EVERYTHING IN ITS PLACE
Page 29
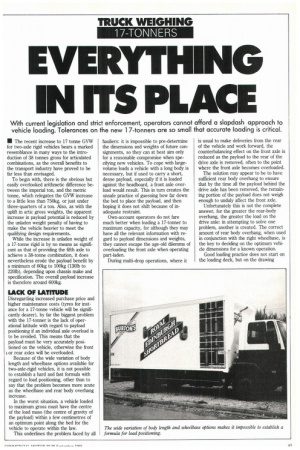
Page 30
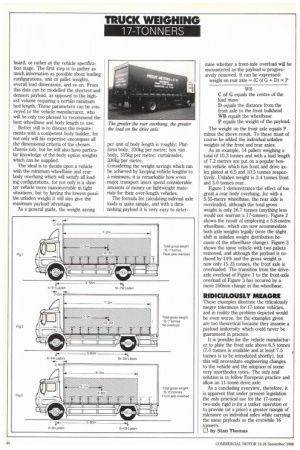
If you've noticed an error in this article please click here to report it so we can fix it.
With current legislation and strict enforcement, operators cannot afford a slapdash approach to vehicle loading. Tolerances on the new 17-tonners are so small that accurate loading is critical.
• The recent increase to 17 tonne GVW for two-axle riOd vehicles bears a marked resemblance in many ways to the introduction of 38 tonnes gross for articulated combinations, as the overall benefits to the transport industry have proved to be far less than envisaged.
To begin with, there is the obvious but easily overlooked arithmetic difference between the imperial ton, and the metric tonne, which relegates the G'VW increase to a little less than 750kg, or just under three-quarters of a ton. Also, as with the uplift in artic gross weights, the apparent increase in payload potential is reduced by the unladen weight penalty of having to make the vehicle heavier to meet the qualifying design requirements.
While the increase in unladen weight of a 17-tonne rigid is by no means as significant as that of providing the fifth axle to achieve a 38-tonne combination, it does nevertheless erode the payload benefit by a minimum of 60kg to 100kg (1301b to 2201b), depending upon chassis make and specification. The overall payload increase is therefore around 600kg.
LACK OF LATITUDE
Disregarding increased purchase price and higher maintenance costs (tyres for instance for a 17-tonne vehicle will be significantly dearer), by far the biggest problem with the 17-tonner is the lack of operational latitude with regard to payload positioning if an individual axle overload is to be avoided. This means that the payload must be very accurately positioned on the vehicle, otherwise the front ) or rear axles will be overloaded.
Because of the wide variation of body length and wheelbase options available for two-axle-rigid vehicles, it is not possible to establish a hard and fast formula with regard to load positioning, other than to say that the problem becomes more acute as the wheelbase and rear body overhang increase.
In the worst situation, a vehicle loaded to maximum gross must have the centre of the load mass (the centre of gravity of the payload) within a few centimetres of an optimum point along the bed for the vehicle to operate within the law.
This underlines the problem faced by all hauliers: it is impossible to pre-determine the dimensions and weights of future consignments, so they can at best aim only for a reasonable compromise when specifying new vehicles. To cope with largevolume loads a vehicle with a long body is necessary, but if used to carry a short, dense payload, especially if it is loaded against the headboard, a front axle overload would result, This in turn creates the unsafe practice of guessing how far down the bed to place the payload, and then hoping it does not shift because of inadequate restraint.
Own-account operators do not fare much better when loading a 17-tonner to maximum capacity, for although they may have all the relevant information with regard to payload dimensions and weights, they cannot escape the age-old dilemma of overloading the front axle when operating part-laden.
During multi-drop operations, where it is usual to make deliveries from the rear of the vehicle and work forward, the counterbalancing effect on the front axle is reduced as the payload to the rear of the drive axle is removed, often to the point where the front axle becomes overloaded.
The solution may appear to be to have sufficient rear body overhang to ensure that by the time all the payload behind the drive axle has been removed, the remaining portion of the payload does not weigh enough to unduly affect the front axle_ Unfortunately this is not the complete answer, for the greater the rear-body overhang, the greater the load on the drive axle: in attempting to solve one problem, another is created. The correct amount of rear body overhang, when used in conjunction with the right wheelbase, is the key to deciding on the optimum vehicle dimensions for a known operation.
Good loading practice does not start on the loading deck, but on the drawing board, or rather at the vehicle specification stage. The first step is to gather as much information as possible about loading configurations, unit or pallet weights, overall load dimensions, and so on. From this data can be modelled the shortest and densest payload, as opposed to the highest volume requiring a certain minimum bed length. These parameters can be conveyed to the vehicle manufacturer, who will be only too pleased to recommend the best wheelbase and body length to use.
Better still is to discuss the requirements with a competent body builder, for not only will his expertise encompass all the dimensional criteria of the chosen chassis cab, but he will also have particular knowledge of the body option weights which can be supplied.
The ideal is to decide upon a vehicle with the minimum wheelbase and rear body overhang which will satisfy all loading configurations, for not only is a shorter vehicle more manoeuvrable in tight situations, but by having the lowest possible unladen weight it will also give the maximum payload advantage.
As a general guide, the weight saving per unit of body length is roughly: Platform body, 230kg per metre; box van body, 315kg per metre; curtainsider, 330kg per metre.
Considering the weight savings which can be achieved by keeping vehicle lengths to a minimum, it is remarkable how even major transport users spend considerable amounts of money on lightweight materials for their over-length vehicles.
The formula for calculating indivual axle loads is quite simple, and with a diminishing payload it is very easy to deter mine whether a front-axle overload will be encountered as the payload is progressively removed. It can be expressed: weight on rear axle = (C of G + D) x P WE C of G equals the centre of the load mass D equals the distance from the front axle to the front bulkhead WB equals the wheelbase P equals the weight of the payload.
The weight on the front axle equals P minus the above result. To these must of course be added the individual unladen weights of the front and rear axles.
As an example, 14 pallets weighing a total of 10.3 tonnes and with a load length of 7.2 metres are put on a popular boxvan vehicle which has front and drive axles plated at 6.5 and 10.5 tonnes respectively. Unladen weight is 3.4 tonnes front and 3.0 tonnes rear.
Figure 1 demonstrates the effect of too great a rear body overhang, for with a 5.55-metre wheelbase, the rear axle is overloaded, although the total gross weight is only 16.7 tonnes (anything less would not warrant a 17-tonner). Figure 2 shows the result of employing a 5.8-metre wheelbase, which can now accommodate both axle weights legally (note the slight shift in unladen weight distribution because of the wheelbase change). Figure 3 shows the same vehicle with two pallets removed, and although the payload is reduced by 14% and the gross weight is now only 15.23 tonnes, the front axle is overloaded. The transition from the driveaxle overload of Figure 1 to the front-axle overload of Figure 3 has occured by a mere 250mm change in the wheelbase.
RIDICULOUSLY MEAGRE
These examples illustrate the ridiculously megre tolerances for 17-tonne vehicles, and in reality the problem depicted would be even worse, for the examples given are too theoretical because they assume a payload uniformity which could never be guaranteed in practice.
It is possible for the vehicle manufacturer to plate the front axle above 6.5 tonnes (7.0 tonnes is available and at least 7.5 ( tonnes is to be introduced shortly), but this will necessitate engineering changes to the vehicle and the adoption of some very unorthodox tyres. The only real solution is to follow European practice and allow an 11-tonne drive axle.
As a concluding overview, therefore, it is apparent that under present legislation the only practical use for the 17-tonne two-axle rigid is for a tanker operation or to provide (at a price) a greater margin of tolerance on individual axles while carrying the same payloads as the erstwhile 16 tonners.
E I by Stan Thomas