'AST SERVICE A 'EATURE OF NEW JSG WORKSHOP
Page 34
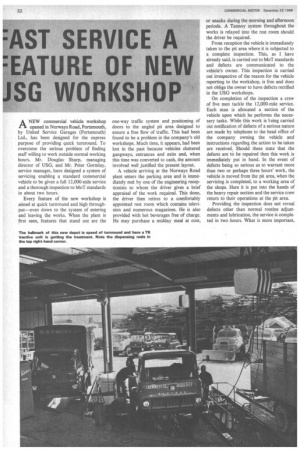
Page 35
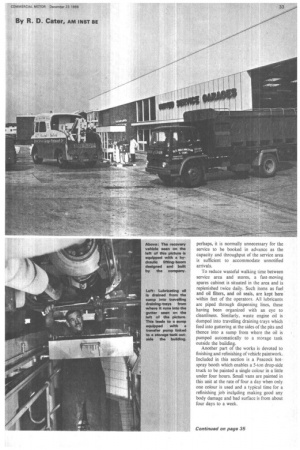
Page 37
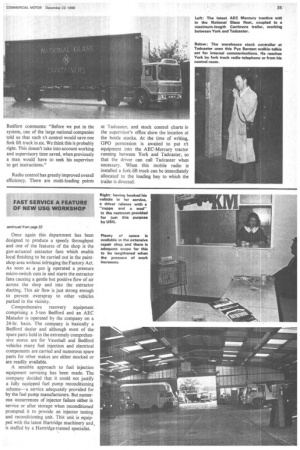
If you've noticed an error in this article please click here to report it so we can fix it.
ANEW commercial vehicle workshop opened in Norways Road, Portsmouth, by United Service Garages (Portsmouth) Ltd., has been designed for the express purpose of providing quick turnround. To overcome the serious problem of finding staff willing to work outside normal working hours, Mr. Douglas Sharp, managing director of USG, and Mr. Peter Gormlay, service manager, have designed a system of servicing enabling a standard commercial vehicle to be given a full 12,000-mile service and a thorough inspection to MoT standards in about two hours.
Every feature of the new workshop is aimed at quick turnround and high throughput—even down to the system of entering and leaving the works. When the plant is first seen, features that stand out are the one-way traffic system and positioning of doors to the angled pit area designed to ensure a free flow of traffic. This had been found to be a problem in the company's old workshops. Much time, it appears, had been lost in the past because vehicles cluttered gangways, entrances and exits and, when this time was converted to cash, the amount involved well justified the present layout.
A vehicle arriving at the Norways Road plant enters the parking area and is immCdiately met by one of the engineering receptionists to whom the driver gives a brief appraisal of the work required. This done, the driver then retires to a comfortably appointed rest room which contains television and numerous magazines. He is also provided with hot beverages free of charge. He may purchase a midday meal at cost, or snacks during the morning and afternoon periods. A Tannoy system throughout the works is relayed into the rest room should the driver be required.
From reception the vehicle is immediately taken to the pit area where it is subjected to a complete inspection. This, as I have already said, is carried out to MoT standards and defects are communicated to the vehicle's owner. This inspection is carried out irrespective of the reason for the vehicle reporting to the workshop, is free and does not oblige the owner to have defects rectified in the USG workshops.
On completion of the inspection a crew of five men tackle the 12,000-mile service. Each man is allocated a section of the vehicle upon which he performs the necessary tasks. While this work is being carried out notification of defects of a serious nature are made by telephone to the head office of the company owning the vehicle and instructions regarding the action to be taken are received. Should these state that the defects are tO be repaired then this work is immediately put in hand. In the event of defects being so serious as to warrant more than two or perhaps three hours' work, the vehicle is moved from the pit area, when the servicing is completed, to a working area of the shops. Here it is put into the hands of the heavy repair section and the service crew return to their operations at the pit area.
Providing the inspection does not reveal defects other than normal routine adjustments and lubrication, the service is completed in two -hours. What is more important, perhaps, it is normally unnecessary for the service to be booked in advance as the capacity and throughput of the service area is sufficient to accommodate unnotified arrivals.
To reduce wasteful walking time between service area and stores, a fast-moving spares cabinet is situated in the area and is replenished twice daily. Such items as fuel and oil filters, and oil seals, are kept here within feet of the operators. All lubricants are piped through dispensing lines, these having been organized with an eye to cleanliness. Similarly, waste engine oil is dumped into travelling draining trays which feed into guttering at the sides of the pits and thence into a sump from where the oil is pumped automatically to a stOrage tank outside the building.
Another part of the works is devoted to finishing and refinishing of vehicle paintwork. Included in this section is a Peacock hotspray booth which enables a 5-ton drop-side truck to be painted a single colour in a little under four hours. Small vans are painted in this unit at the rate of four a day when only one colour is used and a typical time for a refinishing job including making good any body damage and bad surface is from about four days to a week. Once again this department has been designed to produce a speedy throughput and one of the features of the shop is the gun-actuated extractor fans which enable local finishing to be carried out in the paintshop area without infringing the Factory Act. As soon as a gun i operated a pressure micro-switch cuts in and starts the extractor fans causing a gentle but positive flow of air across the shop and into the extractor ducting. This air flow is just strong enough to prevent overspray to other vehicles parked in the vicinity.
Comprehensive recovery equipment comprising a 5-ton Bedford and an AEC Matador is operated by the company on a 24-hr. basis. The company is basically a Bedford dealer and although most of the Spare parts held in the extremely comprehensive stores are for Vauxhall and Bedford vehicles many fuel injection and electrical components are carried and numerous spare parts for other makes are either stocked or are readily available.
A sensible approach to fuel injection • equipment servicing has been made. The company decided that it could not justify a fully equipped fuel pump reconditioning scheme—a service adequately provided for by the fuel pump manufacturers. But numerous occurrences of injector failure either in service or after storage when reconditioned prompted it to provide an injector testing and reconditioning unit. This unit is equipped with the latest Hartridge machinery and, is staffed by a Hartridge-trained specialist.