From Aircraft to Bus Bodies
Page 31
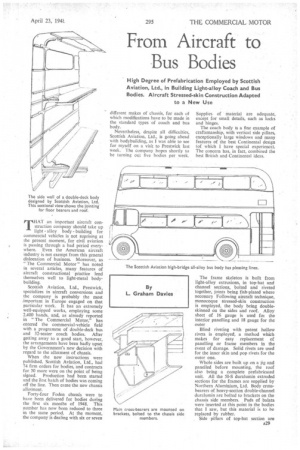
Page 32
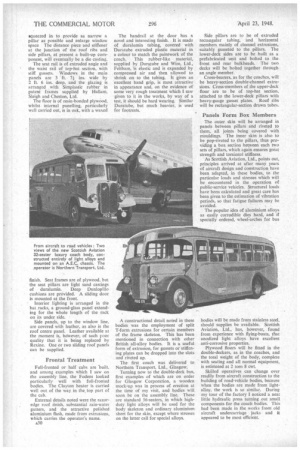
If you've noticed an error in this article please click here to report it so we can fix it.
THAT an important aircraft construction company should take up light alloy body building for commercial vehicles is not suprising at the present moment, for civil aviation is passing through a bad period everywhere. Even the American aircraft industry is not exempt from this general dislocation of business. Moreover, as "The Commercial Motor" has noted in several articles, many features of aircraft constructional practice lend themselves well to light-metal bodybuilding.
Scottish Aviation, Ltd., Prestwick, specializes in aircraft conversions and the company is probably the most .important in Europe engaged on that particular work. It has an extremely well-equipped works, employing some 2,400 hands, and, as already reported in "The Commercial Motor," has entered the commercial-vehicle field with a programme of double-deck bus and 32-seater coach bodies. After getting away to a good start, however, the arrangements have been badly upset by the Government's new decision with regard to the allotment of chassis.
When the new instructions were published, Scottish Aviation, Ltd., had 74 firm orders for bodies, and contracts for 30 more were on the point of being signed. Production had been started and the 'first batch of bodies was coming off the line. Then came the new chassis allotment.
Forty-four Foden chassis were to have been delivered for bodies during the first six months of 1948. This number has now been reduced to three in the same period. At the moment, the company is dealing with six or seven different makes of chassis, for each of which modifications have to be made in the standard types of coach and bus body.
Nevertheless, despite all difficuhies, Scottish Aviation, Ltd., is going ahead with bodybuilding, as I was able to see for myself on a visit to Prestwick last week. The company hopes shortly to be turning out five bodies per week. Supplies of Material are adequate, except for small details, such as locks and hinges.
The coach body is a fine example of craftsmanship, with vertical side pillars, exceptionally large windows and many features of the best Continental design (of which I have special experience). The concern has, in fact, combined the best British and Continental ideas.
The frame skeleton is built from light-alloy extrusions, in top-hat and channel sections, bolted and riveted together, joints being fish-plated where necessary Following aircraft technique, monocoque stressed-skin construction is employed, the body being doubleskinned on the sides and roof. Alloy sheet of 16 gauge is used for the interior panelling and 18 gauge for the Outer Blind riveting whh patent hollow rivets is employed, a method which makes for easy replacement of panelling or frame members in the event of damage. Solid rivets are used for the inner skin and pop rivets for the outer one.
Whole sides are built up on a jig and panelled before mounting, the roof also being a complete prefabricated unit. All the 5I-S duralumin extruded sections for the frames are supplied by Northern Aluminium, Ltd. Body crossbearers of heavy-section double-channel duralumin are bolted to brackets on the chassis side members. Pads of balata were inserted at this point in the bodies that I saw, but this material is to be replaced by rubber. Side pillars of top-hat section are A29
squeezed in to provide as narrow a pillar as possible and enlarge window space The distance piece and stiffener at the junction of the roof ribs and side pillars, at present a built-up corn-ponent, will eventually be a die casting.
The seat rail is of extruded angle and the waist rail of top-hat section, with stiff gussets. Windows in the main panels are 3 ft. 71 ins, wide by 2 ft. 6 ins, deep, and the glazing is arranged with Simplastic rubber in patent frames supplied by Hallam. Sleigh and Cheston, Ltd.
The floor is of resin-bonded plywood. whilst internal panelling, particularly well carried out, is in oak, with a waxed finish. Seat frames are of plywood, but the seat pillars are light sand castings of duralumin. Deep Dunlopillo cushions are provided. A sliding door is mounted at the front.
Interior lighting is arranged in the hat .racks, a ground-glass panel extending for the whole length of the rack on its under side.
Side panels, up to the window line, are covered with leather, as also is the roof centre panel. Leather available at the moment is, however, of such roor quality that it is being replaced by Rexine. One or two sliding roof panels can be supplied.
Frontal Treatment
Full-fronted or half cabs are 'built, and among examples which I saw on the assembly line, the Fodens looked particularly well with full-fronted bodies. The Clayton heater is carried well out of the way in the, top part of the cab.
External details noted were the razoredge roof finish, substantial rain-water gutters, and the attractive polished aluminium flash. made from extrusions, which carries the operator's name.
A30 The handrail at the door has a novel and interesting finish. It is made of duralumin tubing, covered with Duratube extruded plastic material in a colour to match the paintwork of the coach. This rubber-like material, supplied by Duratube and Wire, Ltd , Feltham, is elastic and is expanded by compressed air and then allowed to shrink on to the tubing. It gives an excellent hand grip, is most attractive in appearance and, on the evidence of some very rough treatment which I saw given to it in the works, by way of a test, it should be hard wearing. Similar Duratube, but much heavier, is used for footrests.
A constructional detail noted in these bodies was the employment of split T-form extrusions for certain members of the frame skeleton. This has been mentioned in connection with other British all-alloy bodies. It is a useful form of extrusion, for gussets or stiffening plates can be dropped into the slots and riVeted up. .
The first coach was delivered to Northern Transport, Ltd., Glasgow.
Turning now to the double-deck bus, first examples of which are on order for Glasgow Corporation, a wooden mock-up was in process of erection at the time of my visit, and bodies will soon be on the assembly. line. These are standard 56-seaters, in which high. duty light alloys will be used for the body skeleton and ordinary aluminium sheet for the skin, except where stresses on the latter call for special alloys.
Side pillars are to be of extruded rectangular tubing, and horizontal members mainly of channel extrusions, suitably gusseted to the pillars. The lower-deck sides are to be built as a prefabricated unit and bolted to the front and rear bulkheads. The two decks will be bolted together throughan angle member.
Cross-bearers, as for the coaches, will be heavy-section double-channel extrusions. Cross-members of the upper-deck floor are to be of top-hat section, attached to the lower-deck pillars with heavy-gauge gusset plates. Roof ribs will be rectangular-section drawn tubes.
Panels Form Box Members
The outer skin will be arranged in panels between pillars and riveted to them, all joints being covered with mouldings. The inner skin is also to be pop-riveted to the pillars, thus providing a box section between each two sets of pillars, which again ensures great strength and torsional stiffness.
As Scottish Aviation, Ltd., points out, principles arrived at after many years of aircraft design and construction have been adapted, in these bodies, to the particular loads and stresses which will be encountered in the operation of public-service vehicles. Structural loads have been calculated and great care has been given to the estimation of vibration periods, so that fatigue failures may be avoided.
The popular idea of aluminium alloys as easily corrodible dies hard, and if specially ordered, wheel-arches for bus bodies will be made from stainless steel, should supplies be available. Scottish Aviation, Ltd., has, however, found from experience with flying-boats, that anodized light alloys have excellent anti-corrosive properties.
Plywood floors will be fitted in the double-deckers, as in the coaches, and the total weight of the body, complete with seating and all normal equipment, is estimated at 2 tons 8 cwt.
Skilled operatives can change over readily from aircraft construction to the building of road-vehicle bodies, because when the bodies are made from lightalloy, the work is so similar. During my tour of the factory I noticed a neat little hydraulic press turning out small components for the coach bodies. This had been made in the works from old aircraft undercarriage jacks and it appeared to be most efficient.