Vehicle mission simulation
Page 187
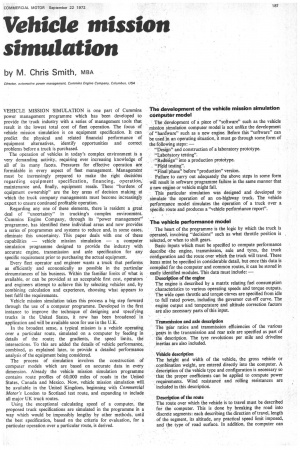
Page 188
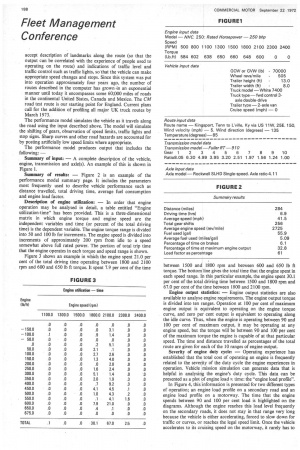
Page 189
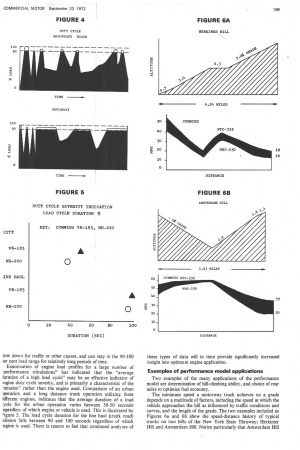
Page 190
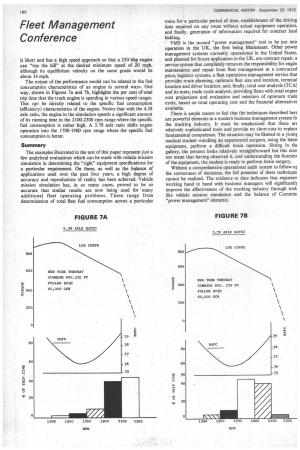
If you've noticed an error in this article please click here to report it so we can fix it.
by M. Chris Smith, MBA
Director, automotive power management, Cummins Engine Company, Columbus, USA
VEHICLE MISSION SIMULATION is one part of Cummins power management programme which has been developed to provide the truck industry with a series of management tools that result in the lowest total cost of fleet operation. The focus of vehicle mission simulation is on equipment specification. It can predict the physical and related financial performance of equipment alternatives, identify opportunities and correct problems before a truck is purchased.
The operation of vehicles in today's complex environment is a• very demanding activity, requiring ever increasing knowledge of all of its many facets. Pressures for effective operation are formidable in every aspect of fleet management. Management must be increasingly prepared to make the right decisions regarding equipment specification, financing, operation; maintenance and, finally, equipment resale. These "burdens of equipment ownership" are the key areas of decision making at which the truck company managements must become increasingly expert to ensure continued profitable operation.
Regarding any one of these elements, there is resident a great deal of "uncertainty" in trucking's complex environment. Cummins Engine Company, through its "power management'' programme, has identified these individual areas and now provides a series of programmes and systems to reduce and, in some cases, eliminate this uncertainty. This paper deals with one of these capabilities — vehicle mission simulation — a computer simulation programme designed to provide the industry with accurate engine, transmission and axle specification for any specific requirement prior to purchasing the actual equipment.
Every fleet operator and engineer wants a truck that performs as efficiently and economically as possible in the particular circumstances of his business. Within the familiar limits of what is available, or can be provided at an acceptable first cost, operators and engineers attempt to achieve this by selecting vehicles and, by combining calculation and experience, choosing what appears to best fulfil the requirements.
Vehicle mission simulation takes this process a big step forward through the use of a computer programme. Developed in the first instance to improve the• technique of designing and specifying trucks in the United States, it now has been broadened in application and will be available soon for use in the U.K.
In the broadest sense, a typical mission is a vehicle operating over a particular route, simulated on a computer by feeding in details of the route; the gradients, the speed limits, the intersections. To this are added the details of vehicle performance, combined, as explained later, to provide a detailed performance analysis of the equipment being considered.
The process of simulation involves the construction of computer models which are based on accurate data in every dimension. Already the vehicle mission simulation programme contains route profiles of 60,000 miles of roads in the United States, Canada and Mexico. Now, vehicle mission simulation wilt be available in the United Kingdom, beginning with Commercial Motor's London to Scotland test route, and expanding to include all major UK truck routes.
Using the exceptional calculating speed of a computer, the proposed truck specifications are simulated in the programme in a way which would be impossibly lengthy by other methods, until the best specification, based on the criteria for evaluation, for A particular operation over a particular route, is derived. The development of the vehicle mission simulation computer model The development of a piece of "software" such as the vehicle mission simulation computer model is not unlike the development of "hardware" such as a new engine. Before this "software" can be used in an operating situation, it must go through some form of the following steps: — "Design" and construction of a laboratory prototype.
• "Labotatory testing".
"RedeSign" into a production prototype.
"Field testing".
"Final phase" before "production" version.
Failure to carry out adequately the above steps in some form will Desult in software programme failure in the same manner that a new engine or vehicle might fail.
This particular simulation was designed and developed to simulate the operation of an on-highway truck. The vehicle performance model simulates the operation of a truck over a specific route and produces a "vehicle perforrnance report".
The vehicle performance model The heart of the programme is the logic by which the truck is operated, involving "decisions" such as what throttle position is selected, or when to shift gears.
Basic inputs which must be specified to compute performance describe the engine, transmission, axle and tyres, the truck configuration and the route over which the truck will travel. These items must be specified in considerable detail, but once this data is compiled for the computer and common routes, it can be stored in easily identified modules. This data must include: — Description of the engine The engine is described by a matrix relating fuel consumption characteristics to various operating speeds and torque outputs. The wide open throttle and torque curves are specified from idle to full rated power, including the governor cut-off curve. The engine output and temperature and altitude correction factors are also necessary parts of this input.
Transmission and axle description The gear ratios and transmission efficiencies of the various gears in the transmission and rear axle are specified as part of the description. The tyre revolutions per mile and driveline inertias are also included.
V6icle description The height and width of the vehicle, the gross vehicle or combination weight, are entered directly into the computer. A description of the vehicle type and configuration is necessary so that the proper coefficients can be applied to compute power requirements. Wind resistance and rolling resistances are included in this description.
Description of the route The route over which the vehicle is to travel must be described for the computer. This is done by breaking the road into discrete segments: each describing the direction of travel, length of the segment, its altitude, any practical speed limit imposed, and the type of road surface. In addition, the computer can accept description of landmarks along the route (so that the output can be correlated with the experience of people used to operating on the route) and indications of traffic level and traffic control such as traffic lights, so'that the vehicle can make appropriate speed changes and stops. Since this system was put into operation approximately four years ago, the number of routes described in the computer has grown in an exponential manner until today it encompasses some 60;000 miles of roads in the continental United States, Canada and Mexico. The CM road test route is our starting point for England. Current plans call for the addition of profiling all major UK truck routes by March 1973.
The performance model simulates the vehicle as it travels along the road using the input described above. The model will simulate the shifting of gears, observation of speed limits, traffic lights and stop signs. Sharp curves and other road hazards are accounted for by posting artificially low speed limits where appropriate.
The performance model produces output that includes the following: Summary of input: A complete description of the vehicle, engine, transmission and axle(s). An example of this is shown in Figure 1.
Summary of results: Figure 2 is an example of the performance model summary page. It includes the parameters most frequently used to describe vehicle performance such as distance travelled, total driving time, average fuel consumption and engine load factor.
Description of engine utilization: In order that engine operation may be analysed in detail, a table entitled "Engine utilization-time" has been provided. This is a three-dimensional matrix in which engine torque and engine speed are the independent variables and time (or percent of the total driving time) is the dependent variable. The engine torque range is divided into 50 and 100 lb for increments. The engine speed is divided into increments of approximately 200 rpm from idle to a speed somewhat above full rated power. The portion of total trip time that the engine operates in each torque and speed range is shown.
Figure 3 shows an example in which the engine spent 21.0 per cent of the total driving time operating between 1800 and 2100 rpm and 600 and 650 lb ft torque. It spent 7.9 per cent of the time
between 1500 and 1800 rpm and between 600 and 650 lb ft torque. The bottom line gives the total time that the engine spent in each speed range. In this particular example, the engine spent 30.1 per cent of the total driving time between 1500 and 1800 rpm and 67.0 per cent of the time between 1800 and 2100 rpm.
Engine output statistics: Engine output statistics are also available to analyse engine requirements. The engine output torque is divided into ten ranges. Operation at 100 per cent of maximum engine output is equivalent to operating on the engine torque curve, and zero per cent output is equivalent to operating along the idle curve. Thus, when the engine is operating between 90 and 100 per cent of maximum output, it may be operating at any engine speed, but the torque will be between 90 and 100 per cent of the maximum torque the engine is capable of at that particular speed. The time and distance travelled as percentages of the total route are given for each of the 10 ranges of engine output.
Severity of engine duty cycle: Operating experience has established that the total cost of operating an engine is frequently related to the severity of the duty cycle the engine experiences in operation. Vehicle Imission simulation can generate data that is helpful in analysing the engine's duty cycle. This data can be presented as a plot of engine load v. time: the "engine load profile".
In Figure 4, this information is presented for two different types of operation; an engine load profile on a secondary road and an engine load profile on a motorway. The time that the engine spends between 90 and 100 per cent load is highlighted on the diagrams. Although the engine reaches this load level frequently on the secondary roads, it does not stay in that range very long because the vehicle is either accelerating, forced to slow down for traffic or curves, or reaches the legal speed limit. Once the vehicle accelerates to its cruising speed on the motorway, it rarely has to low down for traffic or other causes, and can stay in the 90-100 )er cent load range for relatively long periods of time.
Examination of engine load profiles for a large number of 'performance simulations" has indicated that the "average luration of a high load cycle" may be an effective indicator of :ngine duty cycle severity, and is primarily a characteristic of the 'mission" rather than the engine used. Comparison of an urban
■ peration and a long distance trunk operation utilizing three lifferent engines, indicates that the average duration of a load :ycle for the urban operation varies between 30-50 seconds egardless of which engine or vehicle is used. This is illustrated by 7igure 5. The load cycle duration for the line haul (trunk road) nission falls between 90 and 100 seconds regardless of which ngine is used. There is reason to feel that continued analyses of
these types of data will in time provide significantly increased insight into optimum engine application.
Examples of performance model applications
Two examples of the many applications of the performance model are determination of hill-climbing ability, and choice of rear axles to optimize fuel economy.
The minimum speed a motorway truck achieves on a grade depends on a multitude of factors, including the speed at which the vehicle approaches the hill as influenced by traffic conditions and curves, and the length of the grade. The two examples included as Figures 6a and 6b show the speed-distance history of typical trucks on two hills of the New York State Thruway; Herkimer Hill and Amsterdam Hill. Notice particularly that Amsterdam Hill
is—short and has a high speed approach so that a 250 bhp engine can "top the hill" at the desired minimum speed of 20 mph, although its equilibrium velocity on the same grade would be about 14 mph.
The output of the performance model can be related to the fuel consumption characteristics of an engine in several ways. One way, shown in Figures 7a and 7b, highlights the per cent of total trip time that the truck engine is spending in various speed ranges. This can be directly related to the specific fuel consumption (efficiency) characteristics of the engine. Notice that with the 4.38 axle ratio, the engine in the simulation spends a significant amount of its running time in the 2100-2300 rpm range where the specific fuel consumption is rather high, A 3.70 axle ratio shifts engine operation into the 1700-1900 rpm range where the specific fuel consumption is better.
Summary
The examples illustrated in the text of this paper represent just a few analytical evaluations which can be made with vehicle Mission simulation in determining the "right" equipment specifications for a particular requirement. On these, as well as the balance of applications used over the past four years, a high degree of accuracy and reproduction of reality has been achieved. Vehicle mission simulation has, in so many cases, proved to be so accurate that similar results are now being used for many additional fleet operating problems. These range from determination of total fleet fuel consumption across a particular
route for a particular -period of time, establishment of the driving time required on any route without actual equipment operation, and finally, generation of information required for contract haul bidding.
VMS is the second "power management" tool to be put into operation in the UK, the first being Mainsteam. Other power management systems currently operational in the United States, and planned for future application in the UK, are contract repair, a service system that completely removes the responsibility for engin( maintenance and repair from fleet management at a contracted price, logistics systems, a fleet operations management service that provides route planning, optimum fleet size and location, terminal location and driver location; and, finally, total cost analysis (TCA) and its mate, trade cycle analysis, providing fleets with total engine cost projections and evaluation and selection of optimum trade cycle, based on total operating cost and the financial alternatives available.
There is ample reason to feel that the techniques described here are powerful elements in a modern business management system fo the trucking industry. It must be emphasized that these are relatively sophisticated tools and provide no short-cuts to replace fundamental competence. The situation may be likened to a young medical student watching an experienced surgeon, using the latesi equipment, perform a difficult brain operation. Sitting in the gallery, the process looks relatively straightforward but this does not mean that having observed it, and understanding the functior of the equipment, the student is ready to perform brain surgery.
Without a comprehensive operational audit system to follow-ur the correctness of decisions, the full potential of these techniques cannot be realized. The evidence to date indicates that engineers working hand in hand with business managers will significant13 improve the effectiveness of the trucking industry through tools like vehicle mission simulation and the balance of Cummins "power management" elements.