Raise these points .
Page 49
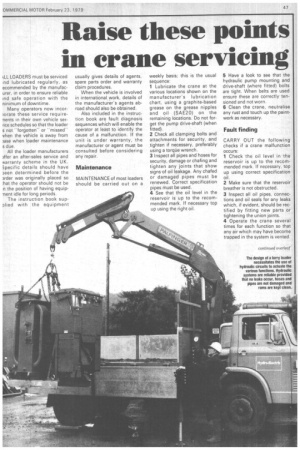
Page 50
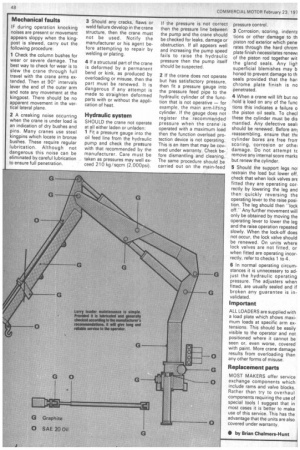
If you've noticed an error in this article please click here to report it so we can fix it.
m crane servicing
kLL LOADERS must be serviced Ind lubricated regularly, as ecommended by the manufacurer, in order to ensure reliable ind safe operation with the ninimum of downtime.
Many operators now incor)orate these service requirenents in their own vehicle serrice schedules so that the loader s not -forgottenor "missed.' when the vehicle is away from )ase when loader maintenance s due.
All the loader manufacturers )ffer an after-sales service and warranty scheme in the UK. 3pecific details should have peen determined before the )rder was originally placed so :hat the operator should not be n the position of having equipTient idle for long periods.
The instruction book supplied with the equipment usually gives details of agents, spare parts order and warranty claim procedures.
When the vehicle is involved in international work, details of the manufacturer's agents abroad should also be obtained.
Also included in the instruction book are fault diagnosis sequences which will enable the operator at least to identify the cause of a malfunction. If the unit is under warranty, the manufacturer or agent must be consulted before considering any repair.
Maintenance
MAINTENANCE of most loaders should be carried out on a weekly basis; this is the usual sequence: 1 Lubricate the crane at the various locations shown on the manufacturer's lubrication chart, using a graphite-based grease on the grease nipples and oil (SAE20) on the remaining locations. Do not forget the pump drive-shaft (when fitted).
2 Check all clamping bolts and attachments for security, and tighten if necessary, preferably using a torque wrench.
3 Inspect all pipes and hoses for security, damage or chafing and tighten any joints that show signs of oil leakage. Any chafed or damaged pipes must be renewed. Correct specification pipes must be used.
4 See that the oil level in the reservoir is up to the recommended mark. If necessary top up using the right oil 5 Have a look to see that the hydraulic pump mounting and drive-shaft (where fitted) bolts are tight. When belts are used ensure these are correctly tensioned and not worn.
6 Clean the crane, neutralise any rust and touch up the paintwork as necessary.
Fault finding
CARRY OUT the following checks if a crane malfunction occurs: 1 Check the oil level in the reservoir is up to the recommended mark. If necessary, top up using correct specification oil.
2 Make sure that the reservoir breather is not obstructed.
3 Inspect all oil pipes, connections and oil seals for any leaks which, if evident, should be rectified by fitting new parts or tightening the union joints.
4 Operate the crane several times for each function so that any air which may have become trapped in the system is vented. IF during operation knocking noises are present or movement appears sloppy when the kingpost is slewed, carry out the following procedure:
1 Check the column bushes for wear or severe damage. The best way to check for wear is to slew the crane through full travel with the crane arms extended. Then at 90 intervals lever the end of the outer arm and note any movement at the kingpost. There should be no apparent movement in the vertical lateral plane.
2 A creaking noise occurring when the crane is under load is an indication of dry bushes and pins. Many cranes use steel kingpins which locate in bronze bushes. These require regular lubrication. Although not dangerous this noise can be eliminated by careful lubrication to ensure full penetration. 3 Should any cracks, flaws or weld failure develop in the crane structure, then the crane must not be used. Notify the manufacturer or his agent before attempting to repair by welding or plating.
4 If a structural part of the crane is deformed by a permanent bend or kink, as produced by overloading or misuse, then the part must be renewed. It is dangerous if any attempt is made to straighten deformed parts with or without the application of heat.
Hydraulic system
SHOULD the crane not operate at all either laden or unladen:
1 Fit a pressure gauge into the oil feed line from the hydraulic pump and check the pressure with that recommended by the manufacturer. Care must be taken as pressures may well exceed 210 kg /sqcm (2.000psi).
If the pressure is not correct then the pressure line between the pump and the crane should be checked for leaks, damage or obstruction. If all appears well and increasing the pump speed fails to raise the hydraulic pressure then the pump itself should be suspected.
2 If the crane does not operate but has satisfactory pressure, then fit a pressure gauge into the pressure feed pipe to the hydraulic cylinder of the function that is not operative — for example, the main arm-lifting cylinder. If the gauge does not register the recommended pressure when the crane is operated with a maximum load then the function overload protection device is not operating. This is an item that may be covered under warranty. Check before dismantling and cleaning. The same procedure should be carried out on the main-feed
pressure control.
3 Corrosion, scoring, indents tions or other damage to th piston rod exterior which pene rates through the hard chrom plate finish necessitates renew of the piston rod together wit the gland seals. Any ligh superficial blemishes may b honed to prevent damage to th seals provided that the har chrome plate finish is no penetrated.
4 When a crane will lift but no hold a load on any of the func tions this indicates a failure o the piston oil seals. To checl these the cylinder must be dis mantled. Any defective seal! should be renewed. Before ant reassembling, ensure that thr cylinder bores are free frorr scoring, corrosion or othel damage. Do not attempt tc remove any internal score marks but renew the cylinder.
5 Should the support legs no restrain the load but lower off, check that when lock valves arE fitted they are operating correctly by lowering the leg and then quickly reversing the operating lever to the raise position. The leg should then -lock off.Any further movement will only be obtained by moving the operating lever to lower the leg and the raise operation repeated slowly. When the lock-off does not occur, the lock valve should be renewed. On units where lock valves are not fitted, or when fitted are operating incorrectly, refer to checks 1 to 4.
6 In normal operating circumstances it is unnecessary to adjust the hydraulic operating pressure. The adjusters when fitted, are usually sealed and if broken any guarantee is invalidated.
Important
ALL LOADERS are supplied with a load plate which shows maximum loads at specific arm extensions. This should be easily visible to the operator and not positioned where it cannot be seen or, even worse, covered with paint. More crane damage results from overloading than any other forms of misuse.
Replacement parts
MOST MAKERS offer service exchange components which include rams and valve blocks. Rather than try to overhaul components requiring the use of special tools I suggest that in most cases it is better to make use of this service. This has the advantage that the units are also covered under warranty.
• by Brian Chalmers-Hunt