Prototype glassfibre chassis by Messerschmitt
Page 31
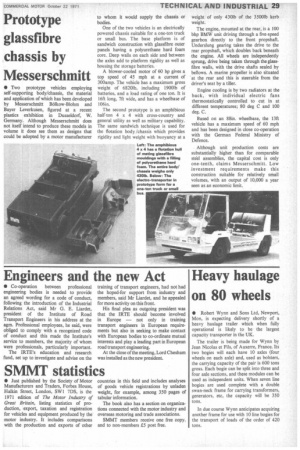
If you've noticed an error in this article please click here to report it so we can fix it.
• Two prototype vehicles employing self-supporting body/chassis, the material and application of which has been developed by Messerschrnitt BOlkow-Blohm and Bayer Leverkusen, figured at a recent plastics exhibition in Dusseldorf, W. Germany. Although Messerschmitt does not itself intend to produce these models in volume it does see them as designs that could be adopted by a motor manufacturer to whom it would supply the chassis or bodies.
One of the two vehicles is an electrically powered chassis suitable for a one-ton truck or small bus. The base platform is of sandwich construction with glassfibre outer panels having a polyurethane hard foam core. Deep walls on each side and between the axles add to platform rigidity as well as housing the storage batteries.
A blower-cooled motor of 60 hp gives a top speed of 45 mph at a current of 300 amp. The vehicle has a maximum gross weight of 68201b, including 19001b of batteries, and a load rating of one ton. It is 16ft long, 7ft wide, and has a wheelbase of 106i n.
The second prototype is an amphibious halfton 4 x 4 with cross-country and general utility as well as military capability. The same sandwich technique is used for the flotation body /chassis which provides rigidity and light weight with buoyancy at a weight of only 4301b of the 35001b kerb weight.
The engine, mounted at the rear, is a 100 bhp BMW unit driving through a five-speed gearbox directly to the front propshaft. Underslung gearing takes the drive to the rear propshaft, which doubles back beneath the engine. All wheels are independently sprung, drive being taken through the glassfibre walls, with the drive shafts sealed by ,bellows. A marine propeller is also situated at the rear and this is steerable from the driver's seat by a tiller.
Engine cooling is by two radiators at the back, with individual electric fans thermostatically controlled to cut in at different temperatures; 80 deg C and 100 deg. C.
Based on an 88in. wheelbase, the 13ft vehicle has a maximum speed of 60 mph and has been designed in close co-operation with the German Federal Ministry of Defence.
Although unit production costs are substantially higher than for comparable stiel assemblies, the capital cost is only one-tenth, claims Messerschmitt. Low investment requirements make this construction suitable for relatively siball volumes, with an output of 10,000 a year seen as an economic limit.