Utilize cranes to grab, not smash
Page 47
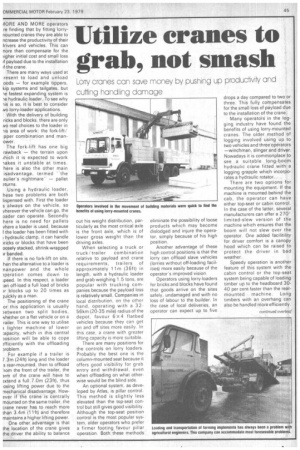
Page 48
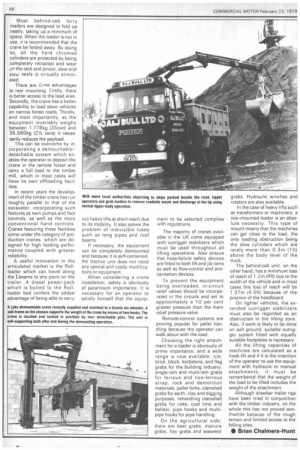
If you've noticed an error in this article please click here to report it so we can fix it.
Lorry cranes can save money by pushing up productivity and cutting handling damage
AORE AND MORE operators re finding that by fitting lorry nounted cranes they are able to ncrease the productivity of their Myers and vehicles. This can nore than compensate for the iigher initial cost and small loss if payload due to the installation if the crane.
There are many ways used at resent to load and unload oods — for example tippers, kip systems and tailgates, but ie fastest expanding system is hydraulic loader. To see why
is so, it is best to consider NO lorry-loader applications.
With the delivery of building ricks and blocks, there are only NO real choices to the loader in "'is area of work: the fork-lift/ pper combination and manower.
The fork-lift has one big rawback — the terrain upon ihich it is expected to work lakes it unstable at times. here is also the other main isadvantage, termed "the aulier's nightmare.' — pallet turns.
Using a hydraulic loader, hese two problems are both lispensed with. First the loader s always on the vehicle, so vherever the vehicle can go, the oader can operate. Secondly here is no need for pallets vhere a loader is used, because I the loader has been fitted with hydraulic clamp, it can handle iricks or blocks that have been oosely stacked, shrink-wrapped )r banded.
If there is no fork-lift on site, hen the alternative to a loader is nanpower and the whole )peration comes down to ;peed. In this respect, a loader ;an off-load a full load of bricks >r blocks up to 20 times as luickly as a man.
The positioning of the crane or this application is usually )etween two split bodies, vhether on a flat vehicle or on a railer. This is one way to utilise 3 lighter machine of lower ;apacity, which in this central )osition will be able to cope 3fficiently with the offloading Noblem.
For example if a trailer is 7.3m (24ft) long and the loader s rear-mounted, then to offload :rom the front of the trailer, the 3rm of the crane will have to axtend a full 7.0m (23ft), thus osing lifting power due to the mechanical disadvantage. Howaver if the crane is centrally mounted on the same trailer, the crane never has to reach more than 3.4m (lift) and therefore maintains a higher lifting power.
One other advantage is that the location of the crane gives the driver the ability to balance out his weight distribution, particularly as the most critical axle is the front axle, which is of lower gross weight than the driving axles.
When selecting a truck or truck/ trailer combination relative to payload and crane requirements, trailers of approximately 11 m (36ft) in length, with a hydraulic loader and grab weighing 1.5 tons, are popular with trucking companies because the payload loss is relatively small. Companies in local distribution, on the other hand, operating with a 3256km (20-35 mile) radius of the depot, favour 6 x 4 flatbed vehicles because they can get on and off sites more easily. In this case, a crane with greater lifting capacity is more suitable.
There are many positions for the controls on lorry loaders. Probably the best one is the column-mounted seat because it offers good visibility for grab entry and withdrawal, even when offloading on what otherwise would be the blind side.
An optional system, as developed by Atlas, is pillar control. This method is slightly less elevated than the top-seat control but still gives good visibility. Although the top-seat position control is the most popular system, older operators who prefer a firmer footing favour pillar operation. Both these methods eliminate the possibility of loose products which may become dislodged and injure the operator, simply because of his high position.
Another advantage of these high control positions is that the lorry can offload slave vehicles (lorries without off-loading facilities) more easily because of the operator's improved vision Operators using lorry-loaders for bricks and blocks have found that goods arrive on the sites safely, undamaged and with no loss of labour to the builder. In the case of local deliveries, an operator can expect up to five drops a day compared to two or three. This fully compensates for the small loss of payload due to the installation of the crane.
Many operators in the logging industry have found the benefits of using lorry-mounted cranes. The older method of logging involved using up to two vehicles and three operators —winchman, slinger and driver. Nowadays it is commonplace to see a suitable long-boom hydraulic crane fitted with a logging grapple which incorporates a hydraulic rotator.
There are two options for mounting the equipment. If the machine is mounted behind the cab, the operator can have either top-seat or cabin control. In the case of the latter, several manufacturers can offer a 270limited-slew version of the machine which ensures that the boom will not slew over the operator. One added facilitility for driver comfort is a canopy hood which can be raised to protect the driver in bad weather.
Speedy operation is another feature of this system with the cabin control or the top-seat system being capable of loading timber up to the headboard 3040 per cent faster than the rearmounted machine. Long timbers with an overhang can also be handled more efficiently. Most behind-cab lorry loaders are designed to fold up neatly, taking up a minimum of space. When the loader is not in use, it is recommended that the crane be folded away. By doing so, all the hard chromed cylinders are protected by being completely retracted and wear on the rack and pinion, slew and slew seals is virtually eliminated.
There are three advantages to rear mounting. i-irstly, there is better access to the load area.
Secondly, the crane has a better capability to load slave vehicles on narrow forest roads. Thirdly, and most importantly, as the equipment invariably weighs between 1,778kg (35cwt) and 35,560kg (21/2 tons) it necessarily reduces the payload.
This can be overcome by incorporating a demountable/ detachable system which en ables the operator to deposit the crane in the remote forest and carry a full load to the timber mill, which in most cases will have its own offloading facilities.
In recent years the development of the timber crane has run roughly parallel to that of the excavator, incorporating such features as twin pumps and foot controls, as well as the more conventional hand controls.
Cranes featuring these facilities come under the category of pro duction cranes, which are designed for high loading performance coupled with greater reliability.
A useful innovation in the articulated market is the Rollloader which can travel along the I-beams to any point on the trailer. A diesel power-pack which is bolted to the Rollloader bed confers the added advantage of being able to carry out heavy lifts at short reach due to its mobility. It also solves the problem of indivisible loads such as long pipes and roof beams.
If necessary, the equipment can be completely demounted and because it is self-contained, the tractive unit does not need any special and costly modifications or equipment.
When considering a crane installation, safety is obviously of paramount importance. It is necessary for an operator to satisfy himself that the equip merit to be selected complies with regulations.
The majority of cranes available in the UK come equipped with outrigger stabilisers which must be used throughout all lifting operations. Also ensure that hose-failure safety devices are fitted to both lift and jib rams as well as flow-control and anticavitation devices.
To prevent the equipment being overloaded, in-circuit relief valves should be incorporated in the circuits and set to approximately a 10 per cent greater pressure than the main relief pressure valve.
Remote-control systems are proving popular for pallet handling because the operator can walk about with the load.
Choosing the right attachment for a loader is obviously of prime importance, and a wide range is now available: tile, brick, block, kerbstone, and flag grabs for the building industry, single-ram and multi-ram grabs for ferrous and non-ferrous scrap, rock and demolition materials, pallet forks, clamshell grabs for earth, clay and digging purposes, rehandling clamshell grabs for coke, coal lime and ballast, pipe hooks and multipipe hooks for pipe handling.
On the agricultural side, there are beet grabs, manure grabs, hay grabs and seaweed grabs. Hydraulic winches and rotators are also available.
In the case of heavy lifts such as transformers or machinery, a rear-mounted loader is an absolute necessity. This type of mount Means that the machines can get close to the load, the only loading obstruction being the slew cylinders which are rarely more than 0.3m (1ft) above the body level of the truck.
The behind-cab unit, on the other hand, has a minimum loss of reach of 1.2m (4ft) due to the width of the vehicle and in most cases this loss of reach will be 1.37m (4.5ft) because of the position of the headboard.
On lighter vehicles, the extended outrigger stabilizers must also be regarded as an obstruction in the lifting zone. Also, if work is likely to be done on soft ground, suitable outrigger system fitted with equally suitable footplates is necessary.
All the lifting capacities of machines are calculated as a hook lift and if it is the intention of the operator to use the equipment with hydraulic or manual attachments, it must be remembered that the weight of the load to be lifted includes the weight of the attachment.
Although drawbar trailer rigs have been tried in conjunction with the timber industry, on the whole this has not proved worthwhile because of the rough terrain and limited access to the felling sites.
• Brian Chalmers-Hunt