Tipping the
Page 18
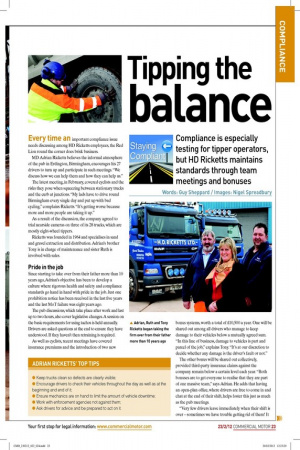
Page 19
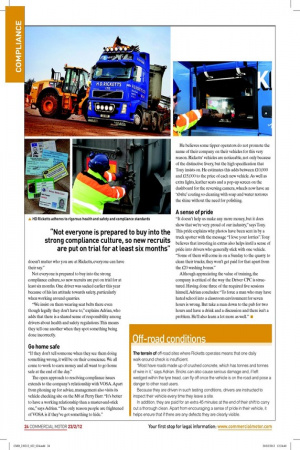
If you've noticed an error in this article please click here to report it so we can fix it.
balance
Compliance is especially testing for tipper operators, but HD Ricketts maintains standards through team meetings and bonuses
Words: Guy Sheppard / Images: Nigel Spreadbury Every time an important compliance issue needs discussing among HD Ricketts employees, the Red Lion round the corner does brisk business.
MD Adrian Ricketts believes the informal atmosphere of the pub in Erdington, Birmingham, encourages his 27 drivers to turn up and participate in such meetings. “We discuss how we can help them and how they can help us.” The latest meeting, in February, covered cyclists and the risks they pose when squeezing between stationary trucks and the curb at junctions. “My lads have to drive round Birmingham every single day and put up with bad cycling,” complains Ricketts. “It’s getting worse because more and more people are taking it up.” As a result of the discussion, the company agreed to trial nearside cameras on three of its 28 trucks, which are mostly eight-wheel tippers.
Ricketts was founded in 1964 and specialises in sand and gravel extraction and distribution. Adrian’s brother Tony is in charge of maintenance and sister Ruth is involved with sales.
Pride in the job
Since starting to take over from their father more than 10 years ago, Adrian’s objective has been to develop a culture where rigorous health and safety and compliance standards go hand in hand with pride in the job. Just one prohibition notice has been received in the last ive years and the last MoT failure was eight years ago.
The pub discussions, which take place after work and last up to two hours, also cover legislative changes. A session on the basic requirements for using tachos is held annually. Drivers are asked questions at the end to ensure they have understood. If they haven’t then retraining is required.
As well as cyclists, recent meetings have covered insurance premiums and the introduction of two new bonus systems, worth a total of £10,500 a year. One will be shared out among all drivers who manage to keep damage to their vehicles below a mutually agreed sum. “In this line of business, damage to vehicles is part and parcel of the job,” explains Tony. “It’s at our discretion to decide whether any damage is the driver’s fault or not.” The other bonus will be shared out collectively, provided third-party insurance claims against the company remain below a certain level each year. “Both bonuses are to get everyone to realise that they are part of one massive team,” says Adrian. He adds that having an open-plan ofice, where drivers are free to come in and chat at the end of their shift, helps foster this just as much as the pub meetings.
“Very few drivers leave immediately when their shift is over – sometimes we have trouble getting rid of them! It doesn’t matter who you are at Ricketts, everyone can have their say.” Not everyone is prepared to buy into the strong compliance culture, so new recruits are put on trial for at least six months. One driver was sacked earlier this year because of his lax attitude towards safety, particularly when working around quarries.
“We insist on them wearing seat belts there even though legally they don’t have to,” explains Adrian, who adds that there is a shared sense of responsibility among drivers about health and safety regulations. This means they tell one another when they spot something being done incorrectly.
Go home safe
“If they don’t tell someone when they see them doing something wrong, it will be on their conscience. We all come to work to earn money and all want to go home safe at the end of the day.” The open approach to resolving compliance issues extends to the company’s relationship with VOSA. Apart from phoning up for advice, management also visits its vehicle checking site on the M6 at Perry Barr. “It’s better to have a working relationship than a master-and-stick one,” says Adrian. “The only reason people are frightened of VOSA is if they’ve got something to hide.” He believes some tipper operators do not promote the name of their company on their vehicles for this very reason. Ricketts’ vehicles are noticeable, not only because of the distinctive livery, but the high speciication that Tony insists on. He estimates this adds between £10,000 and £15,000 to the price of each new vehicle. As well as extra lights, leather seats and a pop-up screen on the dashboard for the reversing camera, wheels now have an ‘xbrite’ coating so cleaning with soap and water restores the shine without the need for polishing.
A sense of pride
“It doesn’t help us make any more money, but it does show that we’re very proud of our industry,” says Tony. This pride explains why photos have been sent in by a truck spotter with the message “I love your lorries” . Tony believes that investing in extras also helps instil a sense of pride into drivers who generally stick with one vehicle. “Some of them will come in on a Sunday to the quarry to clean their trucks; they won’t get paid for that apart from the £20 washing bonus.”
Although appreciating the value of training, the company is critical of the way the Driver CPC is structured. Having done three of the required ive sessions himself, Adrian concludes: “To force a man who may have hated school into a classroom environment for seven hours is wrong. But take a man down to the pub for two hours and have a drink and a discussion and there isn’t a problem. He’ll also learn a lot more as well.” ■
ADRIAN RICKETTS’ TOP TIPS
• Keep trucks clean so defects are clearly visible; • Encourage drivers to check their vehicles throughout the day as well as at the beginning and end of it; • Ensure mechanics are on hand to limit the amount of vehicle downtime; • Work with enforcement agencies not against them; • Ask drivers for advice and be prepared to act on it.
Off-road conditions
The terrain of off-road sites where Ricketts operates means that one daily walk-around check is insufficient.
“Most have roads made up of crushed concrete, which has tonnes and tonnes of wire in it,” says Adrian. Bricks can also cause serious damage and, if left wedged within the tyre tread, can fly off once the vehicle is on the road and pose a danger to other road users.
Because they are driven in such testing conditions, drivers are instructed to inspect their vehicle every time they leave a site.
In addition, they are paid for an extra 45 minutes at the end of their shift to carry out a thorough clean. Apart from encouraging a sense of pride in their vehicle, it helps ensure that if there are any defects they are clearly visible.