road and
Page 34
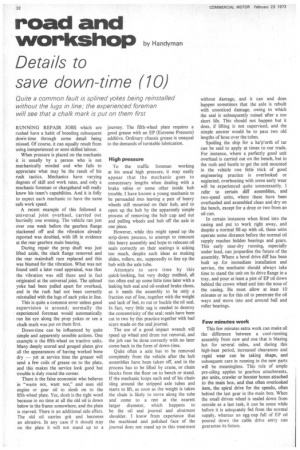
If you've noticed an error in this article please click here to report it so we can fix it.
workshop by Handyman
Details to save down-time (10)
Quite a common fault is splined yokes being reinstalled without the lugs in line,the experienced foreman will see that a chalk mark is put on them first
RUNNING REPAIR JOBS which are rushed have a habit of breeding subsequent down-time through some detail being missed. Of course, it can equally result from using inexperienced or semi-skilled labour.
When pressure is placed on the mechanic it is usually by a person who is not mechanically minded and who fails to appreciate what may be the result of his rush tactics. Mechanics have varying degrees of skill and work rates, and only a mechanic foreman or chargehand will really know his team's capabilities. And it is folly to expect each mechanic to have the same safe work speed.
A recent example of this followed a universal joint overhaul, carried out hurriedly one evening. The vehicle ran just over one week before the gearbox flange slackened off and the vibration already reported was doubled, with lift in evidence at the rear gearbox main bearing.
During repair the prop shaft was just lifted aside, the slack flange removed and the rear mainshaft race replaced and this was blamed for the vibration. What was not found until a later road appraisal, was that the vibration was still there and in fact originated at the universal joint. The splined yoke had been pulled apart for overhaul, and in the rush had not been correctly reinstalled with the lugs of each yoke in line.
This is quite a common error unless good supervision is around; normally the experienced foreman would automatically run his eye along the prop yokes or see a chalk mark was put on them first.
Down-time can be influenced by quite simple and apparently sensible actions. One example is the fifth-wheel on tractive units. Many deeply scored and gouged plates give all the appearances of having worked bone dry — yet at service time the greaser will send a few coils of grease on to the plate, and this makes the service look good but trouble is duly round the corner.
There is the false economist who believes in "waste not, want not," and uses old engine or gear oil to slosh on to the fifth-wheel plate. Yes, slosh is the right word because in no time at all the old oil is down below in the frame somewhere, and the plate is starved. There is an additional side effect. The old oil carries grit and becomes an abrasive. In any case if it should stay on the plate it will not stand up to a journey. The fifth-wheel plate requires a good grease with an EP (Extreme Pressure) additive. Ordinary chassis grease is unequal to the demands of turntable lubrication.
High pressure To the traffic foreman working at his usual high pressure, it may easily appear that the mechanic goes to unnecessary lengths when dealing with a brake reline or some other inside hub trouble. I have known a young mechanic to be persuaded into leaving a pair of heavy wheels still mounted on their hub, and to open up the hub by the apparently simple process of removing the hub cap and nut and pulling wheels and hub off the axle in one piece.
However, while this might speed up the strip-down process, to attempt to remount this heavy assembly and hope to relocate oil seals correctly on their seatings is asking too much, despite such ideas as making slides, rollers, etc, supposedly to line up the hub with the axle tube.
Attempts to save time by this quick-looking, but very dodgy method, all too often end up some little time later with a leaking hub seal and oil-soaked brake shoes, as it needs the assembly to be only a fraction out of line, together with the weight and lack of feel, to cut or buckle the oil seal. In fact, very little sag is needed to destroy the concentricity of the seal; seals have been cut in two by this practice together with bad scars made on the seal journal.
The use of a good impact wrench will speed up wheel and drum nut removal, and the job can be done correctly with no later come-back in the form of down-time.
Quite often a axle has to be removed completely from the vehicle after the hub assemblies have been taken off, and in the process has to be lifted by crane, or chain blocks from the floor on to bench or stand. If the mechanic loops each end of his chain sling around the stripped axle tubes and starts to lift, as soon as the weight is taken the chain is likely to move along the tube and come to a rest at the nearest larger diameter, which happens to be the oil seal journal and abutment shoulder. I know from experience that the machined and polished face of the journal does not stand up to this treatment
without damage, and it can and does happen sometimes that the axle is rebuilt with unnoticed damage, owing to which the seal is subsequently ruined after a too short life. This should not happen but it does, if lifting is not supervised, and the simple answer would be to pass two old lengths of hose over the tubes.
Spoiling the ship for a ha'p'orth of tar can be said to apply at times to our trade. For instance, where a perfectly good unit overhaul is carried out on the bench, but in the rush and bustle to get the unit mounted in the vehicle one little trick of good engineering practice is overlooked or neglected, overheating with some early wear will he experienced quite unnecessarily. I refer to certain dill assemblies, and two-speed units, where these have been overhauled and assembled clean and dry on the bench, except for a drop or two from an oil can.
In certain instances when fitted into the casing and put to work right away, and despite a normal fill-up with oil, these units operate some distance before the normal oil supply reaches hidden bearings and gears. This early near-dry running, especially under load, can jeopardise the future of the assembly. Where a bevel drive diff has been built up for immediate installation and service, the mechanic should always take time to stand the unit on its drive flange in a tray, and pour at least a pint of EP oil down behind the crown wheel and into the nose of the casing. He must allow at least 10 minutes or so for this oil to penetrate the oil ways and move into and around ball and roller bearings.
Few minutes work
This few minutes extra work can make all the difference between a cool-running assembly from new and one that is blazing hot for several miles, and during this high-heat period, increased clearances and rapid wear can be taking shape, and subsequent care in running in the new parts will be meaningless. This rule of ample pre-oiling applies to gearbox attachments, pto units, crawler or booster boxes attached to the main box, and that often overlooked item, the spiral drive for the speedo, often behind the last gear in the main box. When the small driven wheel is sealed down from outside as a last task, it can be some while before it is adequately fed from the normal supply, whereas an egg-cup full of EP oil poured down the cable drive entry can guarantee its future.