A stranger in Burns country
Page 64
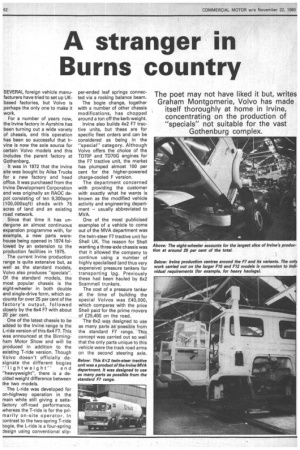
Page 67
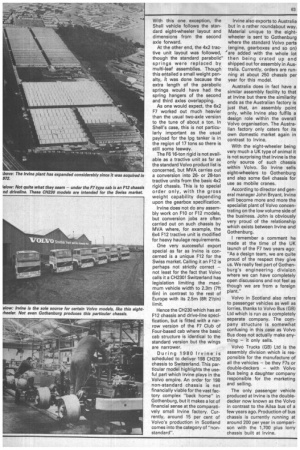
If you've noticed an error in this article please click here to report it so we can fix it.
The poet may not have liked it but, writes Graham Montgonnerie, Volvo has made itself thoroughly at home in Irvine, concentrating on the production of "specials" not suitable for the vast Gothenburg complex.
SEVERAL foreign vehicle manufacturers have tried to set up UKbased factories, but Volvo is perhaps the only one to make it work.
For a number of years now, the Irvine factory in Ayrshire has been turning out a wide variety of chassis, and this operation has been so successful that Irvine is now the sole source for certain Volvo models and this includes the parent factory at Gothenberg.
It was in 1972 that the Irvine site was bought by Ailsa Trucks for a new factory and head office. It was purchased from the Irvine Development Corporation and was originally an RAOC depot consisting of ten 9,300sqm (100,000sqft) sheds with 75 acres of land and an existing road network.
Since that time it has undergone an almost continuous expansion programme with, for example, a new parts warehouse being opened in 1974 followed by an extension to the production facilities in 1975.
The current Irvine production range is quite extensive but, as well as the standard models, Volvo also produces "specials". Of the standard models, the most popular chassis is the eight-wheeler in both double and single-drive form, which accounts for over 25 per cent of the factory's output, followed closely by the 6x4 F7 with about 20 per cent.
One of the latest chassis to be added to the Irvine range is the L-ride version of this 6x4 F7. This was announced at the Birmingham Motor Show and will be produced in addition to the existing T-ride version. Though Volvo doesn't officially designate the different bogies "lightweight" and "heavyweight", there is a decided weight difference between the two models.
The L-ride was developed for on-highway operation in the main while still giving a satisfactory off-road performance, whereas the T-ride is for the primarily on-site operator. In contrast to the two-spring T-ride bogie, the L-ride is a four-spring design using conventional slip
per-ended leaf springs connected via a rocking balance beam.
The bogie change, together with a number of other chassis modifications, has chopped around a ton off the kerb weight.
Irvine also builds 4x2 F7 tractive units, but these are for specific fleet orders and can be considered as being in the "special" category. Although Volvo offers the choice of the TD7OF and TD7OG engines for the F7 tractive unit, the market has plumped almost 100 per cent for the higher-powered charge-cooled F version.
The department concerned with providing the customer with exactly what he wants is known as the modified vehicle activity and engineering department — usually abbreviated to MVA.
One of the most publicised examples of a vehicle to come out of the MVA department was the twin-steer F7 tractive unit for Shell UK. The reason for Shell wanting a three-axle chassis was that it allowed the company to continue using a number of highly specialised (and thus very expensive) pressure tankers for transporting lpg. Previously these had been hauled by 6x2 Scammell trunkers.
The cost of a pressure tanker at the time of building the special Volvos was £40,000, which compares with the price Shell paid for the prime movers of £25,400 on the road.
The 6x2 was designed to use as many parts as possible from the standard F7 range. This concept was carried out so well that the only parts unique to this vehicle were the track road arms on the second steering axle. With this one exception, the Shell vehicle follows the standard eight-wheeler layout and dimensions from the second axle forward.
At the other end, the 4x2 tractive unit layout was followed, though the standard parabolic-springs were replaced by multi-leaf assemblies. Though this entailed a small weight penalty, it was done because the extra length of the parabolic springs would have had the spring hangers of the second and third axles overlapping.
As one would expect, the 6x2 F7 worked out much heavier than the usual two-axle version to the tune of about a ton. In Shell's case, this is not particularly important as the usual payload for the lpg tanker is in the region of 17 tons so there is still some leeway.
The F6 16-ton rigid is not available as a tractive unit as far as the standard Volvo product list is concerned, but MVA carries out a conversion into 26or 28-ton tractive units from the basic 4x2 rigid chassis. This is to special order only, with the gross weight capability depending upon the gearbox specification.
Irvine does not do any assembly work on F10 or F12 models, but conversion jobs are often carried out on such chassis by MVA where, for example, the 6x4 F12 tractive unit is modified for heavy haulage requirements.
One very successful export special as far as Irvine is concerned is a unique F12 for the Swiss market. Calling it an F12 is perhaps not strictly correct — not least for the fact that Volvo calls it a CH230! Switzerland has legislation limiting the maximum vehicle width to 2.3m (7ft 6in) in contrast to the rest of Europe with its 2.5m (8ft 21/2in) limit.
Hence the CH230 which has an F12 chassis and drive-line specification, but is fitted with a narrow version of the F7 Club of Four-based cab where the basic cab structure is identical to the standard version but the wings are narrower.
During 1980 Irvine is scheduled to deliver 198 CH230 chassis to Switzerland. This particular model highlights the useful part which Irvine plays in the Volvo empire. An order for 198 non-standard chassis is not financially viable for the vast factory complex "back home" in Gothenburg, but it makes a lot of financial sense at the comparatively small Irvine factory. Currently, around '15 per cent of Volvo's production in Scotland comes into the category of "nonstandard". Irvine also exports to Australia but in a rather roundabout way. Material unique to the eightwheeler is sent to Gothenburg where the standard Volvo parts (engine, gearboxes and so on) are added with the whole lot then being crated up and shipped out for assembly in Australia. Currently, orders are running at about 250 chassis per year for this model.
Australia does in fact have a similar assembly facility to that at Irvine but there the similarity ends as the Australian factory is just that, an assembly point only, while Irvine also fulfils a design role within the overall Volvo organisation. The Australian factory only caters for its own domestic market again in contrast to Irvine.
With the eight-wheeler being very much a UK type of animal it is not surprising that Irvine is the only source of such chassis within Volvo. So Irvine sells eight-wheelers to Gothenburg and also some 6x4 chassis for use as mobile cranes.
According to director and general manager John Bryant, Irvine will become more and more the specialist plant of Volvo concentrating on the low volume side of the business. John is obviously very proud of the relationship which exists between Irvine and Gothenburg.
I remember a comment he made at the time of the UK launch of the F7 two years ago: "As a design team, we are quite proud of the respect they give us. We really feel part of Gothenburg's engineering division where we can have completely open discussions and not feel as though we are from a foreign plant."
Volvo in Scotland also refers to passenger vehicles as well as lorries, thanks to Volvo Bus (GB) Ltd which is run as a completely separate company. The company structure is somewhat confusing in this case as Volvo Bus does not actually make anything — it only sells.
Volvo Trucks (GB) Ltd is the assembly division which is responsible for the manufacture of all the vehicles — be they F7s or double-deckers — with Volvo Bus being a daughter company responsible for the marketing and selling.
The only passenger vehicle produced at Irvine is the doubledecker now known as the Volvo in contrast to the Ailsa bus of a few years ago. Production of bus chassis is currently running at around 200 per year in comparison with the 1,700 plus lorry chassis built at Irvine.