By - A A. OWNSft: A.\ . 7 Meeli,E .S11 ( 3-,ii or , f.• e2. , .... c:nples
Page 80
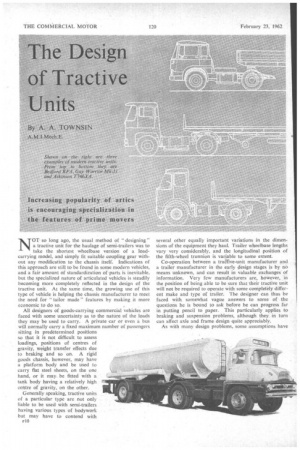
Page 81
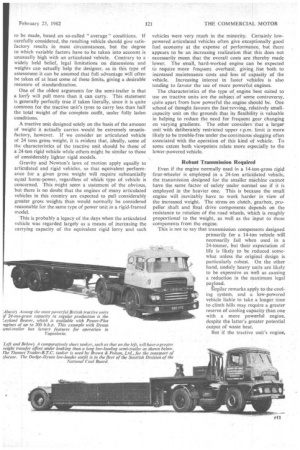
Page 82
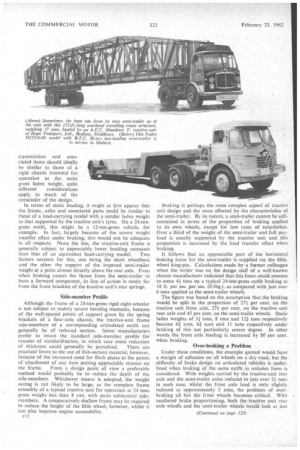
Page 85
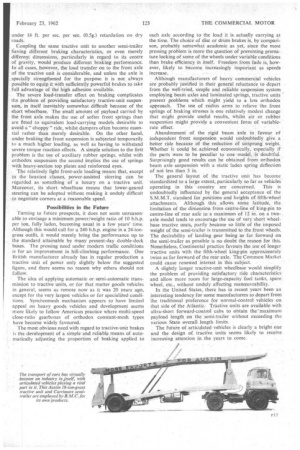
If you've noticed an error in this article please click here to report it so we can fix it.
1)1. frh)ot ■ 1 fr t.r'iii,:(.' NYV: I: Froin inp tr,. H thc--., tr■-e
...,
(P'.4, r.";ziy 01[Irrto,, Mic . I i
_
and A ri ificreasira;; p‘ipalaritN of art • • • S erteottniglrig specialIration ill e felifttires Of pritrie mwvers NOT. so long ago, the usual method of " designing " a tractive unit for the haulage of semi-trailers was to take the shortest wheelbase version of a loadcarrying model, and simply fit suitable coupling gear without any modification to the chassis itself. Indications of this approach are still to be found in some modern vehicles, and a fair amount of standardization of parts is inevitable, but the specialized nature of articulated vehicles is steadily becoming more completely reflected in the design of the tractive unit. At the same time, the growing use of this type of vehicle is helping the chassis manufacturer to meet the need for "tailor made" features by making it more economic to do so. . All designers of goods-carrying commercial vehicles are faced with some uncertainty as to the nature of the loads they may be used to carry. A private car or even a bus will normally carry a fixed maximum number of passengers sitting in predetermined positions so that it is not difficult to assess loadings, positions of centres of gravity, weight transfer effects due to braking and so on. A rigid goods chassis, however, may have a platform body and be used to carry flat steel sheets, on the one hand, or it may, be fitted with a tank body having a relatively high centre of gravity, on the other. Generally speaking, tractive units of a particular type are not only liable to be used with semi-trailers having various types of bodywork but may have to contend with several other equally important variations in the dimensions of the equipment they haul. Trailer wheelbase lengths vary very considerably, and the longitudinal position of the fifth-wheel trunnion is variable to some extent. Co-operation between a traCtive-unit manufacturer and a trailer manufacturer in the early design stages is by no means unknown, and can result in valuable exchanges of information. Very few manufacturers are, however, in the position of being able to be sure that their tractive unit will not be required to operate with some completely different make and type of trailer. The designer can thus be faced with somewhat vague answers to some of the questions he is bound to ask before he can progress far in putting pencil to paper. This particularly applies to braking and suspension problems, although they in turn can affect axle and frame design quite appreciably. As with many design problems, some assumptions have to be made, based on so-called " average " conditions. If carefully considered, the resulting vehicle should give satisfactory results in most circumstances, but the degree to which variable factors have to be taken into account is unusually high with an articulated Vehicle. Contrary to a widely held belief, legal limitations on dimensions and weights can actually help the designer, as in this type of assessment it can be assumed that full advantage will often be taken of at least some of these limits, giving a desirable measure of standardization. One Of the oldest arguments for the semi-trailer is that a lorey will pull more than it can carry. This statement is generally perfectly true if taken literally, since it is quite common for the tractive unit's tyres to Carry less than half the total weight of the complete outfit, under fully laden conditions. A tractive unit designed solely on the basis of the amount of weight it actually carries would be extremely unsatisfactory, however. If we consider an articulated vehicle of 24 tons gross weight, it is evident that, ideally, some of the characteristics of the tractive unit should be those of a 24-ton rigid vehicle while others might be similar to those of considerably lighter rigid models. Gravity and Newton's laws of motion apply equally to articulated and rigid vehicles, so that equivalent performance for a given gross weight will require substantially equal horse-power, regardless of which type of vehicle is concerned. This might seem a statement of the obvious, but there is no doubt that the engines of many articulated vehicles in this country are expected to pull considerably greater gross weights than would normally be considered reasonable for the same type of power unit in a rigid-framed model. This is probably a legacy of the days when the articulated vehicle was regarded largely as a means of increasing the carrying capacity of the equivalent rigid lorry and such vehicles were very much in the minority. Certainly lowpowered articulated vehicles often give exceptionally good fuel economy at the expense of performance, but there appears to be an increasing realization that this does not necessarily mean. that the overall costs are thereby made lower. The small, hard-worked engine can be expected to require more frequent overhaul, giving rise both to increased maintenance costs and loss of capacity of the vehicle. Increasing interest in faster vehicles is also tending to favour the use of more powerful engines. The characteristics of the type of engine best suited to use on tractive units are the subject of some controversy, quite apart from how powerful the engine should be. One school of thought favours the last-revving, relatively smallcapacity unit on the grounds that its flexibility is valuable in helping to reduce the need for frequent gear changing on varying gradients. The other considers that a larger unit with deliberately restricted upper r.p.rn. limit is more likely to he trouble-free under the continuous slogging often associated with the operation of this kind of vehicle. To some extent both viewpoints relate more especially to the lower-powered vehicle. Robust Transmission Required Even if the engine normally used in a 14-ton-gross rigid four-wheeler' is employed in a 24-ton articulated vehicle, the transmission -designed for the smaller machine cannot have the same factor of safety under normal use if it is employed in the heavier one. This is because the small engine will inevitably have to work harder •in view of the increased weight. The stress on clutch, gearbox, propeller shaft and final drive components depends on the resistance to rotation of the road wheels, which is roughly proportional to the weight, as well as the input to these components from the engine. This is not to say that transmission components designed primarily for a 14-ton vehicle will necessarily fail when used in a 24-tonner, but their expectation of life is likely to be reduced somewhat unless the original design is particularly robust. On the other hand, unduly heavy units are likely to be expensive as well as causing a reduction in the maximum legal payload. ginjilar remarks apply to the cooling system, and a low-powered vehicle liable to take a longer time to climb hills may require a greater reserve of cooling capacity than one with a more powerful engine, despite the latter's greater potential output of waste heat. But if the tractive unit's engine, transmission and associated items should ideally be similar to those of a rigid chassis intended for operation at the same gross laden weight, quite different considerations apply to much of the remainder of the design. In terms of static loading, it might at first appear that the frame, axles and associated parts could be similar to those of a load-carrying model with a similar laden weight to that supported by the tractive unit's tyres. On a 24-tongross outfit, this might be a 12-ton-gross vehicle, for example. In fact, largely because of the severe weight transfer effect under braking, this would not be adequate in all respects. None the less, the tractive-unit frame is generally subject to appreciably lower bending moments than that of an equivalent load-carrying model. Two factors account for this, one being the short wheelbase and the other the support of the imposed semi-trailer weight at a point almost directly above the rear axle. Even when braking causes the thrust from the semi-trailer to have a forward component, its line of action is rarely far from the front brackets of the tractive unit's rear springs. Side-member PrOfile Although the frame of a 24-ton-gross rigid eight-wheeler is not subject to unduly severe bending moments, because of the well-spaced points of support given by the spring brackets of a four-axle chassis, the tractive-unit frame side-members of a corresponding articulated outfit can generally be of reduced section. Some manufacturers prefer to retain the standard side-member profile for reasons of standardization, in which case some reduction of thickness could generally be permitted. There are practical limits to the use of thin-section material, however, because of the increased need for flitch plates at the points of attachment of any item putting appreciable stresses on the frame. From a design point of view a preferable method would probably be to reduce the depth of the side-members. Whichever means is adopted, the weight saving is not likely to be large, as the complete frame assembly of a typical tractive unit for operation at 24 tons gross weighs less than 8 cwt. with quite substantial sidemembers. A comparatively shallow frame may be required to reduce the height of the fifth wheel, however, whilst it can also improve engine accessibility. Braking is perhaps the most complex aspect of tractive unit design and the most affected by the characteristics of the semi-trailer. By its nature, a semi-trailer cannot be selfcontained in terms of the proportion of braking applied to its own wheels, except for low rates of retardation. Over a third of the weight of the semi-trailer and full payload is usually supported by the tractive unit and this proportion is increased by the load transfer effect when braking. It follows that an appreciable part of the horizontal braking force for the semi-trailer is supplied via the fifthwheel king-pin. Calculations made by a former colleague when the writer was on the design staff of a well-known chassis manufacturer indicated that this force could amount to some 44 tons on a typical 24-ton-gross outfit braking at 18 ft. per sec. per sec. (0.56g.), as compared with just over 6 tons applied at the semi-trailer wheels. The figure was based on the assumption that the braking would be split in the proportion of 271 per cent. on the tractive unit front axle, 271 per cent. on the tractive unit rear axle and 45 per cent, on the semi-trailer wheels. Static laden weights of 34 tons, 8 tons and 12,1 tons respectively become 64tons, 64tons and 11 tons respectively under braking of this not particularly severe degree. In other words the front axle loading is increased by 80 per cent. when braking. Over-braking a Problem Under these conditions, the example quoted would have a margin of adhesion on all wheels on a dry road, but the difficulty of brake design on articulated vehicles is underlined when braking of the same outfit in unladen form is considered. With weights carried by the tractive-unit rear axle and the semi-trailer axles reduced to just over 2+ tons in each case, whilst the front axle load is only slightly reduced at approximately 3 tons, the problem of overbraking all but the front wheels becomes critical. With unaltered brake proportioning, both the tractive unit rear axle wheels and the semi-trailer wheels would lock at just under 16 ft. per sec. per sec. (0.5g.) retardation on dry roads. Coupling the same tractive unit to another semi-trailer having different braking characteristics, or even merely different dimensions, particularly in regard to its centre of 'gravity, would 'produce different braking performance. In all cases, however, the load transfer on to the front axle of the tractive -unit is considerable, and unless the axle is ,specially strengthened for the purpose it is not always possible to equip it with sufficiently powerful brakes to take full :advantage of the high. adhesion available. The severe load-transfer effect on braking complicates the problem of providing satisfactory tractive-unit suspension, in itself inevitably somewhat difficult because of the short wheelbase. The small amount of payload carried by the front axle makes the use of softer front springs than are fitted to equivalent load-carrying models desirable to avoid a " choppy" ride, whilst dampers often become essential rather than merely desirable. On the other hand, under braking the front suspension is subjected temporarily to a much higher loading, as well as having to withstand severe torque reaction effects. A simple solution to the first problem is the use of auxiliary rubber springs, whilst with orthodox suspension the second implies the use of springs with heavy-section top plates and reinforced eyes. The relatively light front-axle loading means that, except in the heaviest classes, power-assisted steering can be regarded as something of a luxury on a tractive unit. Moreover, its shortwheelbase means that lower-geared steering can be adopted without making it unduly difficult to negotiate corners at a reasonable speed. Possibilities in the Future Turning to future prospects, it does not seem unreasonable to envisage a minimum power/weight ratio of 10 b.h.p. per ton, fully laden, becoming usual in a few years' time. Although this would call for a 240 b.h.p. engine in a 24-tongross outfit, it would merely bring the performance up to the standard attainable by many present-day double-deck buses. The pressing need under modern traffic conditions is for an improvement in hill-climbing performance. One British manufacturer already has in regular production a tractive unit of power only slightly below the suggested figure, and there seems no reason why others should not follow, • The idea of.applying automatic or semi-automatic transmission to tractive units, or.for that matter goods vehicles in general, seems as remote now as it was 20 years ago, except for the very largest vehicles or for specialized conditions. Synchromesh mechanism appears to have limited appeal on heavy goods vehicles and development seems more likely to follow American practice where multi-speed close-ratio gearboxes of orthodox constant-mesh types • have become widely favoured. The most obvious need with regard to tractive-unit brakes is the development of a simple and reliable means of automatically adjusting the proportion of braking applied to each axle according to the load it is actually carrying at the time. The choice of disc or drum brakes is, by comparison, probably somewhat academic as yet, since the most pressing problem is more the question of preventing premature locking of some of the wheels under variable conditions than brake efficiency in itself. Freedom from fade is, however, likely to become increasingly important as speeds increase. Although manufacturers of heavy commercial vehicles are probably justified in their general reluctance to depart • from the well-tried, simPle and reliable suspension system employing beam axles and laminated springs, tractive units present problems which might yield to a less orthodox approach. The use of radius arms to relieve the front springs of braking stresses is one relatively modest change that might provide useful results, whilst air or rubber suspension might provide a convenient form of variablerate effect Abandonment of the rigid beam axle in favour of independent front suspension would undoubtedly give a better ride because of the reduction of unsprung weight. Whether it could be achieved economically,' especially if the parts were to be peculiar to one -model,. is doubtful. Surprisingly good results 'can be obtained from orthodox • beam axle suspension with a static laden spring deflection of not less than 3 in. The, general layout Of the tractive unit has become. standardized to a large extent, particularly so far as vehicles operating in this country are concerned. This is undoubtedly influenced by the general acceptance of the S.M.M.T. standard for ,positions and heights of fifth-wheel attachments. Although this allows some latitude, the, limitation of the dimension from centre-line of king-pin to centre-line of rear axle to a maximum of 12 in. on a two. axle model tends to encourage the use of very short wheelbase tractive units, partly because so little' of the imposed weight of the semi-trailer is transmitted to the front wheels. The desirability of landing gear being as far -forward on the semi-trailer as possible is no doubt the reason for this. Nonetheless, Continental practice favours the use of longer tractive units with the fifth-wheel king-pin approximately twice as far forward of the rear axle. The Common Market could cause renewed interest in this subject. A slightly longer tractive-unit wheelbase would simplify the problem of providing satisfactory ride characteristics and allow more room for large-capacity fuel tanks, spare. wheel, etc., without unduly affecting manoeuvrability. In the United States, there has in recent years been an interesting tendency. for some manufacturers to depart from the traditional preference for normal-control vehicles on that side'of the Atlantic. Tractive units are available with ultra-short forward-control cabs to obtain the maximum payload length on the semi-trailer without exceeding the various State overall length limits. . The future of articulated vehicles is clearly a bright one and the design of tractive units seems likely to receive increasing attention in :the -years to come.Tags