Workshop Practice in Production
Page 35
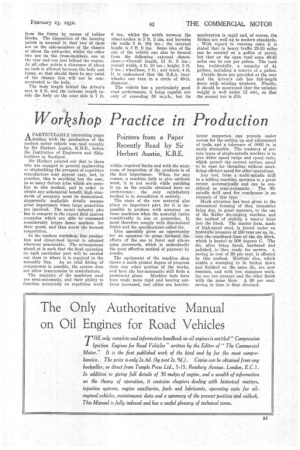
If you've noticed an error in this article please click here to report it so we can fix it.
Pointers from a Paper Recently Read by Sir Herbert Austin, K.B.E.
APARTICULARLX interesting panel' dealing with the Production of the modern motor vehicle was read recently by Sir Herbert Austin, K.II.E., before the Institution of Engineers and Shipbuilders in Scotland.
Sir Herbert pointed out that to those who are engaged in general engineering or shipbuilding the prospect of repetition manufacture may appear easy, but, in practice, this is anything but the ease, as so many factors arise which are peculiar to this method, and in order to obtain any substantial benefit, high standards of accuracy must be maintained. Apparently negligible details assume great importance when large quantities are involved. The motor industry also has to compete in the export field against countries which are able to command considerably larger home markets for their goods, and thus meets the keenest competition.
In the modern workshop, line production and direct-feed layout is adopted wherever practicable. The arrangement aimed at is such that the final operation on each particular part will be carried out close to where it is required in the
assembly line. As no trial fitting of components is possible, the system does not allow inaccuracies in manufacture.
The majority of the machines used are semi-automatic, and their ability to function accurately on repetition work within required limits and with the minimum of inspection of the products is of the first importance. When, for any reason, a machine fails to give uniform work, it is not worth while patching it up, as the results obtained have no permanence ; the only satisfactory method is to recondition it entirely.
The state of the raw material also plays an important part, for it is impossible to produce with accuracy on these machines when the material varies considerably in size or properties. It must therefore comply with dimensional limits and the specifications called for.
Line assembly gives an opportunity for an operator to press forward the efforts of the one in front and allows gang piecework, which is undoubtedly the most effective method of payment by results.
The equipment of the machine shop shows a much greater degree of progress than any other portion of the works, and here the bar-automatic still finds a
prominent place. Machine beds have been made more rigid and bearing surfaces increased, tool slides are heavier,
better supported ana provide easier access for the setting up and adjustment of tools, and a tolerance of .0005 in. is easily attainable. The tendency of certain types of single-spindle machine is to give wider speed range and speed ratio, which permit the correct surface speed to be used for threading without sacrificing efficient speed for other operations.
Any tool, from a multi-spindle drill to a milling machine, operates to a great extent automatically and can be con
sidered as semi-automatic. The 98spindle drill used for crankcases is an example of this type.
Much attention has been given to the eclanomical -forming of dies, economies being due, in great measure, to the use of the Keller die-sinking machine and the method of sinking a master form into the block. The master form, made of high-speed steel, is forced under an ' hydraulic pressure of 150 tons per sq. in., into the machined face of,the die block, which is heated to 900 degrees C. The die, after being faced, hardened and polished, is then ready for service. A saving in cost of 80 per cent is effected by this method. Multiple dies, which enable a stamping to be broken down and finished on the same die, are now common, and with two stompers working one can prepare and the other finish with the same blow. A 60 per cent. saving in time is thus obtained.