiveness of designers is now tending towards the provision of oil troughs, which shall be mechanically fed, and which shall always present a constant level of oil into which the big ends may dip at every revolution. Several prominent makers have pinned their faith to this method for a long time, and it has already become a praiseworthy feature on one or two of the best-known commercial vehicles. In our issue of the 28th May last, we published a description of an application of this trough system to some motorbuses, which are in service in the west of England. The results, as then published, so far as economy of consumption are concerned, were truly exceptional; the first two machines to be fitted with the system, during the first month, ran 6,451 miles at an average of 634 miles to the gallon. As the result of further experiments, when the dip of the connecting-rod ,buckets was cut down to 1-i6th inch, another machine ran 86o miles to the gallon.