Engine Overhauls Round the Clock
Page 57
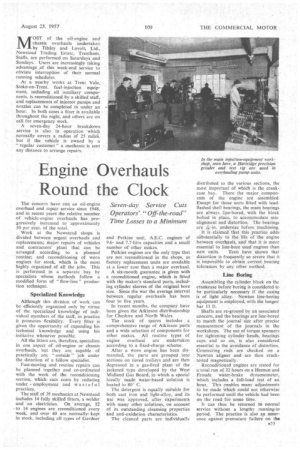
Page 58
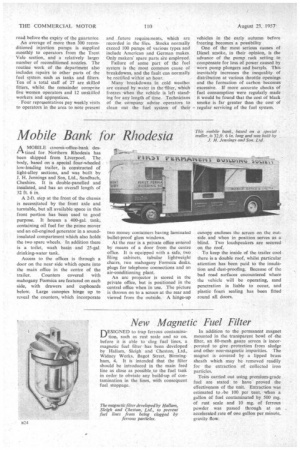
If you've noticed an error in this article please click here to report it so we can fix it.
MOST of the oil-engine and -chassis overhauls undertaken by Tilsley and Lovatt, Ltd., Newstead Trading Estate, Trentham, Staffs, are performed on Saturdays and Sundays. Users are increasingly taking advantage of this week-end service to obviate interruption of their normal
running schedules. .
At a nearby works at Trent Vale, Stoke-on-Trent, fuel-injection equipment, including all auxiliary components, is reconditioned, by a skilled staff,. and replacements of injector pumps and nozzles can be completed in under an .hour. In both cases a fitter is available • throughout the night, and others are on call for emergency work.
A seven-day 24-hour breakdown service is also in operation which normally covers a radius of 25 miles, but if the vehicle is owned by a "regular customer" a mechanic is sent any distance to arrange repairs.
The concern have run an oil-engine overhaul and repair service since 1948, and in recent years the relative number of vehicle-engine overhauls has progressively increased to approximately 50 per cent. of the total.
Work at the Newstead shops is divided between urgent overhauls and replacements; major repairs of vehicles and contractors' plant that can be arranged according to a planned routine; and reconditioning of worn engines for stock, which is the most highly organized of all the jobs. This is performed in a separate bay by specialists whose methods follow a modified form of " flow-line " production technique.
Specialized Knowledge
Although this division of work can be efficiently organized only by virtue of the specialized knowledge of individual members of the staff, in practice it promotes flexibility. Every fitter is given the opportunity of expanding his technical knowledge and using his initiative whenever possible.
All the fitters are, therefore, specialists in one aspect of oil-engine or chassis overhauls, but they arc capable of practically any "outside" job under the direction' of a fellow specialist.
Fast-moving and routine repairs can be planned together and co-ordinated with the work of the reconditioning section, which cuts costs by reducing under employment and wasteful practices.
The staff of 39 mechanics at Newstead includes 14 fully skilled, fitters, a welder and an electrician. On average, 12 to 14 engines are reconditioned every week, and over 40 are normally. kept in stock, including all types of Gardner
and Perkins unit, A.E.C. engines of 9.6and 7.7-litre capacities and a small number of other makes.
Perkins engines are the only type that are not reconditioned in the shops, as factory replacement units are available at a lower cost than a major overhaul.
A six-month guarantee is given with a reconditioned engine, which is fitted with the maker's standard parts, including cylinder sleeves of the original bore size. Since the war the average interval between regular overhauls has been four to five years.
In recent months, the company have been given the Atkinson distributorship for Cheshire and North Wales.
The stock of spares includes a comprehensive range of Atkinson parts and a wide selection of components for other makes. All routine types of engine overhaul are undertaken according to a fixed-charge scheme.
After a worn engine has been dismantled, the parts are grouped into sections on tiered trolleys and arc then degreased in a gas-fired plant of the jacketed type developed by the West Midland Gas Board, in which a special locally made Water-based solution is heated to 80° C.
The detergent is equally suitable for both cast iron and light-alloy, and its use was approved, after experiments with many other solutions, on account of its outstanding cleansing properties and anti-oxidation characteristics.
The cleaned parts are individually
distributed to the various sections, the most important of which is the crankcase bay. There the major, components of the engine are assembled Except for those units fitted with leadflashed shell bearings, the main bearings are always lire-bored, with the block bolted in place, to accommodate misalignment and distortion. The bearings are -h-in. undersize before machining.
It is claimed that this practice adds substantially to the life of the engine between overhauls, and that it is more essential' to line-bore used engines than new units. Tests have shown that distortion is frequently so severe that it is impossible to obtain correct bearing tolerances by any other method.
Line Boring Assembling the cylinder block on the crankcase before 'boring is considered to be particularly necessary if the casing is of light alloy. Newton line-boring equipment is employed, with the longes' bar 11 ft.
Shafts are re-ground by an associated concern, and the bearings are line-bored to match the journal size after precise measurement of the journals in the workshops. The use of torque spanners for tightening cylinder heads, bearings caps and so on, is also considered essential to the avoidance of distortion. Connecting rods are checked on a Newton aligner and are then cracktested magnetically.
Reconditioned engines are tested for a•total run of 32 hours on a Heenan and Froude water-brake dynamometer, which includes a full-load test of an hour. This enables many adjustments to be made Which could not otherwise be performed until the vehicle had been on the road for some time.
It can thus be returned to normal service without a lengthy running-in period. The practice is also an assurance against premature failure on the
road before the expiry of the guarantee.
An average of more than 300 reconditioned injection pumps is supplied monthly to operators from the Trent Vale section, and a relatively large' number of reconditioned nozzles. The routine work of the department also includes repairs to other parts of the fuel system such as tanks and filters. Ten of a total staff of 27 are skilled fitters, whilst the remainder comprise five women operators and 12 unskilled workers and apprentices.
Four representatives pay weekly visits to operators in the area to note present and future requirements, which are recorded in the files. Stocks normally exceed 100 pumps of various types and include American and German makes. Only makers spare parts are employed.
Failure of some part of the fuel system is the most Common cause of breakdowns, and the fault can normally be rectified within an hour.
Many breakdowns in cold weathei are caused by water in the 'filter, which freezes when the vehicle is left standinglor any length of time. Technicians of the company advise operators to clean out the fuel system of their
vehicles in the early autumn before freezing becomes a possibility One of the most serious causes of Diesel smoke, in their opinion, is the advance of the pump rack setting to. compensate for loss of power caused by worn pump plungers and barrels. This inevitably increases the inequality, of distribution at various throttle openings and the formation of carbon becomes excessive. If more accurate checks of fuel consumption were regularly made it would be found that the cost of black smoke is far greater than the cost of regular servicing of the fuel system.